That silver one is mine. I'm off to the Virginia DMV with my Certificate of Origin to register it. Hopefully it will go smoothly. I took the MSF safety course last weekend, passed the test and upgraded my drivers license to M for motorcycle. So far I have successfully applied for and received a vehicle loan for it from my credit union and got it insured with Allstate.
Ok, I'm back from the DMV. I have to give them credit. Current Motors wasn't in their system so they needed to call Richmond and have it added. I had to take a seat and wait about a half hour while they took care of that. After another 10-15 minutes at the window and I was on my way with my plate and registration. Now Current Motor Company is officially in the DMV system in Virginia.
One of the blue ones shown above is now in my garage, and today I had the first few miles longer ride. Great! Even in low power setting, a tour around neighborhood streets went well.
This picture shows a temporary plate I used...not where I live now.
My beautiful C130 was broken by the shipper on Tuesday, at least they did not even try to deliver it, but just sent it back. Hey guys? please check it carefully for steering head bearing and swing arm misalignment, or any structural damage, ok?
culseg and LeThala, congrats, and welcome to the owners club. I'm looking forward to hearing your impressions.
Alan, sorry to hear about your bike. R&L has been generally good, but obviously there's some risk in shipping anything. I just read an article about how many shipping containers fall into the ocean from container ships, apparently it averages out to several per day.
My beautiful C130 was broken by the shipper on Tuesday, at least they did not even try to deliver it, but just sent it back. Hey guys? please check it carefully for steering head bearing and swing arm misalignment, or any structural damage, ok?
Bummer!! That must be very disappointing.
My XM-3000 that I got a couple of years ago came damaged. It probably got damaged on the trip over from China. It had broken loose from its tie downs inside its shipping frame. It arrived with one of its handle bars poking through the box. X-treme sent me replacement parts for free after I sent them pictures but I had to fix it myself. That's one of the reasons I'm getting my C124 myself rather than having it shipped.
My beautiful C130 was broken by the shipper on Tuesday, at least they did not even try to deliver it, but just sent it back. Hey guys? please check it carefully for steering head bearing and swing arm misalignment, or any structural damage, ok?
Will do. We got it back today - looks like it took a nose dive off a forklift... We'll be giving it new parts galore (as well as several test rides).
To be fair to R+L they've done an OK job by us and, heck, "stuff" happens. We met with them yesterday and we're looking at upgrading to their re-usable shipping crates. Even the shipping is a learning experience - we're trying to find the most cost effective way of shipping and R+L are working with us. Can't ask for more than that.
Hey, maybe we'll put one of us in the crate along with the bike...
John H.Founder of Current Motor Company - opinions on this site belong to me; not to my employer Remember: " 'lectric for local. diesel for distance" - JTH, Amp Bros || "No Gas.
Thanks guys, I dont mind receiving the bike again if the frame passes muster, I know you will make it cosmetically right, I am most concerned with the steering head and swingarm, they are not meant to bear high side loads, they are designed for vertical loads. I trust you. Rotate the steering head, check the torque, sight down the swing arm, feel for roughness in the swing arm bearing, and ride it see if it tracks straight, if safe to do so, momentarily 'no-hands' for a test, if you have the confidence. I hate to be picky - but its a new bike that went through a crash, essentially. All is cool.
The danger of shipping damage, obvious, or worse, hidden, is why I'm going to going to take a drive out there with a small U-hail trailer and take delivery at the factory. But then, It is only a 4:45 drive for me.
John, what are the minimum trailer dimensions I will need? Thanks.
Well, I have shipped and received many motorcycles and maxi-scooters, crated, flatbed, pallet, odd ways, etc. Most came through A-ok, some were destroyed. Two had hidden damage to the swing arm that happened when the fall from the dock placed leverage on the rear wheel, and ruined the swing arm bearings and bent the swing arm proper. It was a mess. An otherwise prestigious dealer would not acknowledge the fact that the bike vibrated and would not track straight. In the present case, I am buying a new machine, not a used machine. But it is a hand-built machine - and I trust that John and the guys will go over it with a fine tooth comb. I would be especially pleased if Current had a frame alignment jig, all the more so because when importing these running chassis, it is a good idea to test for frame geometry tolerances every few shipments. They can also eyeball the swingarm to the front wheel sidewall with a straight-edge. And so on and so forth. The steering head is also vulnerable to side-loads in a drop or road crash - the steering head should be re-torqued, and rotated through its range while feeling for binding and roughness. ITs the most important bearing in the frame - etc.
There is one saving grace to bikes with plastic body parts - tupperware in the Scooter vernacular - such plastic parts often have a great deal of spring - and thus can take some of the impact in a shipping drop. If the drop is onto the side or levers the front wheel and flattens a steering race , then the bike will never be the same until the race is disassembled the neck is checked for proper alignment, and the bearing set re-set with the proper tools. Hassle, I know, but these two items, swing arm bearing and straightness, and steering head bearings - are the most likely to be damaged in a shipping drop.
And, the average age of the crew is impressive. There has got to be a lot of experience there. I'll feel very much at home amongst so many fellow boomers.
Terry (on the far right in the photo) isn't wearing any fungus, either - so that makes two out of eight, with him being the only one who has the option but shaves to the beat of his own dyno. I sympathize with the majority, though - it can get chilly in that shop!
We were going to call the business Beards'R'Us - but then Geoffrey the Giraffe would have sued us. And I asked Marie to grow a beard but she refuses.
Besides - I look even worse when you can see more of my face...
Hey - marco are you really coming out this way? If so, definitely stop by.
