I had a similar problem with the throttle reversing a while back it was caused by a red wire that had rubbed through and shorted against the rotating shaft on the electric motor
You will find the red wire in a loom that goes to the optical reader ...have a look at that
Thanks for the reply Martin.
2. I did remove the rear battery pack to get at the MC board. To remove the battery pack I first removed the top layer (2 banks) of batteries, this also meant that I had to remove the two temperature sensors, the front battery main interconnects (to the front battery pack) and the main red and black leads to the MC board. I am sure they are all back in the correct position and were tight.
I have disconnected the battery connections and retightened them and the battery is now charging at a steady 31c (this is still higher than my normal 23c~27c), but at least it is charging steadily now.
3. I agree that this might be a job for the proffesionals, I'll email them.
I don't have any PEAK cable or software, just normal tools.
I'll 'reset' the system later today and see if that cures it.
Hello,
never reverse the battery polarity at the controllers connectors ! The red wire from the battery (positive) must be connected to the big fuse. The battery wires are crossed on the way to the controller ! No one knows why Vectrix did this .
If the motor goes reverse instead of forward direction maybe you have connected the 3 motorphases in a wrong way ?
Hi Klaus,
The red lead is connected correctly so I'll leave it alone :-)
The motorphase cables are labelled A, B & C and are in the correct order. On my bike the A lead won't reach the C terminal so it is impossible to get these connections wrong.
Allan
If all except motor direction of rotation seems normal, it is very possible that you did NOT return the 3 large electrical leads from the motor to exactly the same positions they were at first. ( Reversing or switching positions, of any TWO of the motor leads will also reverse the motor rotation!)--- To correct the problem, disconnect the battery connector, wait about 30 minutes for the capacitor charges to discharge, and CAREFULLY remove and interchange any TWO of the heavy wires to the motor, making certain they are fully and properly secured and tightened, then, use a device to limit charging current, and carefully re-connect the battery, after this, rotation should return to normal.
Hi,
Ordinarily I would agree with you and I have thought long and hard about the correct connections for the motor. But, as you can see from the attached photos, they are reconnected in exactly the same order as they came off.
Before removing
and after installation
I am at a complete loss and my brain hurts :-(
Yes, the leads seem to be placed back in the original configuration!-Are the ENCODER LEADS also attached as at first?? If anything upsets the phase relation between the motor and encoder, rotation can be affected. Are there any wiring changes relative to the OLD controller board?--Carefully compare them.
Hi,
The boards look identical apart from my old board is Rev G and the new board is Rev J but I have no idea what changes have been made to the board by Vectrix. All the wiring connectors will only fit in one way round in their relevant sockets so it is not possible to get them wrong. I am tempted to switch the A and C leads around but I am wary of damaging the bike.
Allan
I assume your Vectrix has a NiMH battery and you did install the cover and both impellers were running when you charged the battery and it got to 47degC.
If those assumptions are correct, then your problem is the old "Recharge after BALPOR" issue: A recharge after a battery low point reset, in which the charger tries to force 30Ah or more into a battery that has a lower capacity than 30Ah. Perfectly normal that the battery gets hot in these circumstances, and very bad for the battery.
Regarding the wheel turning the wrong way round:
Considering that the motor controller and the encoder don't know each other yet, I think a encoder calibration is what will fix your problem. There is a magic sequence to do this involving key, brake levers and throttle. It's somewhere in the handbook. The rear wheel needs to be off the ground for this so it can rotate during the procedure.
What you need to do is the Motor Phase Test and the Motor Encoder Calibration.
For when you get the new fuse: You do not need to take the rear battery to pieces to get it out. You need to make some sort of lifter to attach to the tops of the studs that hold the rear battery modules down, then lift the rear battery out. However, it's very heavy and a hoist is a good idea.
This information may be used entirely at your own risk.
Mik you are a diamond geezer !
It is now working again - I couldn't be more happier :-)
Tomorrow I will clean all the panels and put it back together again for its first ride out in ages.
Thankyou all for your help and expertise, I couldn't have done it without you. I only wish Vectrix would have done the same :-(
Regarding the fans - yes, all fans were connected and the battery was 1/3rd full when it started the charging sequence.
Allan
Wow Allan that is great news. Well done Mik - I should have thought of that.
Allan, I really hope all your angst and hard work (and expense?) is rewarded with much happy motorcycling. Without wishing to gush too much, your perseverance and ultimate success is an example to us all and a credit to you.
As a side note, how have you got on with the ZEV in the meantime?
Best of luck. Martin Winlow.
Regards, Martin Winlow
Isle of Colonsay, Scotland
evalbum.com/2092
Dead MC board update.
