'R' again an interesting question. However, The pre-charge cooling delays, the left brake /kill switch operations and the lower cut-off voltage are all provided by the Motor Controller Software and I haven't got into that yet.
The altered hex charger hex file works in conjunction with the newer Motor Controller software BUT no longer decrements the fuel gauge. That causes a charge failure. Once the fuel gauge is full, the charger refuses to operate normally. It is another problem which I am trying to solve. Temporarily, using the earlier Motor Controller software solves that problem
In some ways, the short answer is NO.
Todd, I am ducking the question on Equalising for the moment. I am in the middle of tests which are taking longer than expected. I will report on that as soon as possible. The 80% charge is being completed in minimum time. Empty (which is more like 20%) to 80% takes 3.0 hours with the altered software against 1 hr 42 mins with the Vectrix software. For the moment, the extra hour (to 80%) is not a serious problem but I would like to improve that and I am working on that too.
The 'calibration charge'? The fuel gauge 'calibrates' to full when the battery is 'full' and to empty it calibrates on the 'red light'. Are you thinking of the equalisation charge?
The canbus adapter question has been answered by 'Mikemitbike' and his post raises some questions on instability.
I am not certain, but I suspect that the Canbus connector on the Vectrix may not be correctly terminated. This could give rise to Canbus instability at any time and could be the cause of those 'gremlins' which many of us have experienced. The use of a 'terminated' connecting lead might solve the problems which occasionally occur when a laptop is connected.
That brings the posts up to date. I shall check and answer messages as soon as possible.
Keep smiling:-)
The Laird.
(The impossible we do at once, Miracles take a little longer)
It looks like they are overseas though and I would like to order something here in the USA. Maybe someone has a suggestion for a US equivalent? Think I will post a new thread for this...
The canbus adapter question has been answered by 'Mikemitbike' and his post raises some questions on instability.
I am not certain, but I suspect that the Canbus connector on the Vectrix may not be correctly terminated. This could give rise to Canbus instability at any time and could be the cause of those 'gremlins' which many of us have experienced. The use of a 'terminated' connecting lead might solve the problems which occasionally occur when a laptop is connected.
Hi the Laird,
that was the reason I purchased a terminated connecting lead too (violet lead) [some of my old PC´s used Small Computer System Interface,
(SCSI) which needed termination too, long long Time ago ;-)]
But the Problem remains (maybe the old USB, as it gets worse with the USB extension) If I have news I´ll post them.
...
...
I am not certain, but I suspect that the Canbus connector on the Vectrix may not be correctly terminated. This could give rise to Canbus instability at any time and could be the cause of those 'gremlins' which many of us have experienced. The use of a 'terminated' connecting lead might solve the problems which occasionally occur when a laptop is connected.
...
...
The "official" advice from Vectrix was to use the non-terminated cable. I bought a terminated cable and took it apart, removed the resistors and so turned it into the non-terminated version. I never tried the terminated cable on the Vectux. Photos here: http://visforvoltage.org/book/ev-collaborative-hand-books/6916
There are 4, not 3 cables connected to the inside of the canbus connector in the Vectux glove box - and no resistor:
This information may be used entirely at your own risk.
...
The "official" advice from Vectrix was to use the non-terminated cable.
I never tried the terminated cable on the Vectux...
A big AHA from my corner. I used a terminated version till today... I´ll try a non terminated one when I use the adapter next time.
By the way, can there be a problem when you hook the Peak-Adapter direct to the CAN Port?
To terminate or not to terminate, that is the question.
All signal cables must be correctly terminated in order to prevent reflected signals appearing on the transmission line.
The problem is that double termination (terminating twice) causes a Loss of signal strength and NOT terminating causes reflections. Termination tales place at the end of the line. If the line is extended then the termination (usually a resistor) must be 'moved' to the end of the extended line.
If the CanBus adapter is itself terminated then there is no need for a 'terminated' connecting lead.
If the Plug in the glove box is not terminated correctly then this could be the cause of the random CanBus problems which many of us have had occur whilst riding and/or charging. (there are signals on the CanBus line at all times of operation). The short length of lead from the electrionics to the CanBus plug in the glove box may be long enough to cause these problems.
The can bus on the vectrix is fully terminated. There is no need for any more termination and would only squash the signal. Ideally the termination should be at the two furthest ends of the system but this is not always practical. Relatively speaking the scooter is a fairly small system.
THe port in the glove box also provides 5V and gnd for any devices that may need it.
The can bus on the vectrix is fully terminated. There is no need for any more termination and would only squash the signal. Ideally the termination should be at the two furthest ends of the system but this is not always practical. Relatively speaking the scooter is a fairly small system.
THe port in the glove box also provides 5V and gnd for any devices that may need it.
Thanks for the Info!, so I´ll use it without termination next Time by dissoldering the termination resistors in teh extensioncord.
Greetings Mike
It looks like the Can Adapter is ready for use as is. Don't forget to purchase the connecting lead also. It's on the same page at $29.00 'Un-terminated'.
Hello: most interesting thread...
If I were to modify the programme in order to charge a LifePo4 40Ah battery, is it possible to go around the 32Ah limit? How does the charger recognize that limit?
I would discourage anyone from loading modified code into their bikes. The charger and motorcontroller codes are paired and expect certain information to be transferred back and forth. If you mix and match codes you will not get this exchange, causing unpredictable behavior. The loss of the fuel gauge was already noted so this should send up a warning flag.
The original SW was designed to be adaptive to the pack capacity. Without the correct exchange between the MC and charger the charge cycle could incorrectly change over time such that charge cycles get too long or get real short.
If you really want to invest in the CANbus adapter and you somehow get the diagnostics, you would be much better off using the latest SW and following a simple procedure to initialize the SW so that the charge cycle is specific to your bikes capacity. There are many instances where the SW was never initialized or was initialized incorrectly for fear of running the pack down to the red light. Initialized correctly, the SW will measure the pack capacity and set charging limits accordingly. Or by changing a few setting you can force the system to treat the pack as if it were any lower capacity you wish, thereby reducing the charge cycle.
Heat problems are a sign of damaged cells whose capacity has been reduced. Any overcharging will heat them up.
Also beware, that one slight mishap during reprogramming and the bootloader can be lost, leaving you with an nonprogrammable bike. The diagnostics commands a certain sequencing to all modules during reprogramming (even if programming just one module) which is somewhat dependent on the modules communicating correctly.
