Hi,
you don´t need the voltage sensors. There are V´s without them on the road. Take a look at Stock BMS one of the last posts. I´ve seen temp.-boards
without the voltagesensors. All you have to to is to open a soldered contact on the board (disconected from battery and Scooter!)
In this case "SH1" was open and no wiring (V1,GND,V2) was soldered to the board. BUT: bevore soldering check the voltage on the disconnected
board, otherwhise the condesators may give you some "kick"
Greetings Mike
I Finaly found the Fotos!
Awesome, thanks. Will head off to try it now :)
@ Mik: I put the photos to the Collaborative Handbook
removed SH1 joint and 3 voltage sense wires. reconnected the battery. flashing temp and batt warning lights on start up. :(
but the charger did fire up on CC155 with a full fuel guage and step down to EC000 after a few minutes.
Drive seems normal (haven't tried it under load.
re soldered SH1, no charging.
Unsoldered, charging
unplugged front and rear temp cards. Charges, drives, still flashing batt and temp light. I think maybe I touched a temp sensor with my ICL while I was connecting it...
I'll ask the Vectrix Oz distributor if they have some temp boards for me to blow up.
Submitted by X Vectrix on Tue, 08/17/2010 - 10:44.
SH1 simply defines whether the PCB is for the front or back pack. It has nothing to do with the wires, other than they are both on the back PCB.
X Vectrix wrote this to the collaborative Handbook. I had a look to Mik´s photos, if I interpret the sheme of the battery right the back BMS board does the voltage
control, so maybe just try to open SH1 of the front board and close it on the back board.
the bike behaves the same boards plugged in or not. Makes me think either both are fried or what ever sees them is damaged :(
Still, it chargers and runs, so not a total loss.
Does anyone know, if the boards are unplugged do the temp and batt lights normally flash?
I got this info from another intrepid Lithiium-explorer:
disconnecting the two temp sensor boards resulted in flashing red lights, but everything else seemed to work.
Have you tried to connect the voltage sensor cables to somewhere appropriate on the new battery?
I thought one could also connect the voltage sensor cables to a resistor ladder that ALWAYS shows a nicely balanced battery to the stock BMS. Then you would not have flashing lights. But there might be some major flaw in my thinking, I have not tried this!
This information may be used entirely at your own risk.
I'm pretty sure the first time I hooked it all up, with the boards unmolested, just the voltage sensing cables rolled up and tucked away - there was no flashing. But no charging either. I had drive, but even then, I never saw anything but 21 degrees displayed.
It all seems to work other than the flashing lights. I still have to fit the MCU and the cycleanalyst before I take it for a spin.
I thought one could also connect the voltage sensor cables to a resistor ladder that ALWAYS shows a nicely balanced battery to the stock BMS. Then you would not have flashing lights. But there might be some major flaw in my thinking, I have not tried this!
I thought one could also connect the voltage sensor cables to a resistor ladder that ALWAYS shows a nicely balanced battery to the stock BMS. Then you would not have flashing lights. But there might be some major flaw in my thinking, I have not tried this!
Happy to try.
Got any ideas how to execute that?
Usually it's connected like this:
And this is how it might work with your Lithium battery (but it's completely untested!)
The big question is what resistor values to use for R1, R2 and R3.
I figure that the ration needs to be 27:48:27 , just like the cell numbers in the original battery.
For example: R1=27kohm; R2=48kohm; R3=27kohm.
This information may be used entirely at your own risk.
I'd like to have the battery voltage supply -to the MCU, Cycleanalyst and possibly this resistor series to trick the stock voltage detection- cut when the key is turned off.
I wonder if the auxilliary supply in the glove box could power one of these
OK guys,
This would have been much easier had you measured the voltage at the points V1SCL and V2SLD and ground before removing the original pack. With that said, you need to simply double the values of the resistors on the original divider. Since the original divider only saw half of the pack voltage, double the values of the shunt resistors (the resistors that go to ground) and the "sense resistors" (the resistors that go to each battery terminal).
For instance if Mik's schematic on the left side is correct (the one with the 2K and 200, double that value and use it for R2 and R3 on Mik's new schematic. I believe R1 will be close to 864K. When faced with this kind of issue, I like to use a resistor substitution box to arrive at the correct value for R1. You can use Ohms law to find the values and get real close, but being the type of nuts and volts guy I am, fine tuning the value with the sub box will arrive at the correct voltage the vectrix bms want to see.
Do not try to remove this divider circuit when the bike is off, leave it connected all the time like it was with the stock configuration. Make sure the shunt resistors never come undone, if they do the higher voltage will destroy the bms electronics.