I have decided to buy a secondhand slightly damaged board (not as bad as mine) and get a company to repair it here in the UK. I'll keep you posted on the out come.
My thanks to everyone here on V is for Voltage as without your help I would just have a pile of scrap. Many thanks to Dan & Scott for their extra help and at least now I have hope and a smile back on my face :-)
Did you let them have a look at the old damaged MC board as well? I'm still not convinced that it cannot be fixed...
This information may be used entirely at your own risk.
Hi Mik,
Yes, I took my old board along to the engineer to be looked at. After a brief smile and a laugh she confirmed what I already knew that 'if' parts could be found and 'if' they could be replaced then 'maybe' it 'might' function again. Also, she was very concerned about the plasma damage to the large beige coloured chip next to high voltage post. When I explained what had happened she asked why such high voltages where going through the board - I didn't have an answer - she was not very impressed with the design of the board :-( Unfortunately there were too many 'if's and 'maybe's in our conversation for me to even consider rebuilding the board. I am sending the dead board to another Vectrix rider in Australia (postage costs only) as it is of no use to me, maybe he can salvage it for parts.
I've been running the bike for about a week now and everything seems to be fine and my confidence is growing again :-)
I still have one slight problem, when charging, the temperature rises to about 30c, before the board blew it never went above about 23c. I know that this is within the charging tolerances from what I understand from other users so I am not too worried. I'll have to recheck the battery connections when I replace the fuse in a few weeks - assuming it arrives by then !
Allan
Hi to everyone watching my progress with the replacement board.
It appears that the new board has the old software (62mph). Am I in the unique position of having the original software, then the newer software and then back to the original software again ?
A few quite unexpected things have happened as a result of this software reversal.
(1) The battery no longer 'hiccups' after about 25 miles (this used to signal the steady reduction in speed and performance for the remaining 10 to 15 miles).
(2) The performance, although marginally slower acceleration, has improved for the better and is far smoother than it used to be.
Best of all (3) The range has increased ! I know I am not dreaming this as I kept accurate range testing records over the years to watch the decline of the batteries over its lifespan. Today I went out to do some shopping : on the motorway I did 62mph for about 3 miles, I then drove at 40~50 mph for the remainder of my journey. I drove quite hard as I was not planing a big trip so range was not my concern. On the way home I realised that the bike was performing quite well and the range was approaching 29 miles with no drop off in performance and no warning lights. I decided to drain the battery to the first 'busvlt' warning (as I usually do with range testing). To my amazement I got 36 miles of range before the bike slowed to 25mph (no 'busvlt' warning). Previously with this type of driving style I only got 32 miles of range.
Later this week I am going to do a 30mph (maximum) range test and see what happens - this usually gets me 37 miles if I am very careful. I'll pop the result on here later.
One thing is for certain - I won't be installing the newer software again.
Does anyone else have any insights into this behaviour ?
I'm working for the official VECTRIX Importer in Austria (MP-ecodrive GmbH). We have brandnew Motor Controllers and other spare parts in stock. In the last months we could help many customers with difficulties in organising spares, software problems and with pre delivery vehicles.
From deep conviction about electric mobility and as VECTRIX veteran we deal despite difficult times, especially with this topic.
If you choose the option to replace your Motor Controller, don't hesitate to contact us for a offer.
Allan kindly sent me this dead MC board for the cost of postage
I was able to repair it yesterday
Basically I used a dremell to cut away the burnt plastic, like I would for one of the phase connections.
The interesting part was electrically reconnecting the positive to the board, both for power for the bike, but mainly so the ceramic caps could do their job at keeping the voltage stable while the IGBT is doing it's switching
I soldered two eye crimp terminals onto the positive traces, after scraping off the conformal coating.
Today I put the repaired board back into service in a friends bike, whose MC had died (IGBT module on his board failed internally)
Allan kindly sent me this dead MC board for the cost of postage
I was able to repair it yesterday
Basically I used a dremell to cut away the burnt plastic, like I would for one of the phase connections.
The interesting part was electrically reconnecting the positive to the board, both for power for the bike, but mainly so the ceramic caps could do their job at keeping the voltage stable while the IGBT is doing it's switching
I soldered two eye crimp terminals onto the positive traces, after scraping off the conformal coating.
