I used two 16mm2 busbars in parallel so it is good for a max of 320Amps (10 Amps for each 1mm2)
In my case 10mm2 would have been enough since the Vectrix doesn't draw more then the fuse which is 200Amps.
ah no, current ratings don't work like that
10mm2 is only good for ~40A continuous
25mm2 is only good for 120A continuous
both with 60 deg C temp rise above ambient
the buss bars on my conversions are 50mm2 braided - rated to 185A continuous (still at 60 deg C temp rise)
If keeping to only 30 Deg C temp rise, the 50mm2 braided is good for 90A continuous - which is the most a vectrix will draw continuous at top speed in hot weather
2 x 16mm2 is as good as 1 x 50mm2 from a temp rise perspective, though higher losses (2 x 16mm2 has better cooling)
2 x 25mm2 is better than a single 50mm2 from a temp rise perspective, but same losses
So, if i understand correctly 2 x 25mm2 is a safe choice. It will be a big challenge to construct this. :0
So, if i understand correctly 2 x 25mm2 is a safe choice. It will be a big challenge to construct this. :0
you can use multiple bussbars in parrallel - so 2 x 25mm2 is safe, but you could also use 3 x 16mm2
with a high cell count, you are actually better off with many series connections between the parrallel groups, rather than a single large connection - it helps keep the current flow even
Daily Ride:
2007 Vectrix, modified with 42 x Thundersky 60Ah in July 2010. Done 194'000km
I think the busbars you are planning are larger than needed. This is what I have experienced over the past four years. The first Vectrix battery set I made was 90 AmpHr and went in my first red scooter. It had 2 x 6 mm2 copper busbars. I rode that scooter for 18 months with no problems until an accident with a car. The next scooter has 2 x 10mm2 busbars and this is what I use in my conversion kits. No problems with either 2 x 6mm2 or 2 x 10 mm2.
I think too actually.
Rule of thumb says 10A per 1mm2 which is why we are able to jank about 16A over 1,5mm2 solid copper wire here according the NEN1010 regulations, and i believe even 32A is allowed over 2,5mm2.
I think it differs if you used braided wire or solid copper. The latter is what i'm using.
you can use multiple bussbars in parrallel - so 2 x 25mm2 is safe, but you could also use 3 x 16mm2
with a high cell count, you are actually better off with many series connections between the parrallel groups, rather than a single large connection - it helps keep the current flow even
I dont see how to use 3 busbars on 3 cells parallel because the middle busbar won't allow you to weld the tabs on the middle cell...
With 2 busbars each bar is between cells.
On another forum i'm in a discussion about these multl parallel or serial wiring between cells. The consensus there is that it is better to create long serial connections and only connect these serials on the ends, so no intermediate connections to prevent cross-cell-current flowing.
In this particular case its about connection the Vectrix NiMh cells in strings of 34 cells each and have these in parallel of 3. So its a 3P34S instead of 34S3P setup.
===================================
My contribution to EV in The Netherlands
- Novox C20
- Vectrix VX-1 Li+ my2009 #2791
- Vectrix VX-1 Li my2011 #3228
- CityEl Fact4 / Mini El Cabrio
- Th!nk PIV4 A266
- Th!nk City A306
- Tesla Model3 AWD
I used two 16mm2 busbars in parallel so it is good for a max of 320Amps (10 Amps for each 1mm2)
In my case 10mm2 would have been enough since the Vectrix doesn't draw more then the fuse which is 200Amps.
A while ago I sent you a pm.
I do have a lot of trouble getting mail though my systems lately because of the heavy spam filtering, in and out, so im not always up to date, sorry about that.
