Hi,
I just got an XB-500 from someone on craigslist. They had it for 2 months and it worked fine. Suddenly it "just stopped working".
Over the course of the next 8 months they tried to figure out the problem, working with the Xtreme company thru warranty service. They had the motor tested. The controller, the batteries, the handbrakes, the throttle. All tested fine, but he was never able to get the thing going again. He finally gave up and bought a Honda Metro. He kept it (for 2 more years) hoping to eventually try again, dragged it along thru 2 moves, and was planning to move again, and decided he'd rather give it away for free than see it go into a landfill. This is where I come in.
Lucky enough to be the first responder, I now have this E bike, and I'd like to have it going for spring.
He gave it to me with the front panel off and controller disconnected from the wiring harness. I reconnected and installed the controller in the front of the bike, there are really only so many wires and they only fit in certain connections, so I think those are right. The control panel was also off ,and the wires all disconnected from the harness. I charged the batteries and tested them at 53.4 V after letting it sit for an hour off charger, so the batts seem to be holding a charge ok. I then plugged in the front panel to the wiring harness, matching plug sizes. When I turned the key,the dash lights turned on and the battery showed a full charge. The lights all work. I tried the throttle and the back wheel turned! I think I got something wrong though, when I turn on the blinker, the horn beeps with each blink. (the horn doesn't work using the horn switches) After awhile I tried the throttle again and it didn't work. So there is something going on with the wiring that isn't right.
The previous owner has 4 extra controllers, 2 extra brake handles and at least one extra throttle in the box full of stuff he gave me.
He says he rewired it 3 times. Other than the spliced wires going to the throttle and the gray wired "child safety switch", I don't see anywhere that he messed with the wires in the harness. It looks like he used friction tape. :O
I was hoping someone might have their front dash panel off for some modifications or repairs and could tell me where these plugs go for sure.
If I give where the wires come from and the size, maybe someone in this forum could tell me what color wires go into the correct plug I should use coming from the harness?
1) a 3 pin female coming from the light on/off switch.
2) a 2 pin red female coming from the battery meter.
3) a 2 pin male coming from the horn switches.
4) a 5 pin female coming from all the lights on the console.
5) a 3 pin male coming from the blinker switch.
6) a 1 pin male with a green wire.
What do you guys think? Is anyone out there able to help me re-cycle this e-cycle?
Thanks, Brenda
Well, I dont have an xb500 so I cant help with the wiring (I have an xb600). I do, however, think the problem sounds familiar. I believe another person on this sight had the problem with the horn and turn signals not working right causing the bike to not work. If I recall correctly it was the circuit board for the front assembly that controls the horn/signals/ etc. after he switched that out it worked. This problem could also be a bad dc/dc converter and/or one of the lights or brakes etc. could be shorting out.
Best thing I can say for now is to hook up only what you need to make it work... IE controller motor and throttle. Dont worry about the lights, horn, gauges, etc. Test it out, making sure to actually ride it to put a load on the motor, not only on the center kickstand. If it works, slowly hook up the other devices and re-testing. This will tell you where the problem is. If it doesnt work with just the motor/controller/converter and throttle, then the problem is elsewhere. You may also want to check the batteries individually, as I recently had a bad battery problem that seemed like a controller/motor problem.
Good luck to you
Dave ; Tennessee
XB-600.
Thanks, I'm going to check each cell to see if I have a bad one. It seems I get a response from the throttle when I 1st turn it on after a charge, but then it quits responding. If the cells are all good, I'm going to follow each cluster of wires back to the motor to see if there's any damaged wires/insulation. I think maybe I'll check the wire coming up the front of the steering column closer to look for a bad wire there too(the horn problem).
I'll post what I find out....
Thanks, Brenda
Did you get a circuit diagram with the bike, or from X-treme, or from somebody on this web site?
Buzzer
There are three kinds of people: Those who make things happen, those who watch things happen, and those who wonder what happened.
First thing I would do is put it on the center kickstand and plug in the charger. Then turn on the bike and try it. If it keeps running with the charger plugged in then it is a battery problem. If he did not keep them charged for those 2 years they are FOR SURE bad and even if they show 54V fully charged means nothing. After a few seconds of a load on them they will drop voltage quickly and the low voltage cutout in the controller will kick in stopping it from working. Once my old batteries hit 12.6V for each battery my motor would cutout. I had mine running at 60V so I didnt hit the LVC for about 10 minutes, but if I was running at 48V like you it prolly never would have worked.
