Submitted by jstept on Sat, 03/29/2008 - 23:38
Well, it's been an exciting week. I spent much of last Saturday getting the brakes working, installing the levers, cables, and switches. The brakelight switches install in-line in the brake cables within the headset, so I had to figure out where to cut the cable housings to get them in the right spot.
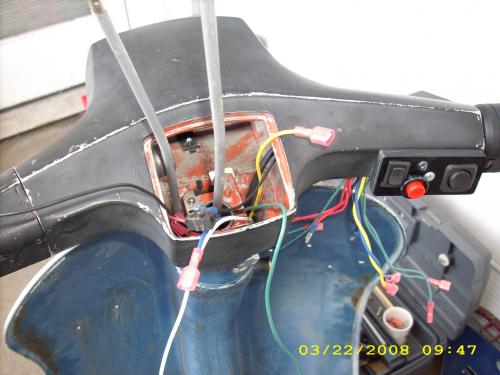
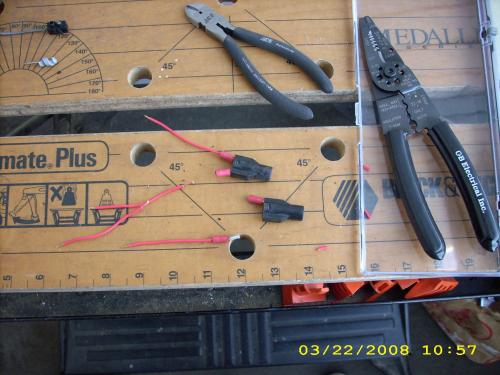
Submitted by zosohawk on Sat, 03/29/2008 - 16:32
I just got this battery sent to me. After reading the instructions and taking the original battery case apart I have no idea what to do. The instructions make absolutely no sense. Has anyone done this yet, and what am I missing?
Thanks in advance,
Mark
Submitted by Ivan on Mon, 03/24/2008 - 05:38
Submitted by reikiman on Thu, 03/20/2008 - 19:14
I rode my Lectra to work today and had the most bizarre ride home.
It started before I took off -- two of my coworkers were in the parking lot having seen the bike and they told me they'd spent the prior 1/2 hour going over all the details of the bike, and saying that Dave (me) would love to see the bike. So when I came towards them wearing a motorcycle jacket they broke into cheers and waving and saying what an awesome bike. Ohmygosh.
Submitted by MattB on Thu, 03/20/2008 - 14:03
My E-Bike experiment started two years ago while recovering from back surgery. I spent lots of money on crazy gadgets that I didn’t need while I was home on disability. Many of the stupid things I bought turned out to be a big waste of money but the E-Bike was not one of them. The E-Bike retrofit kit has turned out to the best purchase that I’ve made for a variety of reasons.
Submitted by strawhistle on Mon, 03/17/2008 - 14:29
Any one out there know how to slow down a controler to 180 cpM ??? a high torque bldc 24" diam at the gap ??
Submitted by jstept on Sun, 03/16/2008 - 23:22
I haven't blogged in a while, but it's not because I haven't been making progress. It's just that when I get free time, I'd rather spend it building than typing and uploading photos. Here's a summary of what I've been doing:
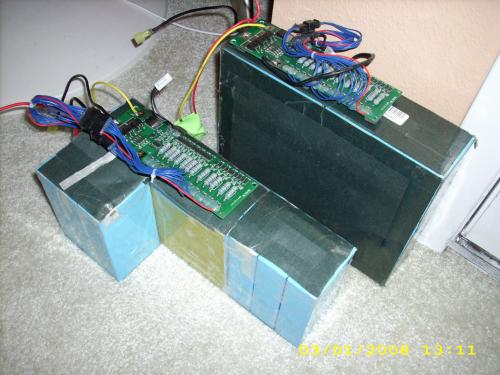
I had to reconfigure LiFeP04 battery pack 1 so it fit better in the space below the seat. This involved cutting the tape that held it together, cutting and resoldering some of the links between the cells, and extending some of the wires to the BMS.
Submitted by reikiman on Sun, 03/16/2008 - 20:14
Today I got the fairing out and tried fitting it to the Lectra. Last week I measured things and drew pictures on paper, but this week it was made a little more real.
First.. this is what the fairing looks like, the picture was taken the day I picked it up. We loaded it on my motorcycle trailer and strapped it down sitting in the rail.
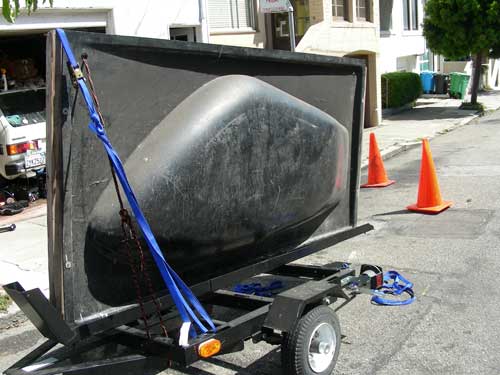
Submitted by strawhistle on Wed, 03/12/2008 - 20:36
can we assembile a list of evs by watts , speed , range type of batt . type of controler and contact address., Support and Service and trust rating etc>> No exclusions ! A way for the newbie to choose his EV and learn the advantages and foibles of each .
Submitted by JCinStaunton on Tue, 03/11/2008 - 18:04
First I have 2 motorcycles. Both are Yamaha 650's that I bought off ebay. I went to ohio for this bike...
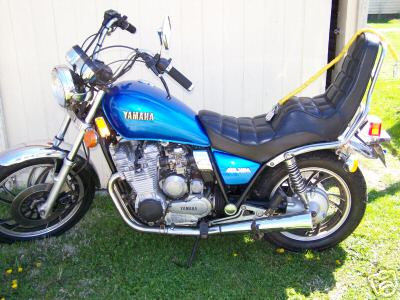
Love the way it looks :) Just had to have it. Only thing needed is the carbs cleaned. They are being done now at the shop.
Went to Ct. for the parts bike. got to visit my brother when I was there and stayed over for the night.
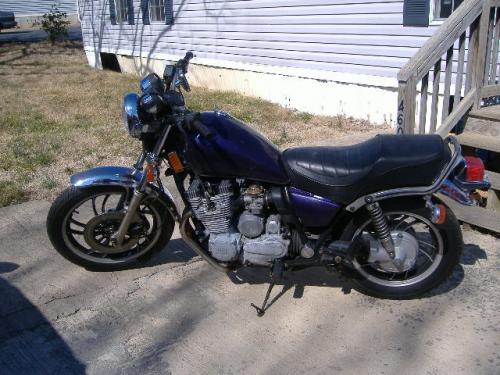
This is the parts bike.
Pages