===================================
My contribution to EV in The Netherlands
- Novox C20
- Vectrix VX-1 Li+ my2009 #2791
- Vectrix VX-1 Li my2011 #3228
- CityEl Fact4 / Mini El Cabrio
- Th!nk PIV4 A266
- Th!nk City A306
- Tesla Model3 AWD
I think the busbars you are planning are larger than needed. This is what I have experienced over the past four years. The first Vectrix battery set I made was 90 AmpHr and went in my first red scooter. It had 2 x 6 mm2 copper busbars. I rode that scooter for 18 months with no problems until an accident with a car. The next scooter has 2 x 10mm2 busbars and this is what I use in my conversion kits. No problems with either 2 x 6mm2 or 2 x 10 mm2.
The cells themselves will act as heat sinks, though long term keeping them cool is necessary for keeping capacity loss under control
my original 40Ah thundersky conversions used 25mm2 copper leaf conductors.
I used to keep the original temp sensors - I used to get temp warnings in summer (of course the LiFePO4 batteries could take a higher temp than the nimh cells could).
The original nimh cell interconnects are 48mm2 (I actually re-use these on the leaf module conversions)
Did you measure battery temperature in your original conversion?
I don't measure battery temp any more (to be honest), though I did for the early conversions
I think too actually.
Rule of thumb says 10A per 1mm2 which is why we are able to jank about 16A over 1,5mm2 solid copper wire here according the NEN1010 regulations, and i believe even 32A is allowed over 2,5mm2.
I^2R - doubling the current quadruples the heat, halving the resistance still means you have twice the heat.
current ratings have more to do with what temp rise you are willing to accept, what cooling the wire has, and how long the current will flow for.
I would suggest testing it on a small scale - you have a 100Ah?
I would push 100A through the wire continuous for an hour - that's basically the worst case scenario
you may find 2 x 16mm2 or 2 x 10mm2 to be sufficient, or you may not
Daily Ride:
2007 Vectrix, modified with 42 x Thundersky 60Ah in July 2010. Done 194'000km
On another forum i'm in a discussion about these multl parallel or serial wiring between cells. The consensus there is that it is better to create long serial connections and only connect these serials on the ends, so no intermediate connections to prevent cross-cell-current flowing.
In this particular case its about connection the Vectrix NiMh cells in strings of 34 cells each and have these in parallel of 3. So its a 3P34S instead of 34S3P setup.
I agree for lossy batteries (lead acid, nimh, etc) keeping track of and managing the side reactions is important.
nimh in particular has a falling voltage at full charge which is disastrous in a parrallel situation
I would suggest it's irrelevant for lithium batteries (all variants). The lithium batteries we are using don't have side reactions within their normal operating window. 2 or 3 in parrallel probably won't need fusing, any more and protection against internal shorts becomes necessary
Daily Ride:
2007 Vectrix, modified with 42 x Thundersky 60Ah in July 2010. Done 194'000km
I^2R - doubling the current quadruples the heat, halving the resistance still means you have twice the heat.
current ratings have more to do with what temp rise you are willing to accept, what cooling the wire has, and how long the current will flow for.
I would suggest testing it on a small scale - you have a 100Ah?
I would push 100A through the wire continuous for an hour - that's basically the worst case scenario
you may find 2 x 16mm2 or 2 x 10mm2 to be sufficient, or you may not
Im not sure if that test would reflect whats going on with the Li battery. My setup is that every 3 cells in parallel are connected to the two busbars. So for the bottom piece of busbar where the last 3-cells are connected it only has to transport 30A max (10A per cell) in total so each busbar (i have two) transports 15A. The next piece of busbar further along the line will add the Amps for the next set of 3-cells so it adds 15A to each busbar, at that point 30A in total. For the next set of 3-cell, again adding 15A, and again, and again until the last set of 3-cell add their max current. So looking at the Amps at every 2cm (cells connections are aprox 2cm apart) along the busbar it would look like this: 15A - 30A - 45A - 60A - 75A - 90A - 105A - 120A - 135A - 150A. So its actually only the last 6cm of solid 16mm2 copper busbar that would transport over 100A (worst case scenario). The R of this short piece is close to nothing so i dont think it would warmup even noticeable transporting 100A or more.