To test the batteries properly you need something that draws a known current at 12V. I went to walmart and bought a set of driving lights for $15. They are 55W each for a total of 110W, and P=IV. power = current x voltage. So both of them hooked up to a fully charged battery should draw a rather constant 9.167V. This is a decent representation of the battery under load in the scooter. I then monitored the voltage over time. The bad batteries dropped kind of normally until they hit 12.6V at which time they dropped like a rock!!! IE in 5 minutes they would normally drop about .1-.3V but after they hit the 12.6V they would drop a volt in only a few seconds until they were useless.
Dave ; Tennessee
XB-600.
Another method of load testing is to get a cheap inverter, hook up a 100W AC load to that, & monitor voltage. Most inverters will have a low-voltage cutout or alarm that will keep from flattening the battery.
The controller has a brake input that shuts down output is the brake is activated. You should be able to find iit on the wiring diagram (which is available on this site).
I do have a copy of the wiring diagram, but the link on the EV downloads page directs me to some directory page, as does all the links from the downloads page.?
I tried the motor with the charger plugged in and the motor ran as long as I was giving it "gas". It did cut out when I tried the brake.I left it for awhile and tried it again and it still wasn't coming back on...
I'm thinking the batts probably are shot.
Do I leave the batteries connected to each other and just test using the terminals for the battery I'm testing, or do the batteries have to be disconnected from each other to be tested? I'd appreciate a detailed description of the process.
I was doing some research on the batteries and came across a place that has something you can hook up to your batteries to desulphate them while charging. It uses Random frequency pulsation to dissolve the sulphation crystals so they can return to the battery's electrolyte. It's supposed to prevent/reverse the sulphation of batteries. They claim that this can prolong your battery life considerably, especially if you live where there are longer periods between use/charges of the battery.
I thought that this might be particularly useful for those who use electric vehicles. They claim that if you can keep the specific gravity higher from having un-sulphated batteries,the electrolyte would be better able to generate more electrical energy-storage capacity than the previously sulphated batteries. Here's the link, http://www.batterystuff.com/battery-restoration/12-volt/OBD-12.html
What do you guys think about their claims? This device gets installed directly to the charging system and goes for about $45.
-Brenda-
I do have a copy of the wiring diagram, but the link on the EV downloads page directs me to some directory page, as does all the links from the downloads page.?
I tried the motor with the charger plugged in and the motor ran as long as I was giving it "gas". It did cut out when I tried the brake.I left it for awhile and tried it again and it still wasn't coming back on...
I'm thinking the batts probably are shot.
Do I leave the batteries connected to each other and just test using the terminals for the battery I'm testing, or do the batteries have to be disconnected from each other to be tested? I'd appreciate a detailed description of the process.
I was doing some research on the batteries and came across a place that has something you can hook up to your batteries to desulphate them while charging. It uses Random frequency pulsation to dissolve the sulphation crystals so they can return to the battery's electrolyte. It's supposed to prevent/reverse the sulphation of batteries. They claim that this can prolong your battery life considerably, especially if you live where there are longer periods between use/charges of the battery.
I thought that this might be particularly useful for those who use electric vehicles. They claim that if you can keep the specific gravity higher from having un-sulphated batteries,the electrolyte would be better able to generate more electrical energy-storage capacity than the previously sulphated batteries. Here's the link, http://www.batterystuff.com/battery-restoration/12-volt/OBD-12.html
What do you guys think about their claims? This device gets installed directly to the charging system and goes for about $45.
-Brenda-
Ok... When you apply the brake the motor is supposed to stop running. Are you saying that since u hit the brake it has not run again? If that is the case then it is prolly the brake switch sticking.... When u hit the brakes, either of them, does the brake light come on? or is it always "bright" like being in the on position? It DOES sound like there might be a problem with the front of the bike..... a circuit board (possibly the one that also controls the horn etc.) in the front may be bad causing the controller to think the brakes are applied and thus cutting off the motor. The motor is not supposed to work when either of the brakes are applied, thus a stuck or malfunctioning switch/board could be causing your motor to cut out or not work at all some times.
This is my recommended course of action....
#1 plug in the charger while on the kickstand. turn the bike on and lights all the way on. inspect all of the lights, blinkers, and brake lights. does the tail light get brighter and then dimmer when u apply and release the brakes? Do this several times, even 10-20 if you want to be sure. If the tail light never changes and seems rather bright, get some WD40 or other lubricant and spray into the brake lever area to try to unstick the switches.