Hi X Vectrix, is there any possibility for you to work that out with the Laird together?
Or is there a possibility that Vectrix offers a changed chargersoftware with that values
mentioned above? EQ charge with a lower rate would be great as the cells heat up very
much during a C/10 EQ Charge. Reading the Datasheet from GP C/20 or even C/30 would be
better. As far as I know the diagnostic-SW can change the fuelgauge by changing it´s
value, butI don´t remember that it can set the average battery capacity?
Your post is more than interesting. It is obvious to me that you know a lot more than most about the programming of the Vectrix charger and perhaps other Vectrix components.
I well understand your advice, to Vectrix owners, about NOT instaling 'altered software'. I too, would be unhappy if someone 'interfered' with programmes which I had developed. It is most unlikely that they would understand my thought processes which have influenced the patterns of behaviour of the software.
However, The Vectrix charger software is overcomplicated and, frankly, not fit for purpose/ up to the job. Even you cannot deny that there are issues with overheating the battery whilst charging, nor can you deny that battery failures are the most common problem suffered by the Vectrix bike and the old Vectrix corporation. Indeed, the problems were such that they added considerable costs to the guarantee system and produced an excessive workload in some cases.
Now, what I have been doing to the Vectric charger software is to change it's behaviour completely. By making subtle changes, I have forced the software to follow a totally different charging principle, whilst still following the original charging path. I have not changed the software, instead I have made it operate in a completely different way.
What I can assure everyone is, that the changes which I have made are far less likely to cause damage than the original software by Vectrix. I have already demonstrated that the 'altered' software results in less heating of the battery whilst charging. The 'fans on' whilst riding also helps to regularise and lower the temperatures throughout the battery. And all this with the smaller, less powerful plenum chamber fans (total fan power is now 12.5 Watts Yes, that's both fans) which I have substituted in my own Vectrix Scooter.
I think that I have improved on the original Vectrix programme, What is more, I am not keeping secrets.
I think that, with what you know, and what I can do, we two could improve the Vectrix much more and much more quickly.
I haven't gotten into the Motor controller software yet but I will, and when I do I have lots of ideas for improving that too.
I said that I don't keep secrets, so how about a bit more openness. I have legal use to the title 'Laird of Camster' hence my using the pen name 'The Laird'. My everyday name is Edward Sandy Gorst, I am a retired electronics engineer and have a very broad experience background which includes the Design and Customising of complex computer controlled security systems. I have taught Electronics to degree level students and have designed and built custom devices to customer requirements and I have some knowledge and experience of computer programme writing. I live in the Isle of Man. My e-mail is MyName [at] manx.net.(The_laird) If you need my full address, then just ask, there is no secret.
Now, just who are you? Will you contact me with a view to improving the Vectrix software? If you don't wish to contact me via the forum, why not use my e-mail address? I shall treat anything you send as confidential if that is what you wish.
If you need any further assurance that I have some knowledge of what I am doing, then please ask.
I hope that the negative comments concerning my posts on the forum will now cease. I am delighted to have constructive criticism, it all helps to improve the future, but negative comments, without 'full knowledge' of what I am doing, are just a little bit irritating and, arguably erroneous.
I look forward to hearing from you, either on the forum or privately. I think that we could do business together.
These sort of concerns have kept me from changing the Vectux firmware so far. I have heard of instances where the firmware update went wrong even in the hands of experienced Vectrix technicians, resulting in a dead bike (at least temporarily, I don't know how it got fixed in the end, but apparently it was. Maybe a motor controller exchange?)
But I have also heard of rough-and-ready Aussie characters willing to take big risks, like riding the Vectrix with only one planetary gear to reduce the noise, and some changing the firmware frequently in various combinations to try it out. It seems one can get away with it if one is lucky.
Another main reason for me not changing firmware so far is that Vectrix most likely know who I am, and I don't like getting sued for copyright breaches or anything similar. I like to be able to describe what I have done with my Vectux without such fears.
Another reason is that the newer software versions have reduced the engine power. That might be good, but I bought the Vectrix because I wanted something with the advertised specs (stupid me) and I do not want to reduce the available power any further. It's lame enough off-the-line as it is!
But the main reason is that the ABCool with a dual timer achieves many of the objectives required to improve the old software versions. I don't recall ever reading or hearing a reply to my ABCool posts which pointed out any valid concerns for risk or danger resulting from it's use. The only reason people did not adopt the simple and reliable concept was that they still had a warranty (or at least a belief in a warranty). It requires some thinking effort to choose appropriate charging times when setting the timers, but the original safeguards (over-temp detection, over-voltage detection) remain fully functional and will put a stop to charging if the ABCool time was chosen wrongly. So unlike The Lairds software changes, you might still get the occasional charge ending in some heating, but most of the time all of the main objectives for the software changes would be met:
- avoiding charging to more than 80% SOC.
- pre and post charge cooling.
- in-ride impeller cooling.
What the ABCool cannot do is reduce the charge current and at the same time the charger mains current draw. That would be such a nice feature to have! My ageing Honda i20 could then charge the Vectux. I also have a 5kW sine wave inverter now, and this could live in the boot of my NHW10 Prius and charge the Vectux if the peak power requirements were reduced somewhat. Then the NHW10 could serve as a companion vehicle for long Vectux rides and as a roadside assistance vehicle.
Something the ABCool can do, which neither the original nor The Laird's firmware can do (yet), is to start and stop delayed charging at specific times, for specific lengths of time. That work a treat in heat conditions. Like this: Start impellers at 0200am, start charger at 0600am, stop charger at 0700am and then ride to work (20-30km) with a battery at 80% SOC and with a battery temperature equal to the lowest ambient temperature occurring during the season/heatwave.
This information may be used entirely at your own risk.
@X-vectrix or whoever has teh anzwer ;)
"The original SW was designed to be adaptive to the pack capacity."
Does this mean that, if I were to replace the pack with a 40Ah or even 60Ah of equal nominal voltage, the system would read by itself the capacity if and when the software is correctly initialized?
Thank you.
If I go for a new battery pack I don't know if I'd go for all the modifications involved with the fitting of 60Ah cells, but just out of curiosity, how does the MC deal with the new charger?
the charger firmware in original form will only measure battery capacity up to 32Ah...