BTW my busbar interconnections are made by 2 M6 bolt/nut so thats close to 60mm2 together.
The 48/50mm2 Vectrix wiring you are referring to is lesser then my interconnects so thats no problem at all.
My next setup of Li-pack which i'm currently building doesnt use sold busbars at all, but every set of 6 cells is connected by two 2,5mm2 or 4mm2 wires to the top. So each set of 6-cells can transport easily upto 80A max over these wires, good enough for 10A cells like the 29E. So for these 36P blocks i just need 6 wires on each side of the block to the interconnecting busbars at the top. Much easier to construct and each set of 6 cells could be fused (if wanted) very easily.
===================================
My contribution to EV in The Netherlands
- Novox C20
- Vectrix VX-1 Li+ my2009 #2791
- Vectrix VX-1 Li my2011 #3228
- CityEl Fact4 / Mini El Cabrio
- Th!nk PIV4 A266
- Th!nk City A306
- Tesla Model3 AWD
Well thats more proof then ever that some people shouldn't drink the Dutch beer Heineken, its too strong for them...
He better had put the red wire in his left ear and the black wire in his right ear...
See what blows first....
===================================
My contribution to EV in The Netherlands
- Novox C20
- Vectrix VX-1 Li+ my2009 #2791
- Vectrix VX-1 Li my2011 #3228
- CityEl Fact4 / Mini El Cabrio
- Th!nk PIV4 A266
- Th!nk City A306
- Tesla Model3 AWD
Heres my latest 'toy' :-)
Fully automated CNC spotwelder for lithium packs....
Packs with these black brackets as seen on the movie dont fit very efficient in the Vectrix though.
I'm working on another setup to make it work.
===================================
My contribution to EV in The Netherlands
- Novox C20
- Vectrix VX-1 Li+ my2009 #2791
- Vectrix VX-1 Li my2011 #3228
- CityEl Fact4 / Mini El Cabrio
- Th!nk PIV4 A266
- Th!nk City A306
- Tesla Model3 AWD
Paul, that is looking great men. A fine machine for your next conversions.
My own project is coming a bit to a hold because i tried to solder the nikkel strips to the copper busbars.
The flat copper busbars are 3mm thick and will not get hot enough. I think i will drop that idea. Now I like to use a holenail(see pictures)
to attach the nikkel to the copper.
I don't know if that is a good idea, but it is a very robust attachment.
I think it is some overkill using this copper chunks...
Why not go for layered nickel strip as busbar like i showed you ?
That's what you can weld and is by far the cleanest solution.
===================================
My contribution to EV in The Netherlands
- Novox C20
- Vectrix VX-1 Li+ my2009 #2791
- Vectrix VX-1 Li my2011 #3228
- CityEl Fact4 / Mini El Cabrio
- Th!nk PIV4 A266
- Th!nk City A306
- Tesla Model3 AWD
I think it is some overkill using this copper chunks...
Why not go for layered nickel strip as busbar like i showed you ?
That's what you can weld and is by far the cleanest solution.
I agree with you that it is a overkill, but I have already bought the copper and have cut the nickel into small pieces.
The flat copper bushbars where the smallest I could get my hands on.
It would be a shame not to use it.
A small advantage of the thick copper is the issue of resistance and overheating I think.
Did you test your solution with the multiple layers of nickel strips?
Well, i finished welding my new batterypack 18650 Samsung 29E, total 36S36P. I did 5250 welds with the JP Spotwelder without any problems. :0
The next step was removing the old Li pack(30Ah). Thanks to all the good information on this forum removal was a piece of cake.
Btw: can i re-use the original BMS? exists a wiring diagram? I'm a little bit confused while the Li configuration is a lot different
then the configuration with the 18650 cells.