If all of that checks out on to the next step.....
#2 while on the kickstand again and charger plugged in and bike turned on. apply the throttle all the way.... does it continue to run as long as u keep it on? when u hit either brake does the motor stop even with the gas on? When u release the brake does the motor start spinning again? try this several times with each brake. If all is good so far try testing the horn and turn signals while you are applying the gas. Do they all work?
If all of that checks out... on to battery testing...
#3 Test the batteries.... To do this correctly all batteries should be disconnected from one another. They should be individually charged using a 12V charger (once again, Walmart has a schumacher 12V 2/4/6A charger for around $20). Once it is fully charged you need to have something of a known Amperage draw. This can be anything you may have, as stated b4 I bought a set of 55Watt driving lights from Walmart for $15. The both of them connected to a 12V battery will draw (P=IV)(I=P/V) 110W/12V = 9.167 Amps. This is a rather good approximation of what the motor will draw to maintain a given speed. If the bike is "stock" ie no mods done to it, it can draw as much as 25A on hard acceleration and/or going up a steep hill. Yet i digress..... Something that is 120Watts at 12V would draw 10 Amps etc. Get settled in and comfy cause this may take a while now....
Either get a pen and paper or set with a text file on a laptop etc....
with a fully charged battery, record a voltage reading. Hook up your testing device (lights, inverter, whatever you have) and start recording a voltage reading at least every 5 minutes. If you notice the voltage dropping fast (more than .1-.2V every 30 seconds or so) record it more often and make note of the battery's voltage when this happens. A "bad" battery will probably only take 20-30 minutes or less to have the Large voltage drop to occur. If this large drop happens anywhere above 12.0V it is almost certainly bad.
You must repeat this for each battery separately and record the results. If you are in doubt, post the results here and myself or someone else will let you know.
You can charge all the batteries at once if you wire them in parallel... IE. all the + together and all the - together connected to the charger. This way they all should start VERY close to the same voltage. Of course if they show full at 13.7V per battery and by the time you get to testing the 3rd or 4th battery they are down under 13.0V chances are they are bad and wont hold a charge.
That is my suggestion... to do those tests in that order and let us know the outcome. There are only so many things on the bike that can be wrong... controller, motor, batteries, brake switch, or the dc-dc converter shorting out. It pretty much HAS to be one of those!!!
One other thing to check, if you are so inclined and think you can do it, is the find what wires coming from the controller are for the dc-dc converter, throttle, turn signals, and brakes. If it IS a faulty brake switch, disconnecting the brake switches(which will also disconnect the brake light response) should show whether or not they are to blame.
Awaiting your response.....
Dave ; Tennessee
XB-600.
The problem with that Desulfator is that it is only for 1 12V battery. You have 4 x 12V batteries in series for 48V. There are only a couple of ways you could use it. Use 1 for EACH battery = 4x desulfators. Use 1 desulfator and use it while u manually charge each battery separately. re-wire the bike for the series/parallel wiring setup as described in the xb600 collective handbook and use it while charging in parallel. I myself am waiting on the Anderson Powerpoles to be delivered so I can complete this to my bike. I just do NOT trust a single charger to charge the battery pack in series!!!! One way or another 1 or 2 batteries will eventually get unbalanced and cause problems in my humble opinion. I have the utmost confidence that my 12V 2/4/6A charger will work Extremely well to charge my 60V battery pack in parallel and give me the best possible performance and life from my batteries. Adding a Desulfator would probably even improve the performance and life as well.
Dave ; Tennessee
XB-600.
Thanks Dave, for the detailed instructions. I am going to start testing each of the things you mentioned, the brakes/lights etc. It has been in the 0-15 deg range here in Wisconsin for a week or so, so I've been waiting to do anything since the insulation on the wires and all plastic parts are as fragile as porcelain at those temps. I've left the trickle charge on to keep the batteries from freezing, and I want to do the brake/light testing first.
From how the bike has been working, it sounds just like what you described as a sticking switch or bad circuit board. The guy who gave it to me thought it might be just that, a faulty cutoff switch for the brakes/motor. Then, I'm hoping it'll get up around the 30's soon, and I'll go out(I have the bike in our unheated breezeway) and bring in the batteries and work on them in the basement.
As far as the desulphurator goes, do you think these old batteries could be restored using one of those? It might not be good for an ongoing or onboard use, but how about for rehabbing my batteries? $45 would be alot cheaper than buying 4 new 12V batteries....