OK guys,
This would have been much easier had you measured the voltage at the points V1SCL and V2SLD and ground before removing the original pack. With that said, you need to simply double the values of the resistors on the original divider. Since the original divider only saw half of the pack voltage, double the values of the shunt resistors (the resistors that go to ground) and the "sense resistors" (the resistors that go to each battery terminal).
For instance if Mik's schematic on the left side is correct (the one with the 2K and 200, double that value and use it for R2 and R3 on Mik's new schematic. I believe R1 will be close to 864K. When faced with this kind of issue, I like to use a resistor substitution box to arrive at the correct value for R1. You can use Ohms law to find the values and get real close, but being the type of nuts and volts guy I am, fine tuning the value with the sub box will arrive at the correct voltage the vectrix bms want to see.
Do not try to remove this divider circuit when the bike is off, leave it connected all the time like it was with the stock configuration. Make sure the shunt resistors never come undone, if they do the higher voltage will destroy the bms electronics.
Good Luck,
Louie
I'm not sure I understand what you are saying.
What do you mean with "the original divider saw only half the pack voltage"?
There is no "ground" connection in these diagrams. The Vectrix battery voltage is floating, I think, totally isolated from chassis ground.
Again, I may be totally wrong about all this, but I think the question to answer is this one: How much current does the original voltage divider need to function properly? (The original voltage divider is shown in the first diagram with all the resistors and capacitors comprising it; in the second diagram, the original voltage divider is only represented by the box labelled "Voltage and temp sensor board". But the original voltage divider is present in both diagrams.)
To use an extreme, but illustrative example:
If R1 and R3 were 2.7Mohm, and R2 were 4.8Mohm, then the current through the (proposed) additional voltage divider would only be 150V / 53.4Mohm = 2.8microA (dissipating 0.4mW as power loss).
But would the original electronics then "see" a much lower voltage, because they draw too much current in order to make the measurements?
This information may be used entirely at your own risk.
This beast measures the front pack voltage. The charger measures the whole pack voltage, therefor you can calculate the back pack voltage. Its wired this way so all the connections can be made on the back pack...that is, there are no connections that need to go to both the front and back pack. All connections are made as the F/R packs are assembled outside the bike. Then the F/R can be dropped in w/o having to make any inter-pack connections other than the anderson. But, the whole thing is moot, b/c none of this is actually used.
well.
removed SH1 joint and 3 voltage sense wires. reconnected the battery. flashing temp and batt warning lights on start up. :(
but the charger did fire up on CC155 with a full fuel guage and step down to EC000 after a few minutes.
Drive seems normal (haven't tried it under load.
re soldered SH1, no charging.
Unsoldered, charging
unplugged front and rear temp cards. Charges, drives, still flashing batt and temp light. I think maybe I touched a temp sensor with my ICL while I was connecting it...
I'll ask the Vectrix Oz distributor if they have some temp boards for me to blow up.
Hi,
maybe this could help:
Submitted by X Vectrix on Tue, 08/17/2010 - 10:44.
SH1 simply defines whether the PCB is for the front or back pack. It has nothing to do with the wires, other than they are both on the back PCB.
X Vectrix wrote this to the collaborative Handbook. I had a look to Mik´s photos, if I interpret the sheme of the battery right the back BMS board does the voltage
control, so maybe just try to open SH1 of the front board and close it on the back board.
greetings Mike
Didn't help.
the bike behaves the same boards plugged in or not. Makes me think either both are fried or what ever sees them is damaged :(
Still, it chargers and runs, so not a total loss.
Does anyone know, if the boards are unplugged do the temp and batt lights normally flash?
I got this info from another intrepid Lithiium-explorer:
Have you tried to connect the voltage sensor cables to somewhere appropriate on the new battery?
I thought one could also connect the voltage sensor cables to a resistor ladder that ALWAYS shows a nicely balanced battery to the stock BMS. Then you would not have flashing lights. But there might be some major flaw in my thinking, I have not tried this!
This information may be used entirely at your own risk.
There is always a way if there is no other way!
Ah, that's reassuring.
I'm pretty sure the first time I hooked it all up, with the boards unmolested, just the voltage sensing cables rolled up and tucked away - there was no flashing. But no charging either. I had drive, but even then, I never saw anything but 21 degrees displayed.
It all seems to work other than the flashing lights. I still have to fit the MCU and the cycleanalyst before I take it for a spin.
Happy to try.
Got any ideas how to execute that?
yup, that was me who tried to run without the cell management boards:
without the boards, the red lights always blink and the charger doesn't work.
interesting that yours charges and mine doesn't..... *jealous*.
I ended up buying an elcon 1500W charger as a replacement for the original.
Matt
Daily Ride:
2007 Vectrix, modified with 42 x Thundersky 60Ah in July 2010. Done 194'000km
Maybe different software on yours and mine Matt.
so did you just put black tape over your flashing lights, or have you found another solution?