Hi, an other way (if you have a PEAK-Canbus-adapter and the scooterdiagnostic-software) is to reduce the
value for the fuel gauge. If you decrease from 17 to one or two bars, the charger try to fill the battery
again with ~30Ah. A little bit tricky and dangereous, because the possibility to overcharge the installed
battery and/or bringing the battery-gauge out of sync.
If I go for a new battery pack I don't know if I'd go for all the modifications involved with the fitting of 60Ah cells, but just out of curiosity, how does the MC deal with the new charger?
If going 60Ah cells, make sure you use WB (used to be known as thundersky).
CALB ones are the wrong shape.
The MC doesn't care what charger is attached, it will still work the same.
If you change the charger, the fuel guage will become a voltage guage (17 bars = ~134v, 0 bars =<108v IIRC)
the charger firmware in original form will only measure battery capacity up to 32Ah...
Hi, an other way (if you have a PEAK-Canbus-adapter and the scooterdiagnostic-software) is to reduce the
value for the fuel gauge. If you decrease from 17 to one or two bars, the charger try to fill the battery
again with ~30Ah. A little bit tricky and dangereous, because the possibility to overcharge the installed
battery and/or bringing the battery-gauge out of sync.
I've tried that,
a bit cumbersome.
the charger in stock form has a max voltage of 153v (again IIRC).
153v across 42 cells is 3.65v average.
in order to use the charger without temp sensors, you need to run BCR2012 or earlier.
unfortunately for the fuel guage to work, that also means you need to run MC1014 or earlier.
that means top speed is back to 105kmh, instead of the 112kmh possible with MC1017.
Matt
Daily Ride:
2007 Vectrix, modified with 42 x Thundersky 60Ah in July 2010. Done 194'000km
The Vectrix Charging process - the latest/last? update Since January this year I have tested and proved the re-arranged software for the P1 charger. The results
of these tests show that it is possible to charge the battery without excessive heating therefore avoiding the damage that is caused by that excessive heating. I have located yet more information backing up the principles on which I have based the modified charger programme. This information relates to the Prius battery operating mode and remember that many Prius batteries are achieving a ten year plus life span.
The latest version of my modified programme provides for lower voltage charging, lower current charging, lower battery heating, a more even temperature of the individual cells throughout the battery both when charging and riding, Plenum chamber fan overrun following charging and riding and lowered cut off voltages and temperatures.
The result of all of this is that I have (on a battery in good condition) achieved a range of up to 38 miles (60.8km) and a regular 30 miles (48km) plus at speeds between 30 and 50mph (48 and 80kmph) and this without getting down to the 'red light' or having the battery temperature rise by more than 3 degrees C. (I admit that I no longer use full power at speeds above 30MPH nor do I do harsh acceleration, but I do use the available high speed, I just curb my enthusiasm with the 'throttle').
Charging time is now (up to) 3.5 hrs(maximum) to reach the 80% of full (giving about 20Ah of useful energy) and a further 4hrs maximum to reach 'Full' charge. If this seems a long charge time then consider this. The Vectrix charger programme runs for about 2.5 hrs (C.P) 1hr (tr) about 2hrs (C.C) . If Equalisation is applied then a further 1hr cool off (C.O.) and up to 3hrs of equalisation (E.Q.) time is required. Total time 5.5hrs maximum without equalisation and up to 9.5hrs if equailisation is applied. Remember that the Vectrix charging system can raise the battery temperature to 50degrees C and some owners have seen these temperatures on their machines. The damage caused by the Vectrix charging process can be total and this has been seen in many bikes world wide. I have seen no damage to my battery by using my modified charging process, indeed, there are two bikes here, using my system, and the other bike owner is claiming an improvement in his bikes range since we fitted my modified software. Like me he has a cooler running battery and has noted no adverse effects.
The charger software I am working with is based on an early version, mainly because that is the one which I have learned most about and it also keeps the gauges on whilst in TR mode. I am using this software with the Motor controller MCR1017 which is the motor control software which provides the higher 'red light' voltage and the 'left brake/kill switch' voltage and temperature readout. This combination has it's problems, firstly the fuel gauge does not decrement when riding and secondly the estimated 'miles to go'/range does not decrement. The way that I deal with this is to use the 'left brake/kill switch' combination whilst riding ( I can now do this 'on the move') in conjunction with the miles travelled (using the trip distance indication) to judge the battery state /miles to go. The 'red' light still operates but is best avoided.
I have included a two hour (this can be changed if required - I have low power fans so it's not a problem to me) 'run on' for the plenum fans . This has (completely by chance) resulted in a choice as to whether to allow the fans to run on or not. Every second switch ON sets the fans running for two hours after switch OFF and the alternate switch ON stops the fans when the bike is turned OFF. The only 'down side?' is that the 'Temp' and 'Batt' red warning lights flash when the next 'switch Off' stops the fans. This state of affairs is repeated whilst charging, but is, I think, tollerable.
I have also fitted the resistors for 'bottom balancing' of the battery i.e. equalising by running the battery voltages low instead of by overcharging. This appears to work well but I am beginning to suspect that, with the cooler running battery, imbalance is no longer the problem that it was when using the 'Vectrix' charging routine/software.
This may well be my last posting as I rather feel that the expense in time and effort required to re-arrange the programming of the motor controller (required to prevent the damage caused by excessive current drain on the battery and excessive current charge by regenerative braking) can not be justified. The Vectrix organisation (in which I am certain 'XVectrix' is a major player) is unwilling to listen to my suggestions for improvement with the result that the programme alterations are extremely difficult to implement (with Vectrix's co-operation it would be a pushover).
I shall keep my Vectix as an item of historic/technical interest. It was the first Electric bike which was capable of 60MPH, has reasonably good acceleration and looks good. But, in all other respects it is a failure. It is over complex electronically and the reliability is very poor, with battery life unlikely to come anywhere near the advertised 50000miles, and the advertised range of 40 to 60 miles in average driving conditions simply unattainable.
I offer my very best wishes to all of you who own and ride the Vectrix bike, enjoy it while you can, and may the wrath of the Gods fall upon those cretins at Vectrix who have ruined a good product through their false marketing, greed and stupidity and their failures to listen to suggestions which could benefit us all.
The latest version of my modified programme provides for lower voltage charging, lower current charging, lower battery heating, a more even temperature of the individual cells throughout the battery both when charging and riding, Plenum chamber fan overrun following charging and riding and lowered cut off voltages and temperatures.