Nice work, I think you can re-use the BMS but I am not sure if there is a wiring diagram. There are 4 PCBs (0-3) one for up to 10 cells. I think it will be the easiest way to reconnect the new batteries to the connectors where the current one (cell 1-36)are. What I don't know is what will happen if you have only 36 instead of 40cells. I bought the BMS from vectrixparts. In my case it was wired cell 1-9 to BMS0 PCB, 10-18 BMS1 PCB, 19-27 BMS2 PCb and 28-36 BMS3 PCB. I hope this help a little bit and maybe someone else can help more.
Nice work, I think you can re-use the BMS but I am not sure if there is a wiring diagram. There are 4 PCBs (0-3) one for up to 10 cells. I think it will be the easiest way to reconnect the new batteries to the connectors where the current one (cell 1-36)are. What I don't know is what will happen if you have only 36 instead of 40cells. I bought the BMS from vectrixparts. In my case it was wired cell 1-9 to BMS0 PCB, 10-18 BMS1 PCB, 19-27 BMS2 PCb and 28-36 BMS3 PCB. I hope this help a little bit and maybe someone else can help more.
Thx Rolli, all info will help. Two wires are connected to the bottom of each batterypack(20 cells). I am not sure but i think that they are temp.sensors? (black and white wires)
Hi Prensel! (
One question. When you accelerate in Vectrix, the value of low cell and the high cell give big diferences?Like low 3.6 and hi 3.75? (at rest the values are equal)
@Meridiaan I think you are right that this are the temp. Sensors for more I have to see the connectors where they are connected. But to keep this BMS you have to contact vectrixpart, because they have the right Firmware and know the wiring. I haven´t seen the BMS Firmware anywere. If you need help I have bought the BMS from them, maybe I can help.
@Vortex I am not Prensel but I have the same conversation. Sometimes I get the same differences but it depends on circumstances. Somtimes I have it then they disappear. In my case the differences are higher when I accelerate slow.(I see only Hi and lo)
@Meridiaan I think you are right that this are the temp. Sensors for more I have to see the connectors where they are connected. But to keep this BMS you have to contact vectrixpart, because they have the right Firmware and know the wiring. I haven´t seen the BMS Firmware anywere. If you need help I have bought the BMS from them, maybe I can help.
I found very useful stuff on service.vectrixparts.com, thanks a lot, Rolli!!
@Vortex I am not Prensel but I have the same conversation. Sometimes I get the same differences but it depends on circumstances. Somtimes I have it then they disappear. In my case the differences are higher when I accelerate slow.(I see only Hi and lo)
Tks a lot.I believe this difference is because in this moment the environment temperature is (10º/12º)
I'm nearing the 10.000km mark pretty soon :-)
The bike is driving almost daily, even in wintertime without any problem at all.
Current range is about +120km.
This 'proof-of-concept' has been succesfull and i will be able to sell these Vectrix-modules brand-new for sale pretty soon.
===================================
My contribution to EV in The Netherlands
- Novox C20
- Vectrix VX-1 Li+ my2009 #2791
- Vectrix VX-1 Li my2011 #3228
- CityEl Fact4 / Mini El Cabrio
- Th!nk PIV4 A266
- Th!nk City A306
- Tesla Model3 AWD
I'm nearing the 10.000km mark pretty soon :-)
The bike is driving almost daily, even in wintertime without any problem at all.
Current range is about +120km.
This 'proof-of-concept' has been succesfull and i will be able to sell these Vectrix-modules brand-new for sale pretty soon.
I'm interested!
Do you have an idea of the pack price?
I'm nearing the 10.000km mark pretty soon :-)
The bike is driving almost daily, even in wintertime without any problem at all.
Current range is about +120km.
This 'proof-of-concept' has been succesfull and i will be able to sell these Vectrix-modules brand-new for sale pretty soon.
Great Job, Prensel.
My conversion is still in progress (36S36P). I am waiting for several parts from Poland.
I recently ordered a BMS adaptor and a BMS case from Vectrixparts. They advised me to re-use the former BMS Boards(Li+).
Together with new cables,a wire diagram and new software i should be able to re-install the BMS.
