OK, here it goes.
I have a Diggler mountain scooter and a large electric motor (told it was a showscan projector motor). My goal is to build a daily commuter to get to and from work (been a fantasy of mine for 5 yrs, now I want to make it a reality). I ran into a guy who was riding one about 17 miles to work (SF bay area). Anywho, I stopped the guy and he said his friend put together a kit for $700 and he said he could go 40mph and could travel 20-25 miles between charge, this scooter had a hub motor and is way out of my price range. I've spent $100 so far for the scooter and the motor was free, quality parts are important but would really like to keep the costs down as much as poss. I checked online for any hub motors but no luck.
Questions that I have:
1. does this sound like it can be done using the motor that I currently have?
2. due to me not currently having a hub motor and this being a scooter means no rear sprocket, does this mean I have to go with a direct drive spindle system to use this motor? The stock wheel axles are a bit narrower then a standard bmx rear wheel so it doesn't fit between the drop outs, I might be able to widen the rear drop outs somehow but don't want to damage the frame integrity.
Pics of the bike and the motor are at the bottom of this string (motor is just placed on the deck for reference).
Diggler dimentions:
20" BMX wheels with no rear sprocket or freewheel (which I will put road tires on)
front shocks with 2" travel
have v brakes f/r (will get disk brakes cause it will travel 30-40 mph)
I'll go the the electronics store down the street to confirm what the motor draws but here are the motor details on the casing itself:
AMETEK DYNAMICS DIV
P/N 0842-11 SN-001
D.C. VOLTS 28
The motor dimensions are:
L= 4 1/2" (including 4 hole flange)
Diameter of casing= 4 1/8"
4 x bolt holes are 3 3/8" apart from each other
Shaft is 6" long (end to end) and
the motor has one black lead (17 1/2") and one white lead (15 1/2")
I'm having a hard time finding any info at all on this motor but am going to continue looking, if anyone know anything about this motor please let me know.
I found a couple examples of DIY electric digglers which have links included in this string. Whenever anyone has some time please help point me in the right direction, whether it be good books to read on building your own e-scooter or someone who wouldn't mind chatting on the phone. Anything would help since I'm not the best with figuring out electricity (volts, Amps and anything related to electric vehicles).
Thanks
Russ
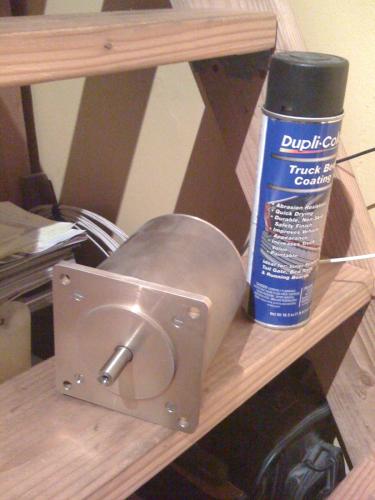
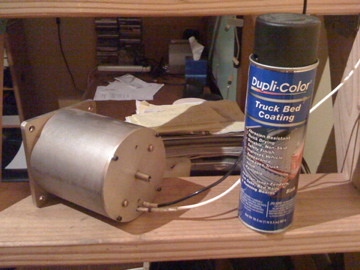
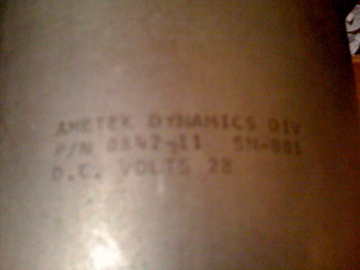
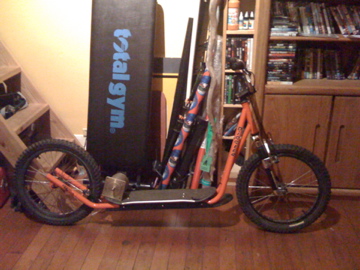
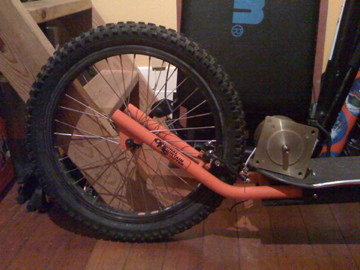
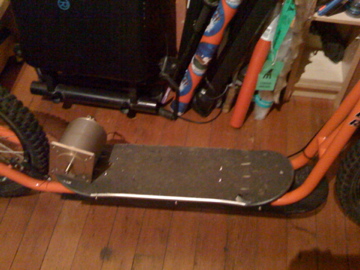
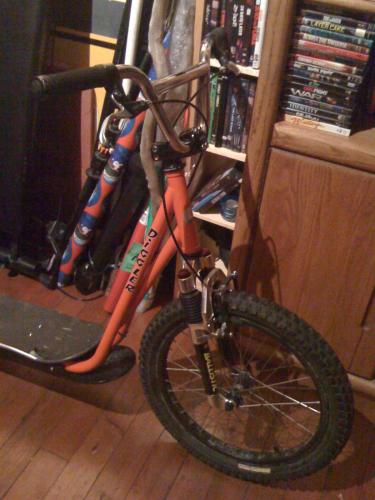
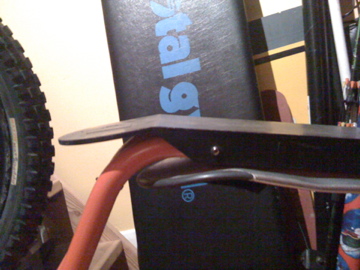