-Brenda-
Honestly, I have no idea how well or IF the Desulfator would work on those batteries or any batteries in general. Then again, the only way you will ever find out is if someone who has used one and tested their batteries responds here, or you do it yourself. In that case you would need to do a load test on one of the batteries use the Desulfator a few times and test again.
Dave ; Tennessee
XB-600.
Dave, here's an update...
I had it on charger, tried the throttle, nothing. The tail lights go on when I turn on the dash lights, the brakelights respond correctly when I use the brakes(even thru the 20+ times each that I tested them), so it looks like the circuit board is bad? Is there an additional board inside the dash panel, or is the board your talking about in the controller?
I tested the horn(nothing still,using the horn switch) and the right blinker works correctly, a tone with each blink. The left blinker sounds the horn AND the tone w/each blink, but the bulb doesn't blink.
Could a short in the blinkers cause the motor not to run properly or do you think those are separate problems?
-Brenda-
I am not positive about the xb500... I know the xb600 has a few boards in the dash area. The fact that the horn does not work and it beeps when you use the left blinker means there is for sure a problem up there. If I recall correctly someone else on this site had a problem and it ended up being the circuit board in the dash that controls the horn and blinkers and makes the noise. It is possible the board is bad and sending a bad signal to the controller. There is also a possibility that there is a wire shorted out somewhere in the dash as well. If you have the wiring diagram for the controller I would try disconnecting all the wires that go to the dash except the ignition (you obviously need that) and the throttle. If it works like that then the problem is for sure in the horn/blinker/brake circuit board. If it still wont work, then that means that there is ALSO a problem with the controller or motor. You should at that point inspect all the wires from the controller to the motor. I am not sure how to do it, but there is a way to hook the motor up directly to that batteries for testing. just not sure how you would do that with the 3 phase wiring, perhaps someone else on this site could tell you how. Also, make sure you check the 2 fuses in the bike. There should be one in line with the ignition which is also the power to the dc/dc converter (on the xb600 anyways) and one in line between the battery pack and the controller. Now that I think of it, on the xb500 the controller is up in the dash area is it not? Some of the differences between the 500 and 600 could lead me to troubleshoot a little incorrectly. Lets hope someone with a little more experience with the xb500 chimes in here.......
Dave ; Tennessee
XB-600.
Here is an update as to this e-bike. I had my rummage and raised the $ for replacing the batteries. I have gotten the wires/connections sorted out and hooked up correctly(thanks to many posts on this site), and have the motor responding to the throttle. On the kickstand, the rear wheel turns, though it sound like it's stuttering. I took it out for a test drive, and I think I have bad news. The bike seems to have little power, with fluctuations of speed, kind of slightly lurching and then running at lower power,lurching and then running at lower power. Then it will completely lose power. If I let it rest, it will "work" again, doing the same thing.
Here's my question; Could this be the controller or throttle? Or worse, is this the motor? And,Is there a way to test the motor with a multimeter?
The guy I got this from said he used it for a couple of months and it worked great, then one day it just quit on him on the road. He tried working with Xtreme, who sent him controllers and brakes. After awhile they wouldn't give him any support because it had reached the one year warranty deadline. (He never did get it going again)
Does anyone have any ideas about this?
Brenda
Brenda,
I don't see were you established that you have a bad circuit board up front. Can you hook up just the controller, motor, throttle and key switch, and take a ride again. I am guessing you got new battries. XB-500 are coming down in price, you might want to pick another one up from CL, or ebay. You did not mention if you could buy a new front circuit board. Sometime it takes a long time to figure it out. In the mean time you are becoming an expert. Beware of pouring too much money into it. Good luck. Poe
Don't buy any futher away than you can drive to and return it.
bls makes one look up motorcyclewhse.com 119.00 not usual price of around 145.00 i ordered one for my evd wating for in to be delivered
At first, it sounded like maybe a bad circuit board or batteries. The batteries did turn out to be old/useless due to age and not having been kept charged by the prev. owner. I did replace the batteries, and did some research and found the only "boards" that are really on this bike are the controller and the dc/dc converter(the little box that lowers the voltage from 48V coming from the batteries to 12V for the lights/horn/etc that run on only 12V.
After working on getting the dash-controller-other wires all hooked up correctly, I find that those all work as they should, so I think that rules out the DC converter as a problem. That leaves the controller itself or the motor.
Next< I will try as suggested to run it with just what HAS to be hooked up;throttle,brake,power to the motor itself, and see if there is still the stuttering of the motor.