Maybe within a few weeks another Vectrix is on the road again!
My goal is a range of +130km.
Slightly off-topic, but I'm working on a conversion to A123 ANR-26650's. One question I have is what's the maximum voltage the controller can handle? I am replacing the charger, so that's not an issue. I can see they used a Vicor DC-DC converter and I know those have hard limits, but w/o unsoldering it, I can't see which model it is. Anyone know?
Incidentally, I have a whole bunch of NiMh cells from the original bike with about 4500 miles on them. One cell of the bunch failed and that in turn somehow caused the original charger to blow up as well.
I'm nearing the 10.000km mark pretty soon :-)
My conversion is still in progress (36S36P). I am waiting for several parts from Poland.
I recently ordered a BMS adaptor and a BMS case from Vectrixparts. They advised me to re-use the former BMS Boards(Li+).
Together with new cables,a wire diagram and new software i should be able to re-install the BMS.
Maybe within a few weeks another Vectrix is on the road again!
My goal is a range of +130km.
Update: All parts delivered. Besides small issues: there is no wiring diagram. Still waiting for our polish friends.
Will i ride again this summer? .....who knows...
My conversion is still in progress (36S36P). I am waiting for several parts from Poland.
I recently ordered a BMS adaptor and a BMS case from Vectrixparts. They advised me to re-use the former BMS Boards(Li+).
Together with new cables,a wire diagram and new software i should be able to re-install the BMS.
Maybe within a few weeks another Vectrix is on the road again!
My goal is a range of +130km.
Update: All parts delivered. Besides small issues: there is no wiring diagram. Still waiting for our polish friends.
Will i ride again this summer? .....who knows...
I took the liberty of drawing an own BMS wiring diagram and sent it to Poland for comment.
They approved and so I am back in business.
Did all the wiring and run a diagnostic with the diagnostic tool.
It came up with the following:
Whats wrong? I checked and double checked , the part of Bd 2 cell 1 to 4 and Bd3 cell 1 and 2 is very strange.
So, if i understand correctly 2 x 25mm2 is a safe choice. It will be a big challenge to construct this. :0
A while ago I sent you a pm.
you can use multiple bussbars in parrallel - so 2 x 25mm2 is safe, but you could also use 3 x 16mm2
with a high cell count, you are actually better off with many series connections between the parrallel groups, rather than a single large connection - it helps keep the current flow even
Daily Ride:
2007 Vectrix, modified with 42 x Thundersky 60Ah in July 2010. Done 194'000km
I think the busbars you are planning are larger than needed. This is what I have experienced over the past four years. The first Vectrix battery set I made was 90 AmpHr and went in my first red scooter. It had 2 x 6 mm2 copper busbars. I rode that scooter for 18 months with no problems until an accident with a car. The next scooter has 2 x 10mm2 busbars and this is what I use in my conversion kits. No problems with either 2 x 6mm2 or 2 x 10 mm2.
I think too actually.
Rule of thumb says 10A per 1mm2 which is why we are able to jank about 16A over 1,5mm2 solid copper wire here according the NEN1010 regulations, and i believe even 32A is allowed over 2,5mm2.
I think it differs if you used braided wire or solid copper. The latter is what i'm using.
I dont see how to use 3 busbars on 3 cells parallel because the middle busbar won't allow you to weld the tabs on the middle cell...
With 2 busbars each bar is between cells.
On another forum i'm in a discussion about these multl parallel or serial wiring between cells. The consensus there is that it is better to create long serial connections and only connect these serials on the ends, so no intermediate connections to prevent cross-cell-current flowing.
In this particular case its about connection the Vectrix NiMh cells in strings of 34 cells each and have these in parallel of 3. So its a 3P34S instead of 34S3P setup.