John H.Founder of Current Motor Company - opinions on this site belong to me; not to my employer Remember: " 'lectric for local. diesel for distance" - JTH, Amp Bros || "No Gas.
Ok, I have my Red C130 on the road - would you believe after all that pain, getting the plate, insurance, etc, they forget to give me the plate decal.....so I can't get the inspection....arrrrggggghhh. Idiots.
So I rode the bike in the cold, glad to have a windscreen, which affords great protection. Good going Current. The bike has plenty of mid range acceleration, but has a puzzlingly hard time pulling off the line, strange. That needs some addressing. But the power overall is worthy of merging onto a highway. The ride is well put together, no rattles, handles pretty good, but the fork compliance needs work. Dual rate springs probably would be the answer.
So far , so good. Im not sure what the heck that right hand gauge does, as it has not moved. I am very optimistic about the bike. It feels like quality here. The evolution of the marque will be an adventure I want to take an active role in. I could sell these at my retail location - they are good enough to represent to the die hard, non green scooter fraternity as an alternative for a local to mid range commuting. I will have more tomorrow after I go to the Danvers RMV and browbeat the drones and get my plate decal and inspection. ARRRRGGGGHHHHHH! MASS RMV BITE ME!!!!!
The right hand gauge is supposed to be an amp meter, but it's currently not implemented. (The BCU is still tracking the numbers, but the display was apparently too jittery to be useful.) It's going to be replaced with a small LCD display, which I hope we'll see in a few months. In the mean time, you'll have to use a well-calibrated butt-dynometer to estimate how much power is going to the wheel. Personally, I think I'd rather have a temp gauge than an amp meter, but there's at least 4 separate temps to display so I'm not sure how you handle that.
I agree that the initial acceleration is strangely weak, especially given how much oomph it has once it's moving. They're looking at that issue, but I don't know if a solution is coming anytime soon.
I agree that the initial acceleration is strangely weak, especially given how much oomph it has once it's moving. They're looking at that issue, but I don't know if a solution is coming anytime soon.
The VX-1 suffers from the same problem, even a good 50cc moped will beat it off-the -line.
I still don't quite understand why this is done, but maybe it is because the controller changes both voltage and current flowing to the motor. At low speed, the voltage might be greatly reduced. Therefore, to get to high power, very high current would be required at low speed. This high current causes components to fry, due to P=I^2*R. I might be wrong about this, though.
I just searched V a bit and found this explanation by X Vectrix again: http://visforvoltage.org/forum/7002-possible-future-vectux-open-source-vectrix#comment-41313
That sounds as if the real cause is probably different to my above attempt at an explanation (but P=I^2*R is still the principal culprit): The controller turns the power on and off in very brief bursts (PWM) when the bike stands still. During the "on" phase very high currents flow due to the dead-short of the motor windings at zero rpm. So the PWM can only be turned "on" for a very brief fraction at start-up. Once the optimum speed has been reached, the PWM is probably turning the current "on" continuously, hence the good power at speed (best around 70km/h on a VX-1).
The resistance of the IGBT's causes them to heat up if too much current flows. Because heat generated is an exponential function of the current flowing (P=I^2*R), the power needs to be drastically reduced at low rpm.
For example: Reducing the power to 1/4 by turning the IGBT's on for 25% of the time would reduce their heating by 75% if the speed was remaining the same (like with downhill driving).
But if the current doubles due to lower rpm during the 25% "on" time, then the IGBT heating will be the same as with 100% "on" time.
I think then "on" and "off" cycling is called "Duty cycle", but I'm not sure which way 'round it is used. I assume 100% duty cycle means on all the time.
100% duty cycle at 100A results in 100^2 * R = 10000A^2*R of heat in the IBGT's.
But 25% duty cycle at 200A also result in 200^2 * R *0.25 = 10000A^2*R.
.
To show the effect of the exponential heat generation with current lets assume a controller can handle 100A continuously (at 100% duty cycle) and has a 100V battery with no sag under load:
If the current at 0rpm is 100 times as high, then that means 10000A begin to flow when the throttle is first opened (I might be out by orders of magnitude with this guesstimate!) and this causes (10000A)^2*R of heating in the IGBT's. That means 100000000*A^2*R of heat being generated in the IGBT's. That's 10000 times as much as the continuous rating allows, therefore the duty cycle would have to be reduced to 1/10000 (0.0001 or 0.01%)
The max continuous power at 100% duty cycle would be 100A * 100V *100% = 10kW.
But "Off the line" the power at the motor would only be 10000A * 100V * 0.01% = 100W .
I'm making some wild guesses here, but I think it may show the principle of why the power is so badly reduced at low speed.
Hopefully someone else can explain it better or correct me if this is all complete hogwash, which it might be!
This information may be used entirely at your own risk.
Hi,
All electric motors have lower torque and use high amps to start rotation !at o-15?rpm there is very little alternation of current and a longer period of time spent between the changing from pole to pole ! back EMF (witch propels the armature)has to shift at a slower pace! I have often though a centrifical clutch on the stater timed to grab at 10-15rpm would solve the problem with a minimum of modification . Like riding the clutch in first gear! Or, a tight torque converter between the wheel rim and the armature to give the motor a chance to start ? Just ideas in my head !!! later StraWhistLe
Another factor is that the acceleration with an electric motor is deceptive when one is used to an IC powered vehicle. Electric propulsion produces linear acceleration (i.e. da/dt = nearly zero, like free-fall), while an IC engine with torque converter or clutch creates a large initial "jerk" (da/dt >>0) that creates an exaggerated "feel" of acceleration. This is a big reason why electric streetcars or subways are much more pleasant mass transit conveyances than buses, especially when having to ride standing.