Have you found a way to allow charging without Ah limit by chance?
perhaps by removing the time limit on the CC stage?
cheers,
Matt
Daily Ride:
2007 Vectrix, modified with 42 x Thundersky 60Ah in July 2010. Done 194'000km
Matt, I am able to change many parameters, but only on one version of the software which is the 2012. changes possible include:-
C.P. - voltage, current/power, ampere hours, time limits. (C.P. can even be turned into Constant Current if needed) tr - current, no of cycles, cycle length (time) C.C. - Voltage, current, time limits, E.Q. - Voltage, current, time limits. The Battery input ampere hour limit can be changed. The Plenum fans can be made to 'run on' after switch off (time can be set) The Plenum fans can be made to run whilst riding (essential to maintain even cell temperatures).
No doubt this will all irritate XVectrix, (I do hope so anyway), but not as much as the engineers report which I intend to drop on the New Vectrix management when I get around to it.
In the mean time I will try to help all of you Vectrix 'Victims' out there where I can.
Mik,
I am happy to supply modified software to any Vectrix owner who wants to use it. I can offer no guarantees except to say that my modifications will damage the batteries far less than any of the charger software so far supplied by the Vectrix Corporation. You obviously fit and use this software at your own risk. If you are not satisfied then you can always revert the the Vectrix Software and thereby increase again the damage to your battery.
If anyone requires a copy of modified software, (It only works on the P1 chargers) send me a personal message with your e-mail address. Include the locality of use and the maximum ambient temperature which the bike will encounter and I will reply a soon as possible to you sending a copy of the hex code file and instructions for use.
Mik, some last thoughts on this. Currently, I am using low powered Plenum fans (12 watts total) and I have my fans to run on for two hours after switch off. This costs some 0.25 Ah for each run on, equivalent to about 1/3rd of a mile lost range. What are your thoughts on this? 'Run on' is essential, and with my fans a three leg journey would cost me a 1 mile loss of range. Choices are, reduce the run on time and/or change to low powered fans. Comments from other interested parties will be welcome.
Matt, I am able to change many parameters, but only on one version of the software which is the 2012. changes possible include:-
C.P. - voltage, current/power, ampere hours, time limits. (C.P. can even be turned into Constant Current if needed) tr - current, no of cycles, cycle length (time) C.C. - Voltage, current, time limits, E.Q. - Voltage, current, time limits. The Battery input ampere hour limit can be changed.
Thanks, very impressive.
I am able to change the Ah, however if I try to set it above 32Ah, it just behaves as if I set it to 32Ah :(
Do you know how high a time limit can be set for the CC stage time limit?
If I set the current to 9A, voltage limit to 153.3V and time limit to 7hours or more, than the original charger can be effectively used for a Lithium battery of any size.
Can the firmware be modified to allow the EQ charge on every cycle?
cheers,
Matt
Daily Ride:
2007 Vectrix, modified with 42 x Thundersky 60Ah in July 2010. Done 194'000km
...
... Mik, some last thoughts on this. Currently, I am using low powered Plenum fans (12 watts total) and I have my fans to run on for two hours after switch off. This costs some 0.25 Ah for each run on, equivalent to about 1/3rd of a mile lost range. What are your thoughts on this? 'Run on' is essential, and with my fans a three leg journey would cost me a 1 mile loss of range. Choices are, reduce the run on time and/or change to low powered fans. Comments from other interested parties will be welcome.
Best wishes to you all,
The Laird
Is this range reduction calculated with the lower power fans - and does it include the post-driving cooling or only the during-driving-cooling energy loss?
This information may be used entirely at your own risk.
Being as Constant Current can be obtained during C.P. as well as C.C.and even E.Q. 7hours and a voltage limit is achievable.
I haven't checked but I see no reason why E.Q. could not follow every charge cycle, I am puzzled as to why you might want to do that though?
Mik.
The range loss figures are based on a three leg journey and three stages of 2hours fan 'run on' using my low power fans. Your higher powered fans (all right Impellors) are five times more greedy and the range loss would therefore be greater by five times under the same conditions.
I have not accounted for the fan power consumption whilst riding as this would be almost insignificant. It is impossible to be accurate, but I theorise that the use of the fans whilst riding would keep the batteries cooler and the cell temperatures more even and this may well decrease the batteries internal losses thereby compensating for the power used to drive the fans. This would be difficult to measure even under laboratory conditions.
However,
A suitably reduced fan run on time might provide an easy answer to the 'problem' of this extra power consumption. Indeed, the other bike here is using a 10minute run on and so far that seems satisfactory with his higher powered fans. Remember that, for some unidentified reason, The two hours run on has a by product in the ability to turn off the fans every other use/charge cycle (it is probably caused by a 'flag' or 'counter' error generated in the delays - I really don't know) but it is reliable and is the only unintended consequence of the modified programme.
I hope that this answers your questions( if not, then we could discuss issues by e-mail?)
Being as Constant Current can be obtained during C.P. as well as C.C.and even E.Q. 7hours and a voltage limit is achievable.
I haven't checked but I see no reason why E.Q. could not follow every charge cycle, I am puzzled as to why you might want to do that though?
I think Matt wants to use this to increase the SOC of larger capacity Li batteries. The stock charger would perceive the EQ current as being lost to heat production, while it actually incrementally fills the Lithium batteries to Full SOC.
Mik.
The range loss figures are based on a three leg journey and three stages of 2hours fan 'run on' using my low power fans. Your higher powered fans (all right Impellors) are five times more greedy and the range loss would therefore be greater by five times under the same conditions.
I have not accounted for the fan power consumption whilst riding as this would be almost insignificant. It is impossible to be accurate, but I theorise that the use of the fans whilst riding would keep the batteries cooler and the cell temperatures more even and this may well decrease the batteries internal losses thereby compensating for the power used to drive the fans. This would be difficult to measure even under laboratory conditions.
However,
A suitably reduced fan run on time might provide an easy answer to the 'problem' of this extra power consumption. Indeed, the other bike here is using a 10minute run on and so far that seems satisfactory with his higher powered fans. Remember that, for some unidentified reason, The two hours run on has a by product in the ability to turn off the fans every other use/charge cycle (it is probably caused by a 'flag' or 'counter' error generated in the delays - I really don't know) but it is reliable and is the only unintended consequence of the modified programme.
...