===================================
My contribution to EV in The Netherlands
- Novox C20
- Vectrix VX-1 Li+ my2009 #2791
- Vectrix VX-1 Li my2011 #3228
- CityEl Fact4 / Mini El Cabrio
- Th!nk PIV4 A266
- Th!nk City A306
- Tesla Model3 AWD
I do have a lot of trouble getting mail though my systems lately because of the heavy spam filtering, in and out, so im not always up to date, sorry about that.
===================================
My contribution to EV in The Netherlands
- Novox C20
- Vectrix VX-1 Li+ my2009 #2791
- Vectrix VX-1 Li my2011 #3228
- CityEl Fact4 / Mini El Cabrio
- Th!nk PIV4 A266
- Th!nk City A306
- Tesla Model3 AWD
The cells themselves will act as heat sinks, though long term keeping them cool is necessary for keeping capacity loss under control
my original 40Ah thundersky conversions used 25mm2 copper leaf conductors.
I used to keep the original temp sensors - I used to get temp warnings in summer (of course the LiFePO4 batteries could take a higher temp than the nimh cells could).
The original nimh cell interconnects are 48mm2 (I actually re-use these on the leaf module conversions)
Did you measure battery temperature in your original conversion?
I don't measure battery temp any more (to be honest), though I did for the early conversions
I^2R - doubling the current quadruples the heat, halving the resistance still means you have twice the heat.
current ratings have more to do with what temp rise you are willing to accept, what cooling the wire has, and how long the current will flow for.
I would suggest testing it on a small scale - you have a 100Ah?
I would push 100A through the wire continuous for an hour - that's basically the worst case scenario
you may find 2 x 16mm2 or 2 x 10mm2 to be sufficient, or you may not
Daily Ride:
2007 Vectrix, modified with 42 x Thundersky 60Ah in July 2010. Done 194'000km
I agree for lossy batteries (lead acid, nimh, etc) keeping track of and managing the side reactions is important.
nimh in particular has a falling voltage at full charge which is disastrous in a parrallel situation
I would suggest it's irrelevant for lithium batteries (all variants). The lithium batteries we are using don't have side reactions within their normal operating window. 2 or 3 in parrallel probably won't need fusing, any more and protection against internal shorts becomes necessary
Daily Ride:
2007 Vectrix, modified with 42 x Thundersky 60Ah in July 2010. Done 194'000km
Im not sure if that test would reflect whats going on with the Li battery. My setup is that every 3 cells in parallel are connected to the two busbars. So for the bottom piece of busbar where the last 3-cells are connected it only has to transport 30A max (10A per cell) in total so each busbar (i have two) transports 15A. The next piece of busbar further along the line will add the Amps for the next set of 3-cells so it adds 15A to each busbar, at that point 30A in total. For the next set of 3-cell, again adding 15A, and again, and again until the last set of 3-cell add their max current. So looking at the Amps at every 2cm (cells connections are aprox 2cm apart) along the busbar it would look like this: 15A - 30A - 45A - 60A - 75A - 90A - 105A - 120A - 135A - 150A. So its actually only the last 6cm of solid 16mm2 copper busbar that would transport over 100A (worst case scenario). The R of this short piece is close to nothing so i dont think it would warmup even noticeable transporting 100A or more.
BTW my busbar interconnections are made by 2 M6 bolt/nut so thats close to 60mm2 together.
The 48/50mm2 Vectrix wiring you are referring to is lesser then my interconnects so thats no problem at all.
My next setup of Li-pack which i'm currently building doesnt use sold busbars at all, but every set of 6 cells is connected by two 2,5mm2 or 4mm2 wires to the top. So each set of 6-cells can transport easily upto 80A max over these wires, good enough for 10A cells like the 29E. So for these 36P blocks i just need 6 wires on each side of the block to the interconnecting busbars at the top. Much easier to construct and each set of 6 cells could be fused (if wanted) very easily.