The consequence is when starting at the front of a traffic signal in my scooter, I never feel like I am accelerating that much at all, yet the car behind me usually falls a surprising distance back.
If the current at 0rpm is 100 times as high, then that means 10000A begin to flow when the throttle is first opened (I might be out by orders of magnitude with this guesstimate!) and this causes (10000A)^2*R of heating in the IGBT's.
As usual, Mik is close to the money :)
a few basics to get started:
Torque is proportional to average motorside current
at 0 rpm, back emf = 0
the motor inductance stops the current rising directly to max.
so if the full 125v is applied to the motor at 0rpm, current wants to get to say 10'000A.
but at the instant you apply voltage, current is still 0A.
the inductance determines how fast the current rises:
current rise (A/s) = voltage applied to inductance (V) / inductance (H)
The controller turns the gate off when the current (instantaneous) reaches its max value (set in hardware).
The the controller turns off, the motor voltage is held at the freewheel diode voltage (usually 1V), and current decays until the next time the controller turns the gate on.
basically, initially the average current is much lower than peak current at low rpm.
the more the rpm, the higher the average current.
the peak current stays the same.
This happens until motor voltage = battery voltage, and average current = peak current.
Thus peak torque on an electric motor running from a controller is not at 0rpm (despite what the sales blurbs say).
There are a few things you can do to improve initial acceleration:
1) use a larger controller so you can get to a higher peak current, and limit average current in software.
2) add external inductors to slow the current rise
3) use a contactor setup to reduce the battery voltage intially, again to slow the current rise.
there are disadvantages:
1) more expensive
2) reduces effectiveness of field weakening on AC drives
3) more complicated, higher failure rates
Matt
Daily Ride:
2007 Vectrix, modified with 42 x Thundersky 60Ah in July 2010. Done 194'000km
The current you are looking at on the CANbus is the integrated battery current. This is battery current integrated at 15khz, so it is the true sum of all the current flowing from the battery but it is reported on the CANbus at 1Hz. Since the battery is feeding the IGBT at 15Khz you will not see the current spikes on the CANbus, its happening way too fast. Its these current spikes that are smoothed out by the motor (a big inductor). The motor current (phase current) is maximum at 0 rpm when the windings are basically a dead short. At full throttle from 0mph the phase current is maximum then begins to taper off, the bus current peaks about 3500 rpm or so.
The rate at which phase current increases and the maximum current are controlled, otherwise the IGBT would fry. Uncontrolled you could burn rubber...but only once!
Could one say (very simplified) that the motor controller turns the power back on (after it hit the max current) after 1/15000th of a second; and that this time is too long (compared to the very brief time/steep climb of the current curve when it is going up from a zero-V start) to get anywhere near the average max current that the controller can tolerate?
Would a motor controller that operates at 100MHz (I have no idea if such a thing exists!) get a much much better result - and would a MC operating at 1kHz be much worse "off the line" than a 15kHz MC?
This information may be used entirely at your own risk.
Would a motor controller that operates at 100MHz (I have no idea if such a thing exists!) get a much much better result - and would a MC operating at 1kHz be much worse "off the line" than a 15kHz MC?
If a controller operated at a higher frequency, yes the average current would be higher.
The losses would also be higher.
the amount of heat in the controller is mainly from two things (relatively equal between each):
1) the current in the conduction phase, where the gate is fully on.
at this stage, losses a proportional to the average of the current squared (I^2R)
2) the current in the linear stage, where the gate is switching between on and off.
the amount of heat generated each time the gate makes this transition has already been minimised. Thus, the more transitions the more heat. The higher the switching frequency, the higher the losses.
There are other factors aswell, such as the gate drivers ability to turn the gate on and off fast enough.
Matt
Daily Ride:
2007 Vectrix, modified with 42 x Thundersky 60Ah in July 2010. Done 194'000km
Maybe I can contribute a little science here. I'll take you through the graph and tell you what's going on in the motor and controller, then we can talk about low speed torque, OK? The graph above is a Current C130 on the dyno. This is a wide open throttle acceleration run. The X axis is time. The green trace in the top window is wheel RPM. The little glitch near the beginning is because the wheel was slipping on the drum for just a bit.
The lower window is more interesting. The red trace is battery amps, and the blue trace is motor phase winding amps (RMS). As you can see, when the rider opens the throttle at zero speed, the motor current goes immediately over 300 amps. It stays there until about 600RPM or 32MPH. This 325 amp limit is set in the motor controller (inverter). It's adjustable in software, but if you turn it up too much you'll let the expensive smoke out of the MOSFETS. Now lets look at the battery current, it's much lower. For instance, at something like 10MPH the battery current is only 100 amps, while the motor current is over 300. How can that be?
Remember back EMF is proportional to speed. Back EMF is basically the same as motor voltage. So at low speed the motor naturally has a low voltage. The voltage is controlled by the electromagnetics of the motor, not by the controller. So what's happening here is that we have about 96 volts going into the controller at 100 amps, and the controller is stepping that down to the lower voltsge the motor needs, and a higher current. It's acting as a buck converter, but the math is similar to a transformer -- less volts means more amps, power stays constant. Since we have 3x the amps, we must be at about 1/3 the voltage, or about 32 volts at the motor. (Yes, I'm simplifying some three-phase stuff here, the math would work for a DC motor)
As we move to the right, speed and motor voltage are increasing while motor current stays steady. So the motor is making more and more power. (P = A x V) When we get to the cursor bar we are at max power, nearly 15kW. From here on the controller limits the battery current, see how the red trace flattens out around 200 amps. This is to increase range and keep from abusing the batteries. The bike has great power here so nobody complains about this limit.