The Laird
I think the energy/range loss is acceptable, but a shorter than 2hr cooling period would usually be better. This is because during hot times in Australia, the running cooling system would actually heat the battery. A 10min period of strong stock cooling will do a lot to equalise the temperature between cells after riding.
Does the alternating between cooling on and off only occur with the 2hr limit, or with any cooling time you program?
And do I understand this correctly: If you find the fans are not running when you turn the bike off, you turn it back on and back off and then they will run?
This information may be used entirely at your own risk.
can be obtained during C.P. as well as C.C.and even E.Q. 7hours and a voltage limit is achievable.
I haven't checked but I see no reason why E.Q. could not follow every charge cycle, I am puzzled as to why you might want to do that though?
I think Matt wants to use this to increase the SOC of larger capacity Li batteries. The stock charger would perceive the EQ current as being lost to heat production, while it actually incrementally fills the Lithium batteries to Full SOC.
Mik.
Close,
I was actually thinking I couldn't use the CP stage, as the "fuel guage" would always show full ie the charger always thinks the battery is already fully charged.
This is fine for both the CC and EQ stages.
So what I was thinking was set limits for
CC: 9A 153V 7+ hours
EG: 3A 154V 7+ hours
Thus having the correct charge profile without having to use the CP stage.
So the majority of the capacity is recharged quickly.
ideally the charger would skip to the next stage once the voltage limit is reached.
However, if we can use the CP stage, than this is best:
CP: 1500W 153V 7+ hours
CC: 3A 154V
EQ becomes unnecessary
I am rather hoping to be able to avoid having to replace the original charger when using CALB 70Ah cells (which may become 80Ah cells next year).
Matt
Daily Ride:
2007 Vectrix, modified with 42 x Thundersky 60Ah in July 2010. Done 194'000km
Hi folks,
Slow down, you're gaining on me.
Answers to posts.
'R' again an interesting question. However, The pre-charge cooling delays, the left brake /kill switch operations and the lower cut-off voltage are all provided by the Motor Controller Software and I haven't got into that yet.
The altered hex charger hex file works in conjunction with the newer Motor Controller software BUT no longer decrements the fuel gauge. That causes a charge failure. Once the fuel gauge is full, the charger refuses to operate normally. It is another problem which I am trying to solve. Temporarily, using the earlier Motor Controller software solves that problem
In some ways, the short answer is NO.
Todd, I am ducking the question on Equalising for the moment. I am in the middle of tests which are taking longer than expected. I will report on that as soon as possible.
The 80% charge is being completed in minimum time. Empty (which is more like 20%) to 80% takes 3.0 hours with the altered software against 1 hr 42 mins with the Vectrix software. For the moment, the extra hour (to 80%) is not a serious problem but I would like to improve that and I am working on that too.
The 'calibration charge'? The fuel gauge 'calibrates' to full when the battery is 'full' and to empty it calibrates on the 'red light'. Are you thinking of the equalisation charge?
The canbus adapter question has been answered by 'Mikemitbike' and his post raises some questions on instability.
I am not certain, but I suspect that the Canbus connector on the Vectrix may not be correctly terminated. This could give rise to Canbus instability at any time and could be the cause of those 'gremlins' which many of us have experienced. The use of a 'terminated' connecting lead might solve the problems which occasionally occur when a laptop is connected.
That brings the posts up to date. I shall check and answer messages as soon as possible.
Keep smiling:-)
The Laird.
(The impossible we do at once, Miracles take a little longer)
Thank Mike.
It looks like they are overseas though and I would like to order something here in the USA. Maybe someone has a suggestion for a US equivalent? Think I will post a new thread for this...
Todd
Hi the Laird,
that was the reason I purchased a terminated connecting lead too (violet lead) [some of my old PC´s used Small Computer System Interface,
(SCSI) which needed termination too, long long Time ago ;-)]
But the Problem remains (maybe the old USB, as it gets worse with the USB extension) If I have news I´ll post them.
Greetings Mike
Yes the equalization charge was what I was thinking of.
Todd
The "official" advice from Vectrix was to use the non-terminated cable. I bought a terminated cable and took it apart, removed the resistors and so turned it into the non-terminated version. I never tried the terminated cable on the Vectux. Photos here: http://visforvoltage.org/book/ev-collaborative-hand-books/6916
There are 4, not 3 cables connected to the inside of the canbus connector in the Vectux glove box - and no resistor: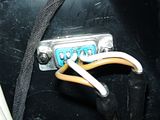
This information may be used entirely at your own risk.
There is always a way if there is no other way!
A big AHA from my corner. I used a terminated version till today... I´ll try a non terminated one when I use the adapter next time.
By the way, can there be a problem when you hook the Peak-Adapter direct to the CAN Port?
Greetings Mike
Hi there,
To terminate or not to terminate, that is the question.
All signal cables must be correctly terminated in order to prevent reflected signals appearing on the transmission line.
The problem is that double termination (terminating twice) causes a Loss of signal strength and NOT terminating causes reflections. Termination tales place at the end of the line. If the line is extended then the termination (usually a resistor) must be 'moved' to the end of the extended line.
If the CanBus adapter is itself terminated then there is no need for a 'terminated' connecting lead.
If the Plug in the glove box is not terminated correctly then this could be the cause of the random CanBus problems which many of us have had occur whilst riding and/or charging. (there are signals on the CanBus line at all times of operation). The short length of lead from the electrionics to the CanBus plug in the glove box may be long enough to cause these problems.
This should help to explain what is going on.
The Laird.
The can bus on the vectrix is fully terminated. There is no need for any more termination and would only squash the signal. Ideally the termination should be at the two furthest ends of the system but this is not always practical. Relatively speaking the scooter is a fairly small system.
THe port in the glove box also provides 5V and gnd for any devices that may need it.
Thanks for the Info!, so I´ll use it without termination next Time by dissoldering the termination resistors in teh extensioncord.
Greetings Mike
So does anything need to be done to the peak adapter or can it be used as is?
http://www.gridconnect.com/usbcanin.html
Todd
It looks like the Can Adapter is ready for use as is. Don't forget to purchase the connecting lead also. It's on the same page at $29.00 'Un-terminated'.
The Laird
Hello: most interesting thread...
If I were to modify the programme in order to charge a LifePo4 40Ah battery, is it possible to go around the 32Ah limit? How does the charger recognize that limit?