===================================
My contribution to EV in The Netherlands
- Novox C20
- Vectrix VX-1 Li+ my2009 #2791
- Vectrix VX-1 Li my2011 #3228
- CityEl Fact4 / Mini El Cabrio
- Th!nk PIV4 A266
- Th!nk City A306
- Tesla Model3 AWD
Here is the proof that the level fuses that Tesla uses in his battery , are not a "superflue" thing.
http://youtu.be/_IYXxGQ6Giw
Well thats more proof then ever that some people shouldn't drink the Dutch beer Heineken, its too strong for them...
He better had put the red wire in his left ear and the black wire in his right ear...
See what blows first....
===================================
My contribution to EV in The Netherlands
- Novox C20
- Vectrix VX-1 Li+ my2009 #2791
- Vectrix VX-1 Li my2011 #3228
- CityEl Fact4 / Mini El Cabrio
- Th!nk PIV4 A266
- Th!nk City A306
- Tesla Model3 AWD
Heres my latest 'toy' :-)
Fully automated CNC spotwelder for lithium packs....
Packs with these black brackets as seen on the movie dont fit very efficient in the Vectrix though.
I'm working on another setup to make it work.
https://m.youtube.com/watch?v=n1fZsSDsY_c
===================================
My contribution to EV in The Netherlands
- Novox C20
- Vectrix VX-1 Li+ my2009 #2791
- Vectrix VX-1 Li my2011 #3228
- CityEl Fact4 / Mini El Cabrio
- Th!nk PIV4 A266
- Th!nk City A306
- Tesla Model3 AWD
Paul, that is looking great men. A fine machine for your next conversions.
My own project is coming a bit to a hold because i tried to solder the nikkel strips to the copper busbars.
The flat copper busbars are 3mm thick and will not get hot enough. I think i will drop that idea. Now I like to use a holenail(see pictures)
to attach the nikkel to the copper.
I don't know if that is a good idea, but it is a very robust attachment.
Anyone?
Hi,
I think it is some overkill using this copper chunks...
Why not go for layered nickel strip as busbar like i showed you ?
That's what you can weld and is by far the cleanest solution.
===================================
My contribution to EV in The Netherlands
- Novox C20
- Vectrix VX-1 Li+ my2009 #2791
- Vectrix VX-1 Li my2011 #3228
- CityEl Fact4 / Mini El Cabrio
- Th!nk PIV4 A266
- Th!nk City A306
- Tesla Model3 AWD
I agree with you that it is a overkill, but I have already bought the copper and have cut the nickel into small pieces.
The flat copper bushbars where the smallest I could get my hands on.
It would be a shame not to use it.
A small advantage of the thick copper is the issue of resistance and overheating I think.
Did you test your solution with the multiple layers of nickel strips?
Well, i finished welding my new batterypack 18650 Samsung 29E, total 36S36P. I did 5250 welds with the JP Spotwelder without any problems. :0
The next step was removing the old Li pack(30Ah). Thanks to all the good information on this forum removal was a piece of cake.
Btw: can i re-use the original BMS? exists a wiring diagram? I'm a little bit confused while the Li configuration is a lot different
then the configuration with the 18650 cells.
Nice work, I think you can re-use the BMS but I am not sure if there is a wiring diagram. There are 4 PCBs (0-3) one for up to 10 cells. I think it will be the easiest way to reconnect the new batteries to the connectors where the current one (cell 1-36)are. What I don't know is what will happen if you have only 36 instead of 40cells. I bought the BMS from vectrixparts. In my case it was wired cell 1-9 to BMS0 PCB, 10-18 BMS1 PCB, 19-27 BMS2 PCb and 28-36 BMS3 PCB. I hope this help a little bit and maybe someone else can help more.
Thx Rolli, all info will help. Two wires are connected to the bottom of each batterypack(20 cells). I am not sure but i think that they are temp.sensors? (black and white wires)
Hi Prensel! (
One question. When you accelerate in Vectrix, the value of low cell and the high cell give big diferences?Like low 3.6 and hi 3.75? (at rest the values are equal)
@Meridiaan I think you are right that this are the temp. Sensors for more I have to see the connectors where they are connected. But to keep this BMS you have to contact vectrixpart, because they have the right Firmware and know the wiring. I haven´t seen the BMS Firmware anywere. If you need help I have bought the BMS from them, maybe I can help.