From about 600 RPM on, we're in the constant power region. Battery volts and amps are pretty flat, so power is constant. But the motor EMF voltage is rising, so the current has to fall for the power to stay constant. This means torque is also tapering off, since torque is proportional to current. At even higher speeds, like over 1000RPM, battery current tapers off too. This is because our battery voltage just isn't high enough compared to the motor EMF to push more power into the motor.
Wow, this is getting to be a long post! I hope you're finding it interesting? So now let's talk about low speed torque.
The most obvious way to increase torque is to increase current. At low speeds motor current is limited by the controller, so all we need is more or bigger MOSFETs and a bigger heatsink, right? Right, but that gets expensive fast. And if we're not careful we will put too much heat into the motor. Remember copper losses go up as the *square* of the motor current. There are lots of burned-out motors in the Current graveyard. We actually go partway here, since we have a temperature sensor inside the motor we allow this high current when the motor is cool. If the motor starts getting hot we restrict the current. This way most riders under most conditions get all the power the controller can handle, instead of restricting everybody all the time.
The details of three-phase commutation, and the way the PWM and the current limiting are designed, have some effect. But heat in the MOSFETS is proportional to RMS (average) current, and torque is also proportional to RMS current. So anything that makes more torque makes more heat in the motor and controller.
Another way to increase torque is to wind the motor differently, or use more powerful magnets in the motor. This gives you more torque per amp, which is a good thing. But there is a matching bad thing -- more back EMF per RPM. So this motor would make great torque but wouldn't have nearly as good a "top end". This is a fine motor to use on a moped that doesn't need to go fast, but it's not so good for a C130's mission.
Another approach is to use gears to multiply the torque. This is what the Vectrix VX-1 does. They use a smaller motor, turn it lots faster, and gear it down. The downside here is the mechanical complexity of a gearbox, as well as the cost, weight, and losses therein.
So what's the bottom line? Maybe it's that there is no "magic bullet". Everything is a tradeoff. We've gone pretty far down the path of optimizing performance of this hub motor and using a very powerful controller, with sensors and clever software to monitor the heat. And of course we're working on some new ideas, that's the fun part for me! But I can't say much about that now.
-- Erik Kauppi, Chief Engineer, Current Motor Co --
erikK , that was an excellent Report !!! do you know the temp of the motor at start and finish? What were the torque readings in Ft.Lb. at start and mid range ?? this is very interesting to be part of a real innovative machine !!! LaTeR
Thank you for taking the time to post this explanation, Erik. I find it fascinating. I'm wondering if the controller were tuned for efficiency rather than performance, would the controller settings be different? If so maybe the hi/low switch could toggle the controller settings between performance and efficiency modes? Of course, when the LCD display comes, it would be great to have a power indicator on it that would give me feedback that would allow me to choose a balance between performance and efficiency through how I use the throttle. There are many traffic lights in my area so I am constantly stopping and going.
I picked up my new C124 on April 15th and had the pleasure of meeting John and the rest of the team at Current Motors. I took some videos of John talking about the bike which I will edit into a little production and post on youtube when I get a chance. I'm between jobs right now so getting employed is my first priority and therefore I'm a little behind with my plans to post about my thoughts and experiences with the bike here on V.
My first impression is that this is a great bike and a joy to ride. My experience up to this point was with an XM-3000 which is a smaller, less powerful bike that does not require a license to ride in the state of Virginia. I commuted to work on my XM-3000 until I wiped out on it and broke my elbow because I overran my headlights and hit a curb the first time I rode home in the dark. After that experience I decided it is safer to be riding in traffic with the cars than on the shoulder with unexpected obstructions. I'm obviously not commuting to work yet on the C124, but I've taken it out for a few rides, both in the daylight and in the dark and I have to say that I feel much safer going 50mph on this larger bike than I did going 35 on the smaller one.
I will be starting separate threads on to discuss specific features of the bike where appropriate. I will also be taking real life measurements on things like speed on various terrains, range, power usage, etc. and posting the numbers. I have a kill a watt meter that I will be using to measure electricity use. I used it the first time this morning. I topped off the batteries after a 2.8 mi round trip to the store on a 30mph road. I took about 25 minutes to recharge the batteries using the fan noise from the charger as an indication that the charging was complete. The kill a watt meter indicated that the charge used 0.34 kwh. That comes to .12 kwh per mile. One reading doesn't mean much. I'll be keeping a journal of my trips and recharges and will post all the numbers in a separate thread.
Anyone want to add their C124/C130 performance to the '07 table below?
0-48 kph
0-80 kph
0-30 mph
0-50 mph
Vmax - kph
Vmax - mph
Vespa 250
4.4
9
105
65
Vectrix
5
9.5
101
63
XM-4500
7.8
19.5
86
53
XM-3500
8.8
N/A
61
38
The data was collected with fresh battery charges on level ground on non-windy days. All data was collected and analyzed using Corsa Instruments hardware and software.
Some things to note:
1. The Vespa's speedo indicated 75mph the GPS data was 65mph (see, we told you it wasn't just XM's that had "optimistic speedos"! ;)
2. Vectrix claim a 0-50mph time of 6.8 seconds on their website. It's possible that we could maybe squeeze another 0.5 to 1 second of improved accel time (after all I was riding someone else's bike!) but does anyone know of any independent online performance figures for the Vectrix? Do any intrepid Vectrix owners want to provide an electronically measured (e.g. GPS, radar, accelerometer) 0-50mph (0-80kph) time for us?
3. Note how close the Vectrix is to the Vespa.
4. While the XM-4500 isn't as quick off the line many people have ridden it and commented on how "brisk" the acceleration is.