I think the elcon is a better solution than the stock charger, more suitable charge profile
Usually it's connected like this:
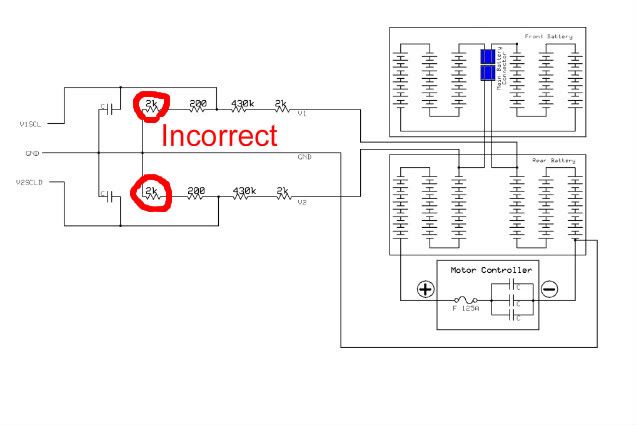
And this is how it might work with your Lithium battery (but it's completely untested!)
The big question is what resistor values to use for R1, R2 and R3.
I figure that the ration needs to be 27:48:27 , just like the cell numbers in the original battery.
For example: R1=27kohm; R2=48kohm; R3=27kohm.
This information may be used entirely at your own risk.
There is always a way if there is no other way!
1mA to run the loop.
I won't jump into this just yet. Maybe X Vectrix and others could have a look and advise.
thanks mik
here's another one for the electronics gurus
I'd like to have the battery voltage supply -to the MCU, Cycleanalyst and possibly this resistor series to trick the stock voltage detection- cut when the key is turned off.
I wonder if the auxilliary supply in the glove box could power one of these
solid state relay
OK guys,
This would have been much easier had you measured the voltage at the points V1SCL and V2SLD and ground before removing the original pack. With that said, you need to simply double the values of the resistors on the original divider. Since the original divider only saw half of the pack voltage, double the values of the shunt resistors (the resistors that go to ground) and the "sense resistors" (the resistors that go to each battery terminal).
For instance if Mik's schematic on the left side is correct (the one with the 2K and 200, double that value and use it for R2 and R3 on Mik's new schematic. I believe R1 will be close to 864K. When faced with this kind of issue, I like to use a resistor substitution box to arrive at the correct value for R1. You can use Ohms law to find the values and get real close, but being the type of nuts and volts guy I am, fine tuning the value with the sub box will arrive at the correct voltage the vectrix bms want to see.
Do not try to remove this divider circuit when the bike is off, leave it connected all the time like it was with the stock configuration. Make sure the shunt resistors never come undone, if they do the higher voltage will destroy the bms electronics.
Good Luck,
Louie
I had a bit of a worry for the moment, but it uses a mosfet for the gate not an SCR like most SSRs do.
yep that should be fine.
28mA to drive it max, the dc-dc shouldn't even know its there
you could also use the fan drivers to power it.
Matt
Daily Ride:
2007 Vectrix, modified with 42 x Thundersky 60Ah in July 2010. Done 194'000km
I'm not sure I understand what you are saying.
What do you mean with "the original divider saw only half the pack voltage"?
There is no "ground" connection in these diagrams. The Vectrix battery voltage is floating, I think, totally isolated from chassis ground.
Again, I may be totally wrong about all this, but I think the question to answer is this one: How much current does the original voltage divider need to function properly? (The original voltage divider is shown in the first diagram with all the resistors and capacitors comprising it; in the second diagram, the original voltage divider is only represented by the box labelled "Voltage and temp sensor board". But the original voltage divider is present in both diagrams.)
To use an extreme, but illustrative example:
If R1 and R3 were 2.7Mohm, and R2 were 4.8Mohm, then the current through the (proposed) additional voltage divider would only be 150V / 53.4Mohm = 2.8microA (dissipating 0.4mW as power loss).
But would the original electronics then "see" a much lower voltage, because they draw too much current in order to make the measurements?
This information may be used entirely at your own risk.
There is always a way if there is no other way!
This beast measures the front pack voltage. The charger measures the whole pack voltage, therefor you can calculate the back pack voltage. Its wired this way so all the connections can be made on the back pack...that is, there are no connections that need to go to both the front and back pack. All connections are made as the F/R packs are assembled outside the bike. Then the F/R can be dropped in w/o having to make any inter-pack connections other than the anderson. But, the whole thing is moot, b/c none of this is actually used.
nice idea, but the fans aren't on all the time in my bike
Faking out the voltage sensor probably deserves its own thread.
Pages