I'll post with the results....
-Brenda-
I think I can help you a bit.
I haven't read all the posts in this thread, so forgive me if I'm being redundant.
First of all, here is a link to the original wiring of an XB500:
http://bergerweb.net/xb500/XB500WiringDiagram.gif
Also, There is a lot of information about the XB500 on my website:
http://bergerweb.net/xb500/
Finally, If you look at the original schematic for the XB500, there is only one connector shown between the motor and the controller hall wires. (the five wires that go through a 6 pin connector between the motor and the controller. In reality, the wires that come from the motor are not long enough to reach to the front of the bike, so they actually go through an extension cable, and if I remember correctly, the color codes on the extension cable are not the same as the ones on the controller and on the motor. That can easily be a source of error in wiring, and it could easily be the cause of your motor vibrating instead of running smoothly forward.
Look closely at the schematic, and you will see that there are three power wires coming from the motor to the controller, and 5 thinner wires coming from the motor hall sensors to the controller. You will have to remove your seat to get to the ends of the wires coming out of the motor. Use an ohmmeter to check these wires for correctness. the big green wire from the motor must go to the big green wire on the controller. Likewise, the big blue and big yellow wires must match up. In turn, the hall wires (bundle of 5 wires going to the 6 pin connector) must also match up by color. (Red, Black, Blue, Green, Yellow from controller must go to the same colors on the motor. ignore the colors of the wires in the extension cable, as they do not match
The reason that it is important to get these wires connected properly is that the phasing of the power from the controller is controlled by the phasing of the hall signals coming from the motor. Reverse any two of them, and you will get one of these conditions:
It's also possible that the motor will not run at all in some combinations, but will start if you move the wheel by hand a little bit.
You can get a bit of an Idea about hub motor wiring and hall sensor phasing on the discussion on my website about building an electric bike. Go to this page:
http://bergerweb.net/electricbike and then click on IV - Controller Programming
Dickey_b
Waste Not, Want Not
I forgot something that's very important.
Several Xb-500 owners have had Axle Spin-outs. That's when the rear axle gets loose, and when you apply the throttle, instead of the wheel turning, the axle turns in the opposite direction. When this happens, it almost always damages the wires that go into the motor through the axle.
Before proceeding any further, check to see if this has happened. Telltale signs are the wires that go into the end of the motor axle will be twisted, and maybe broken. In some cases, if the wires become twisted, but not broken, the insulation will be damaged, and this can cause intermittent shorts, which will cause erratic things to happen when you apply throttle.
Another big problem is that the XB-500 comes with a very cheap fuseholder, which has a tendency to cause intermittent problems. Buy a new fuseholder at an auto parts store and replace the old one.
Good luck,
Dick
http://bergerweb.net/xb500
Dickey_b
Waste Not, Want Not
Dick,
Thanks for the info. I started like you suggested, Checking the axle and the wires going into it. Sure enough, there was visible damage once I peeled back the tape.
The wire sheath that was to protect the electrical wires was all mangled and broken. I could see the wires inside, and they were obviously twisted. I took off the wheel to get a little room to work on it, and took some pictures.
I untwisted the wires and you can see from the photos the insulation was damaged on more than one wire(causing my stuttering/dying power). Though all the wires were twisted, I found one thin green wire that was completely severed.(the others looked like they were still intact) I soldered that back together and coated the damaged insulation on all the wires with liquid electrical tape. After drying well, I bound them all back together with regular electrical tape. After reinstalling the wheel, tightening the axle nuts REALLY GOOD, and saying a prayer, I tried it out on the kickstand. I now have three speeds that it runs at!!(or maybe 2 because the 2 higher ones sound very much alike)
I wanted to take it out for a test run, but it rained here all day, ending with a 4 1/2 inch downpour that came down in a 2 hour span. (Milwaukee, WI. area)
One thing that definitely doesn't mix with these cheap made Chinese E-bikes is rain! I couldn't believe how poorly they were protected from any moisture.
I will post again after I take it out on a test run.
The spin-out was due to the loose axle nuts, correct?