5. The top speed we managed to get out of the XM-3500 on the day of testing was 38 mph - however, we had seen speeds of 42 mph at other times. We're not sure what caused the discrepancy - we checked the usual suspects (brake drag, tire pressure) but didn't spend too much time worrying about it.
Motorcycles: 2011 ZEV Trail 7100, 84V, 60AH, 60+mph, Cycle Analyst, TNC throttle, modified charger. 2013 Kymco GT300i
Bicycles: 2017 Sondors Thin
Cars: 2016 Leaf SV, 30KWH pack. 2007 CR-V
Solar array: 5KW. Cost per lifetime KWH produced $0.073
Bi
That's my Red One! You are a proud group - you are going to take the electric scooter mainstream. I will be there here....whatever! FLAME ON!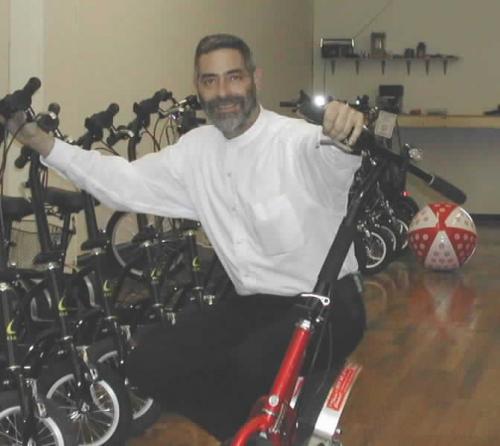
That silver one is mine. I'm off to the Virginia DMV with my Certificate of Origin to register it. Hopefully it will go smoothly. I took the MSF safety course last weekend, passed the test and upgraded my drivers license to M for motorcycle. So far I have successfully applied for and received a vehicle loan for it from my credit union and got it insured with Allstate.
John
Ok, I'm back from the DMV. I have to give them credit. Current Motors wasn't in their system so they needed to call Richmond and have it added. I had to take a seat and wait about a half hour while they took care of that. After another 10-15 minutes at the window and I was on my way with my plate and registration. Now Current Motor Company is officially in the DMV system in Virginia.
Next step: Go get my bike.
John
One of the blue ones shown above is now in my garage, and today I had the first few miles longer ride. Great! Even in low power setting, a tour around neighborhood streets went well.
This picture shows a temporary plate I used...not where I live now.
My beautiful C130 was broken by the shipper on Tuesday, at least they did not even try to deliver it, but just sent it back. Hey guys? please check it carefully for steering head bearing and swing arm misalignment, or any structural damage, ok?
culseg and LeThala, congrats, and welcome to the owners club. I'm looking forward to hearing your impressions.
Alan, sorry to hear about your bike. R&L has been generally good, but obviously there's some risk in shipping anything. I just read an article about how many shipping containers fall into the ocean from container ships, apparently it averages out to several per day.
My electric vehicle: CuMoCo C130 scooter.
Bummer!! That must be very disappointing.
My XM-3000 that I got a couple of years ago came damaged. It probably got damaged on the trip over from China. It had broken loose from its tie downs inside its shipping frame. It arrived with one of its handle bars poking through the box. X-treme sent me replacement parts for free after I sent them pictures but I had to fix it myself. That's one of the reasons I'm getting my C124 myself rather than having it shipped.
John
Will do. We got it back today - looks like it took a nose dive off a forklift... We'll be giving it new parts galore (as well as several test rides).
To be fair to R+L they've done an OK job by us and, heck, "stuff" happens. We met with them yesterday and we're looking at upgrading to their re-usable shipping crates. Even the shipping is a learning experience - we're trying to find the most cost effective way of shipping and R+L are working with us. Can't ask for more than that.
Hey, maybe we'll put one of us in the crate along with the bike...
John H. Founder of Current Motor Company - opinions on this site belong to me; not to my employer
Remember: " 'lectric for local. diesel for distance" - JTH, Amp Bros || "No Gas.
Thanks guys, I dont mind receiving the bike again if the frame passes muster, I know you will make it cosmetically right, I am most concerned with the steering head and swingarm, they are not meant to bear high side loads, they are designed for vertical loads. I trust you. Rotate the steering head, check the torque, sight down the swing arm, feel for roughness in the swing arm bearing, and ride it see if it tracks straight, if safe to do so, momentarily 'no-hands' for a test, if you have the confidence. I hate to be picky - but its a new bike that went through a crash, essentially. All is cool.
The danger of shipping damage, obvious, or worse, hidden, is why I'm going to going to take a drive out there with a small U-hail trailer and take delivery at the factory. But then, It is only a 4:45 drive for me.
John, what are the minimum trailer dimensions I will need? Thanks.
Well, I have shipped and received many motorcycles and maxi-scooters, crated, flatbed, pallet, odd ways, etc. Most came through A-ok, some were destroyed. Two had hidden damage to the swing arm that happened when the fall from the dock placed leverage on the rear wheel, and ruined the swing arm bearings and bent the swing arm proper. It was a mess. An otherwise prestigious dealer would not acknowledge the fact that the bike vibrated and would not track straight. In the present case, I am buying a new machine, not a used machine. But it is a hand-built machine - and I trust that John and the guys will go over it with a fine tooth comb. I would be especially pleased if Current had a frame alignment jig, all the more so because when importing these running chassis, it is a good idea to test for frame geometry tolerances every few shipments. They can also eyeball the swingarm to the front wheel sidewall with a straight-edge. And so on and so forth. The steering head is also vulnerable to side-loads in a drop or road crash - the steering head should be re-torqued, and rotated through its range while feeling for binding and roughness. ITs the most important bearing in the frame - etc.