Thank you
I would discourage anyone from loading modified code into their bikes. The charger and motorcontroller codes are paired and expect certain information to be transferred back and forth. If you mix and match codes you will not get this exchange, causing unpredictable behavior. The loss of the fuel gauge was already noted so this should send up a warning flag.
The original SW was designed to be adaptive to the pack capacity. Without the correct exchange between the MC and charger the charge cycle could incorrectly change over time such that charge cycles get too long or get real short.
If you really want to invest in the CANbus adapter and you somehow get the diagnostics, you would be much better off using the latest SW and following a simple procedure to initialize the SW so that the charge cycle is specific to your bikes capacity. There are many instances where the SW was never initialized or was initialized incorrectly for fear of running the pack down to the red light. Initialized correctly, the SW will measure the pack capacity and set charging limits accordingly. Or by changing a few setting you can force the system to treat the pack as if it were any lower capacity you wish, thereby reducing the charge cycle.
Heat problems are a sign of damaged cells whose capacity has been reduced. Any overcharging will heat them up.
Also beware, that one slight mishap during reprogramming and the bootloader can be lost, leaving you with an nonprogrammable bike. The diagnostics commands a certain sequencing to all modules during reprogramming (even if programming just one module) which is somewhat dependent on the modules communicating correctly.
Hi X Vectrix, is there any possibility for you to work that out with the Laird together?
Or is there a possibility that Vectrix offers a changed chargersoftware with that values
mentioned above? EQ charge with a lower rate would be great as the cells heat up very
much during a C/10 EQ Charge. Reading the Datasheet from GP C/20 or even C/30 would be
better. As far as I know the diagnostic-SW can change the fuelgauge by changing it´s
value, butI don´t remember that it can set the average battery capacity?
Greetings Mike
Hi there XVectrix,
Your post is more than interesting. It is obvious to me that you know a lot more than most about the programming of the Vectrix charger and perhaps other Vectrix components.
I well understand your advice, to Vectrix owners, about NOT instaling 'altered software'. I too, would be unhappy if someone 'interfered' with programmes which I had developed. It is most unlikely that they would understand my thought processes which have influenced the patterns of behaviour of the software.
However, The Vectrix charger software is overcomplicated and, frankly, not fit for purpose/ up to the job. Even you cannot deny that there are issues with overheating the battery whilst charging, nor can you deny that battery failures are the most common problem suffered by the Vectrix bike and the old Vectrix corporation. Indeed, the problems were such that they added considerable costs to the guarantee system and produced an excessive workload in some cases.
Now, what I have been doing to the Vectric charger software is to change it's behaviour completely. By making subtle changes, I have forced the software to follow a totally different charging principle, whilst still following the original charging path. I have not changed the software, instead I have made it operate in a completely different way.
What I can assure everyone is, that the changes which I have made are far less likely to cause damage than the original software by Vectrix. I have already demonstrated that the 'altered' software results in less heating of the battery whilst charging. The 'fans on' whilst riding also helps to regularise and lower the temperatures throughout the battery. And all this with the smaller, less powerful plenum chamber fans (total fan power is now 12.5 Watts Yes, that's both fans) which I have substituted in my own Vectrix Scooter.
I think that I have improved on the original Vectrix programme, What is more, I am not keeping secrets.
I think that, with what you know, and what I can do, we two could improve the Vectrix much more and much more quickly.
I haven't gotten into the Motor controller software yet but I will, and when I do I have lots of ideas for improving that too.
I said that I don't keep secrets, so how about a bit more openness. I have legal use to the title 'Laird of Camster' hence my using the pen name 'The Laird'. My everyday name is Edward Sandy Gorst, I am a retired electronics engineer and have a very broad experience background which includes the Design and Customising of complex computer controlled security systems. I have taught Electronics to degree level students and have designed and built custom devices to customer requirements and I have some knowledge and experience of computer programme writing. I live in the Isle of Man. My e-mail is MyName [at] manx.net.(The_laird) If you need my full address, then just ask, there is no secret.
Now, just who are you? Will you contact me with a view to improving the Vectrix software? If you don't wish to contact me via the forum, why not use my e-mail address? I shall treat anything you send as confidential if that is what you wish.
If you need any further assurance that I have some knowledge of what I am doing, then please ask.
I hope that the negative comments concerning my posts on the forum will now cease. I am delighted to have constructive criticism, it all helps to improve the future, but negative comments, without 'full knowledge' of what I am doing, are just a little bit irritating and, arguably erroneous.
I look forward to hearing from you, either on the forum or privately. I think that we could do business together.
Best wishes,
The Laird (Sandy)
These sort of concerns have kept me from changing the Vectux firmware so far. I have heard of instances where the firmware update went wrong even in the hands of experienced Vectrix technicians, resulting in a dead bike (at least temporarily, I don't know how it got fixed in the end, but apparently it was. Maybe a motor controller exchange?)
But I have also heard of rough-and-ready Aussie characters willing to take big risks, like riding the Vectrix with only one planetary gear to reduce the noise, and some changing the firmware frequently in various combinations to try it out. It seems one can get away with it if one is lucky.
Another main reason for me not changing firmware so far is that Vectrix most likely know who I am, and I don't like getting sued for copyright breaches or anything similar. I like to be able to describe what I have done with my Vectux without such fears.
Another reason is that the newer software versions have reduced the engine power. That might be good, but I bought the Vectrix because I wanted something with the advertised specs (stupid me) and I do not want to reduce the available power any further. It's lame enough off-the-line as it is!
But the main reason is that the ABCool with a dual timer achieves many of the objectives required to improve the old software versions. I don't recall ever reading or hearing a reply to my ABCool posts which pointed out any valid concerns for risk or danger resulting from it's use. The only reason people did not adopt the simple and reliable concept was that they still had a warranty (or at least a belief in a warranty). It requires some thinking effort to choose appropriate charging times when setting the timers, but the original safeguards (over-temp detection, over-voltage detection) remain fully functional and will put a stop to charging if the ABCool time was chosen wrongly. So unlike The Lairds software changes, you might still get the occasional charge ending in some heating, but most of the time all of the main objectives for the software changes would be met:
- avoiding charging to more than 80% SOC.
- pre and post charge cooling.
- in-ride impeller cooling.