@Vortex I am not Prensel but I have the same conversation. Sometimes I get the same differences but it depends on circumstances. Somtimes I have it then they disappear. In my case the differences are higher when I accelerate slow.(I see only Hi and lo)
I found very useful stuff on service.vectrixparts.com, thanks a lot, Rolli!!
Tks a lot.I believe this difference is because in this moment the environment temperature is (10º/12º)
How many Kilometers this battery pack have in this moment?
I'm nearing the 10.000km mark pretty soon :-)
The bike is driving almost daily, even in wintertime without any problem at all.
Current range is about +120km.
This 'proof-of-concept' has been succesfull and i will be able to sell these Vectrix-modules brand-new for sale pretty soon.
===================================
My contribution to EV in The Netherlands
- Novox C20
- Vectrix VX-1 Li+ my2009 #2791
- Vectrix VX-1 Li my2011 #3228
- CityEl Fact4 / Mini El Cabrio
- Th!nk PIV4 A266
- Th!nk City A306
- Tesla Model3 AWD
I'm interested!
Do you have an idea of the pack price?
Great Job, Prensel.
My conversion is still in progress (36S36P). I am waiting for several parts from Poland.
I recently ordered a BMS adaptor and a BMS case from Vectrixparts. They advised me to re-use the former BMS Boards(Li+).
Together with new cables,a wire diagram and new software i should be able to re-install the BMS.
Maybe within a few weeks another Vectrix is on the road again!
My goal is a range of +130km.
Slightly off-topic, but I'm working on a conversion to A123 ANR-26650's. One question I have is what's the maximum voltage the controller can handle? I am replacing the charger, so that's not an issue. I can see they used a Vicor DC-DC converter and I know those have hard limits, but w/o unsoldering it, I can't see which model it is. Anyone know?
Incidentally, I have a whole bunch of NiMh cells from the original bike with about 4500 miles on them. One cell of the bunch failed and that in turn somehow caused the original charger to blow up as well.
I found this posted elsewhere on the forum:
I couldn't find part no. VE-251-01 on the Vicor website but I think any of the following could be used as a replacement:
VE-251-EU (VI-251-EU) Economy grade -10 to 85C ($181)
VE-251-CU (VI-251-CU) Commercial grade -25 to 85C ($274)
VE-251-IU (VI-251-IU) Industrial grade -40 to 85C ($398)
VE-251-MU (VI-251-MU) Military grade -50 to 85C ($687)
All of the above are rated 12V 200W output and have an input voltage of 150V nominal (100V minimum to 200V maximum)
Although the DC:DC converter can cope with up to 200V, there may be other components on the MC that can't.
Did the cell fail in an open circuit or closed circuit (completely shorted) state?
Did the cell fail during use, or while it was on charge?
Alan
I took the liberty of drawing an own BMS wiring diagram and sent it to Poland for comment.
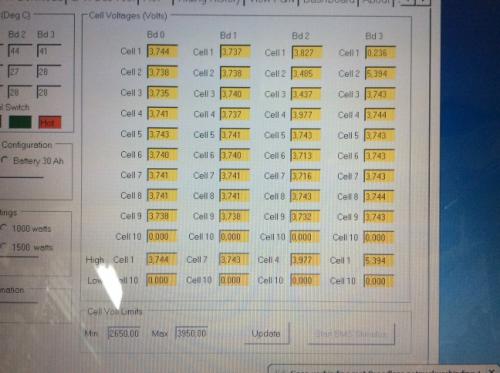
They approved and so I am back in business.
Did all the wiring and run a diagnostic with the diagnostic tool.
It came up with the following:
Whats wrong? I checked and double checked , the part of Bd 2 cell 1 to 4 and Bd3 cell 1 and 2 is very strange.
Pages