There is one saving grace to bikes with plastic body parts - tupperware in the Scooter vernacular - such plastic parts often have a great deal of spring - and thus can take some of the impact in a shipping drop. If the drop is onto the side or levers the front wheel and flattens a steering race , then the bike will never be the same until the race is disassembled the neck is checked for proper alignment, and the bearing set re-set with the proper tools. Hassle, I know, but these two items, swing arm bearing and straightness, and steering head bearings - are the most likely to be damaged in a shipping drop.
...
John,
No need to reply. U-haul doesn't have the range of trailers it used to have. The smallest will be fine and I'll bring some lateral bracing material.
Hi, congratulations on the current steady progress.
I shall look forward to visiting you, and testing out the bike, later in the year on my annual pilgrimage to Michigan.
By the way, should I start to grow a beard to join the club?
Cheer's
marcopolo
Yup; the only one without a beard is the woman.
And, the average age of the crew is impressive. There has got to be a lot of experience there. I'll feel very much at home amongst so many fellow boomers.
Terry (on the far right in the photo) isn't wearing any fungus, either - so that makes two out of eight, with him being the only one who has the option but shaves to the beat of his own dyno. I sympathize with the majority, though - it can get chilly in that shop!
We were going to call the business Beards'R'Us - but then Geoffrey the Giraffe would have sued us. And I asked Marie to grow a beard but she refuses.
Besides - I look even worse when you can see more of my face...
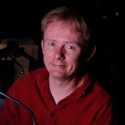
Hey - marco are you really coming out this way? If so, definitely stop by.
John H. Founder of Current Motor Company - opinions on this site belong to me; not to my employer
Remember: " 'lectric for local. diesel for distance" - JTH, Amp Bros || "No Gas.
Ok, I have my Red C130 on the road - would you believe after all that pain, getting the plate, insurance, etc, they forget to give me the plate decal.....so I can't get the inspection....arrrrggggghhh. Idiots.
So I rode the bike in the cold, glad to have a windscreen, which affords great protection. Good going Current. The bike has plenty of mid range acceleration, but has a puzzlingly hard time pulling off the line, strange. That needs some addressing. But the power overall is worthy of merging onto a highway. The ride is well put together, no rattles, handles pretty good, but the fork compliance needs work. Dual rate springs probably would be the answer.
So far , so good. Im not sure what the heck that right hand gauge does, as it has not moved. I am very optimistic about the bike. It feels like quality here. The evolution of the marque will be an adventure I want to take an active role in. I could sell these at my retail location - they are good enough to represent to the die hard, non green scooter fraternity as an alternative for a local to mid range commuting. I will have more tomorrow after I go to the Danvers RMV and browbeat the drones and get my plate decal and inspection. ARRRRGGGGHHHHHH! MASS RMV BITE ME!!!!!
I will attach a picture
of my electric fleet here
OOhh, congrats!
The right hand gauge is supposed to be an amp meter, but it's currently not implemented. (The BCU is still tracking the numbers, but the display was apparently too jittery to be useful.) It's going to be replaced with a small LCD display, which I hope we'll see in a few months. In the mean time, you'll have to use a well-calibrated butt-dynometer to estimate how much power is going to the wheel. Personally, I think I'd rather have a temp gauge than an amp meter, but there's at least 4 separate temps to display so I'm not sure how you handle that.
I agree that the initial acceleration is strangely weak, especially given how much oomph it has once it's moving. They're looking at that issue, but I don't know if a solution is coming anytime soon.
My electric vehicle: CuMoCo C130 scooter.
The VX-1 suffers from the same problem, even a good 50cc moped will beat it off-the -line.
I still don't quite understand why this is done, but maybe it is because the controller changes both voltage and current flowing to the motor. At low speed, the voltage might be greatly reduced. Therefore, to get to high power, very high current would be required at low speed. This high current causes components to fry, due to P=I^2*R. I might be wrong about this, though.
I just searched V a bit and found this explanation by X Vectrix again: http://visforvoltage.org/forum/7002-possible-future-vectux-open-source-vectrix#comment-41313
That sounds as if the real cause is probably different to my above attempt at an explanation (but P=I^2*R is still the principal culprit): The controller turns the power on and off in very brief bursts (PWM) when the bike stands still. During the "on" phase very high currents flow due to the dead-short of the motor windings at zero rpm. So the PWM can only be turned "on" for a very brief fraction at start-up. Once the optimum speed has been reached, the PWM is probably turning the current "on" continuously, hence the good power at speed (best around 70km/h on a VX-1).
The resistance of the IGBT's causes them to heat up if too much current flows. Because heat generated is an exponential function of the current flowing (P=I^2*R), the power needs to be drastically reduced at low rpm.
For example: Reducing the power to 1/4 by turning the IGBT's on for 25% of the time would reduce their heating by 75% if the speed was remaining the same (like with downhill driving).
But if the current doubles due to lower rpm during the 25% "on" time, then the IGBT heating will be the same as with 100% "on" time.
I think then "on" and "off" cycling is called "Duty cycle", but I'm not sure which way 'round it is used. I assume 100% duty cycle means on all the time.
100% duty cycle at 100A results in 100^2 * R = 10000A^2*R of heat in the IBGT's.
But 25% duty cycle at 200A also result in 200^2 * R *0.25 = 10000A^2*R.
.