What the ABCool cannot do is reduce the charge current and at the same time the charger mains current draw. That would be such a nice feature to have! My ageing Honda i20 could then charge the Vectux. I also have a 5kW sine wave inverter now, and this could live in the boot of my NHW10 Prius and charge the Vectux if the peak power requirements were reduced somewhat. Then the NHW10 could serve as a companion vehicle for long Vectux rides and as a roadside assistance vehicle.
Something the ABCool can do, which neither the original nor The Laird's firmware can do (yet), is to start and stop delayed charging at specific times, for specific lengths of time. That work a treat in heat conditions. Like this: Start impellers at 0200am, start charger at 0600am, stop charger at 0700am and then ride to work (20-30km) with a battery at 80% SOC and with a battery temperature equal to the lowest ambient temperature occurring during the season/heatwave.
This information may be used entirely at your own risk.
There is always a way if there is no other way!
@X-vectrix or whoever has teh anzwer ;)
"The original SW was designed to be adaptive to the pack capacity."
Does this mean that, if I were to replace the pack with a 40Ah or even 60Ah of equal nominal voltage, the system would read by itself the capacity if and when the software is correctly initialized?
Thank you
the charger firmware in original form will only measure battery capacity up to 32Ah.
in theory you could scale the original byte used for counting Ah, for a greater range.
incidentally, 32Ah works out to be the usable capacity of a TS or SE 40Ah cell above 1C (or above 40A continuous).
the original charger will still be able to fully charge a 40Ah cell pack, even if you do take more than 32Ah out of it.
after charging 32Ah during the CP stage, the charger will continue at 3A for usually an hour or so.
with a 60Ah pack (like mine) or even larger, its easier to just use a cycle analyst and an elcon charger.
Matt
Daily Ride:
2007 Vectrix, modified with 42 x Thundersky 60Ah in July 2010. Done 194'000km
Thank you.
If I go for a new battery pack I don't know if I'd go for all the modifications involved with the fitting of 60Ah cells, but just out of curiosity, how does the MC deal with the new charger?
Hi, an other way (if you have a PEAK-Canbus-adapter and the scooterdiagnostic-software) is to reduce the
value for the fuel gauge. If you decrease from 17 to one or two bars, the charger try to fill the battery
again with ~30Ah. A little bit tricky and dangereous, because the possibility to overcharge the installed
battery and/or bringing the battery-gauge out of sync.
If going 60Ah cells, make sure you use WB (used to be known as thundersky).
CALB ones are the wrong shape.
The MC doesn't care what charger is attached, it will still work the same.
If you change the charger, the fuel guage will become a voltage guage (17 bars = ~134v, 0 bars =<108v IIRC)
I've tried that,
a bit cumbersome.
the charger in stock form has a max voltage of 153v (again IIRC).
153v across 42 cells is 3.65v average.
in order to use the charger without temp sensors, you need to run BCR2012 or earlier.
unfortunately for the fuel guage to work, that also means you need to run MC1014 or earlier.
that means top speed is back to 105kmh, instead of the 112kmh possible with MC1017.
Matt
Daily Ride:
2007 Vectrix, modified with 42 x Thundersky 60Ah in July 2010. Done 194'000km
The Vectrix Charging process - the latest/last? update
Since January this year I have tested and proved the re-arranged software for the P1 charger. The results
of these tests show that it is possible to charge the battery without excessive heating therefore avoiding the damage that is caused by that excessive heating.
I have located yet more information backing up the principles on which I have based the modified charger programme. This information relates to the Prius battery operating mode and remember that many Prius batteries are achieving a ten year plus life span.
The latest version of my modified programme provides for lower voltage charging, lower current charging, lower battery heating, a more even temperature of the individual cells throughout the battery both when charging and riding, Plenum chamber fan overrun following charging and riding and lowered cut off voltages and temperatures.
The result of all of this is that I have (on a battery in good condition) achieved a range of up to 38 miles (60.8km) and a regular 30 miles (48km) plus at speeds between 30 and 50mph (48 and 80kmph) and this without getting down to the 'red light' or having the battery temperature rise by more than 3 degrees C. (I admit that I no longer use full power at speeds above 30MPH nor do I do harsh acceleration, but I do use the available high speed, I just curb my enthusiasm with the 'throttle').
Charging time is now (up to) 3.5 hrs(maximum) to reach the 80% of full (giving about 20Ah of useful energy) and a further 4hrs maximum to reach 'Full' charge. If this seems a long charge time then consider this. The Vectrix charger programme runs for about 2.5 hrs (C.P) 1hr (tr) about 2hrs (C.C) . If Equalisation is applied then a further 1hr cool off (C.O.) and up to 3hrs of equalisation (E.Q.) time is required. Total time 5.5hrs maximum without equalisation and up to 9.5hrs if equailisation is applied. Remember that the Vectrix charging system can raise the battery temperature to 50degrees C and some owners have seen these temperatures on their machines. The damage caused by the Vectrix charging process can be total and this has been seen in many bikes world wide. I have seen no damage to my battery by using my modified charging process, indeed, there are two bikes here, using my system, and the other bike owner is claiming an improvement in his bikes range since we fitted my modified software. Like me he has a cooler running battery and has noted no adverse effects.
The charger software I am working with is based on an early version, mainly because that is the one which I have learned most about and it also keeps the gauges on whilst in TR mode. I am using this software with the Motor controller MCR1017 which is the motor control software which provides the higher 'red light' voltage and the 'left brake/kill switch' voltage and temperature readout. This combination has it's problems, firstly the fuel gauge does not decrement when riding and secondly the estimated 'miles to go'/range does not decrement. The way that I deal with this is to use the 'left brake/kill switch' combination whilst riding ( I can now do this 'on the move') in conjunction with the miles travelled (using the trip distance indication) to judge the battery state /miles to go. The 'red' light still operates but is best avoided.
I have included a two hour (this can be changed if required - I have low power fans so it's not a problem to me) 'run on' for the plenum fans . This has (completely by chance) resulted in a choice as to whether to allow the fans to run on or not. Every second switch ON sets the fans running for two hours after switch OFF and the alternate switch ON stops the fans when the bike is turned OFF. The only 'down side?' is that the 'Temp' and 'Batt' red warning lights flash when the next 'switch Off' stops the fans. This state of affairs is repeated whilst charging, but is, I think, tollerable.
I have also fitted the resistors for 'bottom balancing' of the battery i.e. equalising by running the battery voltages low instead of by overcharging. This appears to work well but I am beginning to suspect that, with the cooler running battery, imbalance is no longer the problem that it was when using the 'Vectrix' charging routine/software.