Thanks, Brenda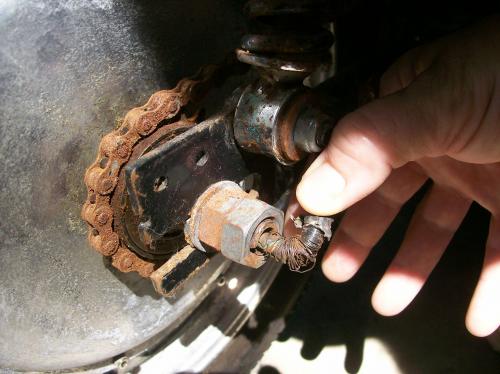
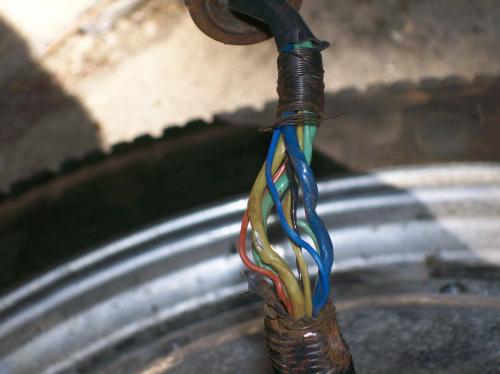
You might consider adding tabbed washers as are used on the XB600..
The oval holes in the washers engage the flats on the axle.
Mark
To MF70 - Looks like he might have the tabbed torque washers if you look really close at the photo of the installed axle above.
To BSTrue - Yes, the damage to your wires was indeed caused by axle spinout, and that was because the axle nuts were not tight enough. The correct torque for a 500W motor is 67 Ft/lbs. Borrow a torque wrench. Read my section on Assembling the bike on my website at
http://bergerweb.net/xb500/assembly.shtml
One other tip. The pedals on the bike are useless. Leave the chain off. You will have a more efficient bike. (Yours is rusty anyway)
Finally, looking at your photo, it looks like your blue wire may be damaged also.... the way it's stretched, there are at most a few strands still connected. I repaired one of these motors that had spun out, and I simply unsoldered all the wires, pulled them further into the case, and re-soldered the shortened cables onto the original connecting points. There is plenty of wire to allow you to cut off the damaged portion and pull the rest further into the case.
Dick Berger
Dickey_b
Waste Not, Want Not
As "useless" as the pedals are, they serve one vital purpose, they keep the vehicle legally classified as a bicycle. Depending on where you live, the laws may call for "functional pedals, capable of propulsion" some places go so far as to set the standard to capable of propelling the bike for a minimum distance of 3/4 mile on level ground. Aside from this, the poor quality of the components does make that a tempting idea for effeciency.
Hi Dick,
I took it out on the test run and though it was a bit better, it still had poor power and stuttered under load. When I was working on it, I was going to do just as you suggested, pull the wire into the hub further and re-solder it to good wire, but I couldn't get the wheel apart. I took all those little allen wrench bolts out on both sides but nothing would come apart. I also took all the nuts off one side of the axle. It seemed like it was one big cast piece of aluminum. I tried prying it apart with a screwdriver but there wasn't anyplace to get a grip. Any help on getting that darn thing apart would be greatly appreciated.
Also, I do have the tabbed washers, but I thought they were poorly placed because the flat of the washers didn't engage the flat of the axle very well on one side. One looked like it had almost rounded out. I did put them back on the same way they came off, but I think I should replace them. I'm going to see if I can get them from Xtreme, or if you know a better source....?
In the end I settled for repairing the most obvious wire break, but those wires are pretty thin and I suspect you are right, there is more damage and the best route is to go back to where the wire is solid and undamaged and re-solder directly to the original connecting points.
As far as the chain goes, I took it off and put it in a small coffee can I keep for a small amount of gas I use for cleaning parts. I figured I could clean it up/oil it when I got a chance, but I didn't plan on putting it back on. I'll have to see how touchy the police are in my area. I don't plan on using this on any streets posted over 25mph.
-Brenda-
P.S.
MF70, those were some great drawings there, very helpful blow up of the area! Was that added washer(flat plate lock washer) stock with your XB-600, or did you get that after? If I remember right, on the chain side, the XB-500 had 2 or 3 regular washers between the swing arm and the double nuts. The brake side only had one washer.
BSTrue,
There is a thread somewhere VIsForVoltage that describes how to get the XB500/600 Motor apart. I know it isn't easy, especially on an old one, but the sides do come off after you have removed all those allen screws. I didn't have much problem with the one I opened up, but I think I remember the thread on this website mentioning something about using a sharp knife to get into the edge of the cover, and striking the back of the knife with a hammer.
Search this website.... There are some photos and explanations of opening up a hub motor for this bike on this page:
http://visforvoltage.org/blog/gendronw/5196
Good luck
Dickey_b
Waste Not, Want Not