To show the effect of the exponential heat generation with current lets assume a controller can handle 100A continuously (at 100% duty cycle) and has a 100V battery with no sag under load:
If the current at 0rpm is 100 times as high, then that means 10000A begin to flow when the throttle is first opened (I might be out by orders of magnitude with this guesstimate!) and this causes (10000A)^2*R of heating in the IGBT's. That means 100000000*A^2*R of heat being generated in the IGBT's. That's 10000 times as much as the continuous rating allows, therefore the duty cycle would have to be reduced to 1/10000 (0.0001 or 0.01%)
The max continuous power at 100% duty cycle would be 100A * 100V *100% = 10kW.
But "Off the line" the power at the motor would only be 10000A * 100V * 0.01% = 100W .
I'm making some wild guesses here, but I think it may show the principle of why the power is so badly reduced at low speed.
Hopefully someone else can explain it better or correct me if this is all complete hogwash, which it might be!
This information may be used entirely at your own risk.
There is always a way if there is no other way!
Hi,
All electric motors have lower torque and use high amps to start rotation !at o-15?rpm there is very little alternation of current and a longer period of time spent between the changing from pole to pole ! back EMF (witch propels the armature)has to shift at a slower pace! I have often though a centrifical clutch on the stater timed to grab at 10-15rpm would solve the problem with a minimum of modification . Like riding the clutch in first gear! Or, a tight torque converter between the wheel rim and the armature to give the motor a chance to start ? Just ideas in my head !!! later StraWhistLe
thank GOD I wake up above ground !!!!
Another factor is that the acceleration with an electric motor is deceptive when one is used to an IC powered vehicle. Electric propulsion produces linear acceleration (i.e. da/dt = nearly zero, like free-fall), while an IC engine with torque converter or clutch creates a large initial "jerk" (da/dt >>0) that creates an exaggerated "feel" of acceleration. This is a big reason why electric streetcars or subways are much more pleasant mass transit conveyances than buses, especially when having to ride standing.
The consequence is when starting at the front of a traffic signal in my scooter, I never feel like I am accelerating that much at all, yet the car behind me usually falls a surprising distance back.
As usual, Mik is close to the money :)
a few basics to get started:
Torque is proportional to average motorside current
at 0 rpm, back emf = 0
the motor inductance stops the current rising directly to max.
so if the full 125v is applied to the motor at 0rpm, current wants to get to say 10'000A.
but at the instant you apply voltage, current is still 0A.
the inductance determines how fast the current rises:
current rise (A/s) = voltage applied to inductance (V) / inductance (H)
The controller turns the gate off when the current (instantaneous) reaches its max value (set in hardware).
The the controller turns off, the motor voltage is held at the freewheel diode voltage (usually 1V), and current decays until the next time the controller turns the gate on.
basically, initially the average current is much lower than peak current at low rpm.
the more the rpm, the higher the average current.
the peak current stays the same.
This happens until motor voltage = battery voltage, and average current = peak current.
Thus peak torque on an electric motor running from a controller is not at 0rpm (despite what the sales blurbs say).
There are a few things you can do to improve initial acceleration:
1) use a larger controller so you can get to a higher peak current, and limit average current in software.
2) add external inductors to slow the current rise
3) use a contactor setup to reduce the battery voltage intially, again to slow the current rise.
there are disadvantages:
1) more expensive
2) reduces effectiveness of field weakening on AC drives
3) more complicated, higher failure rates
Matt
Daily Ride:
2007 Vectrix, modified with 42 x Thundersky 60Ah in July 2010. Done 194'000km
Thanks, Matt!
Combining this with X Vectrix' explanation:
Could one say (very simplified) that the motor controller turns the power back on (after it hit the max current) after 1/15000th of a second; and that this time is too long (compared to the very brief time/steep climb of the current curve when it is going up from a zero-V start) to get anywhere near the average max current that the controller can tolerate?
Would a motor controller that operates at 100MHz (I have no idea if such a thing exists!) get a much much better result - and would a MC operating at 1kHz be much worse "off the line" than a 15kHz MC?
This information may be used entirely at your own risk.
There is always a way if there is no other way!
If a controller operated at a higher frequency, yes the average current would be higher.
The losses would also be higher.
the amount of heat in the controller is mainly from two things (relatively equal between each):
1) the current in the conduction phase, where the gate is fully on.
at this stage, losses a proportional to the average of the current squared (I^2R)
2) the current in the linear stage, where the gate is switching between on and off.
the amount of heat generated each time the gate makes this transition has already been minimised. Thus, the more transitions the more heat. The higher the switching frequency, the higher the losses.
There are other factors aswell, such as the gate drivers ability to turn the gate on and off fast enough.
Matt
Daily Ride:
2007 Vectrix, modified with 42 x Thundersky 60Ah in July 2010. Done 194'000km
Maybe I can contribute a little science here. I'll take you through the graph and tell you what's going on in the motor and controller, then we can talk about low speed torque, OK? The graph above is a Current C130 on the dyno. This is a wide open throttle acceleration run. The X axis is time. The green trace in the top window is wheel RPM. The little glitch near the beginning is because the wheel was slipping on the drum for just a bit.
The lower window is more interesting. The red trace is battery amps, and the blue trace is motor phase winding amps (RMS). As you can see, when the rider opens the throttle at zero speed, the motor current goes immediately over 300 amps. It stays there until about 600RPM or 32MPH. This 325 amp limit is set in the motor controller (inverter). It's adjustable in software, but if you turn it up too much you'll let the expensive smoke out of the MOSFETS. Now lets look at the battery current, it's much lower. For instance, at something like 10MPH the battery current is only 100 amps, while the motor current is over 300. How can that be?