This may well be my last posting as I rather feel that the expense in time and effort required to re-arrange the programming of the motor controller (required to prevent the damage caused by excessive current drain on the battery and excessive current charge by regenerative braking) can not be justified. The Vectrix organisation (in which I am certain 'XVectrix' is a major player) is unwilling to listen to my suggestions for improvement with the result that the programme alterations are extremely difficult to implement (with Vectrix's co-operation it would be a pushover).
I shall keep my Vectix as an item of historic/technical interest. It was the first Electric bike which was capable of 60MPH, has reasonably good acceleration and looks good. But, in all other respects it is a failure. It is over complex electronically and the reliability is very poor, with battery life unlikely to come anywhere near the advertised 50000miles, and the advertised range of 40 to 60 miles in average driving conditions simply unattainable.
I offer my very best wishes to all of you who own and ride the Vectrix bike, enjoy it while you can, and may the wrath of the Gods fall upon those cretins at Vectrix who have ruined a good product through their false marketing, greed and stupidity and their failures to listen to suggestions which could benefit us all.
Telling it like it is, (as always),
The Laird.
Have you found a way to allow charging without Ah limit by chance?
perhaps by removing the time limit on the CC stage?
cheers,
Matt
Daily Ride:
2007 Vectrix, modified with 42 x Thundersky 60Ah in July 2010. Done 194'000km
Well done, The Laird! Are you happy to share the modified software?
This information may be used entirely at your own risk.
There is always a way if there is no other way!
Hi Matt, Mik, Everyone,
Matt, I am able to change many parameters, but only on one version of the software which is the 2012. changes possible include:-
C.P. - voltage, current/power, ampere hours, time limits. (C.P. can even be turned into Constant Current if needed)
tr - current, no of cycles, cycle length (time)
C.C. - Voltage, current, time limits,
E.Q. - Voltage, current, time limits.
The Battery input ampere hour limit can be changed.
The Plenum fans can be made to 'run on' after switch off (time can be set)
The Plenum fans can be made to run whilst riding (essential to maintain even cell temperatures).
No doubt this will all irritate XVectrix, (I do hope so anyway), but not as much as the engineers report which I intend to drop on the New Vectrix management when I get around to it.
In the mean time I will try to help all of you Vectrix 'Victims' out there where I can.
Mik,
I am happy to supply modified software to any Vectrix owner who wants to use it. I can offer no guarantees except to say that my modifications will damage the batteries far less than any of the charger software so far supplied by the Vectrix Corporation. You obviously fit and use this software at your own risk. If you are not satisfied then you can always revert the the Vectrix Software and thereby increase again the damage to your battery.
If anyone requires a copy of modified software, (It only works on the P1 chargers) send me a personal message with your e-mail address. Include the locality of use and the maximum ambient temperature which the bike will encounter and I will reply a soon as possible to you sending a copy of the hex code file and instructions for use.
Mik, some last thoughts on this. Currently, I am using low powered Plenum fans (12 watts total) and I have my fans to run on for two hours after switch off. This costs some 0.25 Ah for each run on, equivalent to about 1/3rd of a mile lost range. What are your thoughts on this? 'Run on' is essential, and with my fans a three leg journey would cost me a 1 mile loss of range. Choices are, reduce the run on time and/or change to low powered fans. Comments from other interested parties will be welcome.
Best wishes to you all,
The Laird
Thanks, very impressive.
I am able to change the Ah, however if I try to set it above 32Ah, it just behaves as if I set it to 32Ah :(
Do you know how high a time limit can be set for the CC stage time limit?
If I set the current to 9A, voltage limit to 153.3V and time limit to 7hours or more, than the original charger can be effectively used for a Lithium battery of any size.
Can the firmware be modified to allow the EQ charge on every cycle?
cheers,
Matt
Daily Ride:
2007 Vectrix, modified with 42 x Thundersky 60Ah in July 2010. Done 194'000km
Is this range reduction calculated with the lower power fans - and does it include the post-driving cooling or only the during-driving-cooling energy loss?
This information may be used entirely at your own risk.
There is always a way if there is no other way!
Hi Matt,
Being as Constant Current can be obtained during C.P. as well as C.C.and even E.Q. 7hours and a voltage limit is achievable.
I haven't checked but I see no reason why E.Q. could not follow every charge cycle, I am puzzled as to why you might want to do that though?
Mik.
The range loss figures are based on a three leg journey and three stages of 2hours fan 'run on' using my low power fans. Your higher powered fans (all right Impellors) are five times more greedy and the range loss would therefore be greater by five times under the same conditions.
I have not accounted for the fan power consumption whilst riding as this would be almost insignificant. It is impossible to be accurate, but I theorise that the use of the fans whilst riding would keep the batteries cooler and the cell temperatures more even and this may well decrease the batteries internal losses thereby compensating for the power used to drive the fans. This would be difficult to measure even under laboratory conditions.
However,
A suitably reduced fan run on time might provide an easy answer to the 'problem' of this extra power consumption. Indeed, the other bike here is using a 10minute run on and so far that seems satisfactory with his higher powered fans. Remember that, for some unidentified reason, The two hours run on has a by product in the ability to turn off the fans every other use/charge cycle (it is probably caused by a 'flag' or 'counter' error generated in the delays - I really don't know) but it is reliable and is the only unintended consequence of the modified programme.
I hope that this answers your questions( if not, then we could discuss issues by e-mail?)
Happy riding folks,
The Laird
I think Matt wants to use this to increase the SOC of larger capacity Li batteries. The stock charger would perceive the EQ current as being lost to heat production, while it actually incrementally fills the Lithium batteries to Full SOC.
I think the energy/range loss is acceptable, but a shorter than 2hr cooling period would usually be better. This is because during hot times in Australia, the running cooling system would actually heat the battery. A 10min period of strong stock cooling will do a lot to equalise the temperature between cells after riding.
Does the alternating between cooling on and off only occur with the 2hr limit, or with any cooling time you program?
And do I understand this correctly: If you find the fans are not running when you turn the bike off, you turn it back on and back off and then they will run?
This information may be used entirely at your own risk.
There is always a way if there is no other way!
Daily Ride:
2007 Vectrix, modified with 42 x Thundersky 60Ah in July 2010. Done 194'000km
Pages