Remember back EMF is proportional to speed. Back EMF is basically the same as motor voltage. So at low speed the motor naturally has a low voltage. The voltage is controlled by the electromagnetics of the motor, not by the controller. So what's happening here is that we have about 96 volts going into the controller at 100 amps, and the controller is stepping that down to the lower voltsge the motor needs, and a higher current. It's acting as a buck converter, but the math is similar to a transformer -- less volts means more amps, power stays constant. Since we have 3x the amps, we must be at about 1/3 the voltage, or about 32 volts at the motor. (Yes, I'm simplifying some three-phase stuff here, the math would work for a DC motor)
As we move to the right, speed and motor voltage are increasing while motor current stays steady. So the motor is making more and more power. (P = A x V) When we get to the cursor bar we are at max power, nearly 15kW. From here on the controller limits the battery current, see how the red trace flattens out around 200 amps. This is to increase range and keep from abusing the batteries. The bike has great power here so nobody complains about this limit.
From about 600 RPM on, we're in the constant power region. Battery volts and amps are pretty flat, so power is constant. But the motor EMF voltage is rising, so the current has to fall for the power to stay constant. This means torque is also tapering off, since torque is proportional to current. At even higher speeds, like over 1000RPM, battery current tapers off too. This is because our battery voltage just isn't high enough compared to the motor EMF to push more power into the motor.
Wow, this is getting to be a long post! I hope you're finding it interesting? So now let's talk about low speed torque.
The most obvious way to increase torque is to increase current. At low speeds motor current is limited by the controller, so all we need is more or bigger MOSFETs and a bigger heatsink, right? Right, but that gets expensive fast. And if we're not careful we will put too much heat into the motor. Remember copper losses go up as the *square* of the motor current. There are lots of burned-out motors in the Current graveyard. We actually go partway here, since we have a temperature sensor inside the motor we allow this high current when the motor is cool. If the motor starts getting hot we restrict the current. This way most riders under most conditions get all the power the controller can handle, instead of restricting everybody all the time.
The details of three-phase commutation, and the way the PWM and the current limiting are designed, have some effect. But heat in the MOSFETS is proportional to RMS (average) current, and torque is also proportional to RMS current. So anything that makes more torque makes more heat in the motor and controller.
Another way to increase torque is to wind the motor differently, or use more powerful magnets in the motor. This gives you more torque per amp, which is a good thing. But there is a matching bad thing -- more back EMF per RPM. So this motor would make great torque but wouldn't have nearly as good a "top end". This is a fine motor to use on a moped that doesn't need to go fast, but it's not so good for a C130's mission.
Another approach is to use gears to multiply the torque. This is what the Vectrix VX-1 does. They use a smaller motor, turn it lots faster, and gear it down. The downside here is the mechanical complexity of a gearbox, as well as the cost, weight, and losses therein.
So what's the bottom line? Maybe it's that there is no "magic bullet". Everything is a tradeoff. We've gone pretty far down the path of optimizing performance of this hub motor and using a very powerful controller, with sensors and clever software to monitor the heat. And of course we're working on some new ideas, that's the fun part for me! But I can't say much about that now.
-- Erik Kauppi, Chief Engineer, Current Motor Co --
erikK , that was an excellent Report !!! do you know the temp of the motor at start and finish? What were the torque readings in Ft.Lb. at start and mid range ?? this is very interesting to be part of a real innovative machine !!! LaTeR
thank GOD I wake up above ground !!!!
Thank you for taking the time to post this explanation, Erik. I find it fascinating. I'm wondering if the controller were tuned for efficiency rather than performance, would the controller settings be different? If so maybe the hi/low switch could toggle the controller settings between performance and efficiency modes? Of course, when the LCD display comes, it would be great to have a power indicator on it that would give me feedback that would allow me to choose a balance between performance and efficiency through how I use the throttle. There are many traffic lights in my area so I am constantly stopping and going.
John D.
I picked up my new C124 on April 15th and had the pleasure of meeting John and the rest of the team at Current Motors. I took some videos of John talking about the bike which I will edit into a little production and post on youtube when I get a chance. I'm between jobs right now so getting employed is my first priority and therefore I'm a little behind with my plans to post about my thoughts and experiences with the bike here on V.
My first impression is that this is a great bike and a joy to ride. My experience up to this point was with an XM-3000 which is a smaller, less powerful bike that does not require a license to ride in the state of Virginia. I commuted to work on my XM-3000 until I wiped out on it and broke my elbow because I overran my headlights and hit a curb the first time I rode home in the dark. After that experience I decided it is safer to be riding in traffic with the cars than on the shoulder with unexpected obstructions. I'm obviously not commuting to work yet on the C124, but I've taken it out for a few rides, both in the daylight and in the dark and I have to say that I feel much safer going 50mph on this larger bike than I did going 35 on the smaller one.
I will be starting separate threads on to discuss specific features of the bike where appropriate. I will also be taking real life measurements on things like speed on various terrains, range, power usage, etc. and posting the numbers. I have a kill a watt meter that I will be using to measure electricity use. I used it the first time this morning. I topped off the batteries after a 2.8 mi round trip to the store on a 30mph road. I took about 25 minutes to recharge the batteries using the fan noise from the charger as an indication that the charging was complete. The kill a watt meter indicated that the charge used 0.34 kwh. That comes to .12 kwh per mile. One reading doesn't mean much. I'll be keeping a journal of my trips and recharges and will post all the numbers in a separate thread.
John D.
Anyone want to add their C124/C130 performance to the '07 table below?
Motorcycles: 2011 ZEV Trail 7100, 84V, 60AH, 60+mph, Cycle Analyst, TNC throttle, modified charger. 2013 Kymco GT300i
Bicycles: 2017 Sondors Thin
Cars: 2016 Leaf SV, 30KWH pack. 2007 CR-V
Solar array: 5KW. Cost per lifetime KWH produced $0.073
Bi