Today I put the repaired board back into service in a friends bike, whose MC had died (IGBT module on his board failed internally)
I will have to let you know when I install one, but it should be
The last one I bought was from china and I think that was second hand too
a brand new one is ~$40 more, if you're concerned that would be the way to go
I would be interested in what is involved in refurbishment
I have a few IGBT modules that have failed internally - not burnt out but the thermal cycling has caused the gates to become detached from the heatsink resulting in the over temp cutout being activated under acceleration, particularly at low speed
you don't normally see that failure mode till after 30'000km or more (the IGBT module used isn't designed for an automotive application with significant thermal cycling)
Given that many bikes are reaching that extent of use, I'm expecting to see a bit of a run of people with bad IGBT's
Daily Ride:
2007 Vectrix, modified with 42 x Thundersky 60Ah in July 2010. Done 194'000km
I have to get a quote on getting them tinned - but I'm looking at $8 - $10 per stud.
That would include a M5 bolt, and you have 3 choices of size:
16mm long for if you want to cut a hole in the board and bolt directly to the IGBT module
10mm long for if you want to just replace the original steel studs
28mm long for if you have had to repair a burnt out terminal and had to re-drill a hole in the copper tab coming out of the IGBT module
getting them made is surprisingly labour intensive
I'm getting copper tube cut and drilled on a lathe, then electroplated with tin
the copper studs I'm using have a conductor surface area of 107mm2, so should run cold (the battery interconnects on the nimh battery are 45mm2 for reference)
Daily Ride:
2007 Vectrix, modified with 42 x Thundersky 60Ah in July 2010. Done 194'000km
Let us know when they are ready, please. They'll go in the next time the MC board is out for some reason.
They're ready:
There's presently 3 sizes:
$7.50 - 10mm - can only be used on negative terminal and centre phase terminal
$8.50 - 16mm - for left and right phase terminals and the positive terminals, and any terminal where the PCB has been cut away
$9.50 - 28mm - for where a burnt out terminal has been repaired and a new hole had to be drilled in the IGBT module
Included is the correct size M5 bolt (between 10mm and 20mm longer than the stud), a pair of nordlock washers and if needed, a nyloc Nut.
the nyloc is only needed if you have cut away the backside of the IGBT module
Let us know when they are ready, please. They'll go in the next time the MC board is out for some reason.
They're ready:
There's presently 3 sizes:
$7.50 - 10mm - can only be used on negative terminal and centre phase terminal
$8.50 - 16mm - for left and right phase terminals and the positive terminals, and any terminal where the PCB has been cut away
$9.50 - 28mm - for where a burnt out terminal has been repaired and a new hole had to be drilled in the IGBT module
Included is the correct size M5 bolt (between 10mm and 20mm longer than the stud), a pair of nordlock washers and if needed, a nyloc Nut.
the nyloc is only needed if you have cut away the backside of the IGBT module
What would you suggest as a preventative modification?
I think it might be best to drill / dremel out all 5 terminals, so that the board is gone and the terminals connect straight to the undamaged IGBT module.
So 5 x 16mm needed?
This information may be used entirely at your own risk.
What would you suggest as a preventative modification?
I think it might be best to drill / dremel out all 5 terminals, so that the board is gone and the terminals connect straight to the undamaged IGBT module.
So 5 x 16mm needed?
The Positive and negative connections can't be drilled out, regrettably, at least not until we can work out a good way to solder the new studs to the board
but the 3 phase terminals, dremmelling out would be the best
I mis-measured the required stud lengths - I forgot about the washer and spring washer between the stud and the PCB
so that's why the 10mm versions exist - you need minimum 12mm to clear the hall sensors (although you can use the 10mm ones, the lug on the wire just bends down.
the 16mm versions were supposed to be for when you dremel out the holes for direct connection to IGBT, but they actually need to be minimum of 18mm long.
the 28mm stud is the correct length (thankfully)
I'm waiting to see what kinda demand there is for these lugs before committing another $700 to making a second batch
Matt
Daily Ride:
2007 Vectrix, modified with 42 x Thundersky 60Ah in July 2010. Done 194'000km
I had a similar problem with the throttle reversing a while back it was caused by a red wire that had rubbed through and shorted against the rotating shaft on the electric motor
You will find the red wire in a loom that goes to the optical reader ...have a look at that
rob white
Thanks for the reply Martin.
2. I did remove the rear battery pack to get at the MC board. To remove the battery pack I first removed the top layer (2 banks) of batteries, this also meant that I had to remove the two temperature sensors, the front battery main interconnects (to the front battery pack) and the main red and black leads to the MC board. I am sure they are all back in the correct position and were tight.
I have disconnected the battery connections and retightened them and the battery is now charging at a steady 31c (this is still higher than my normal 23c~27c), but at least it is charging steadily now.
3. I agree that this might be a job for the proffesionals, I'll email them.
I don't have any PEAK cable or software, just normal tools.
I'll 'reset' the system later today and see if that cures it.
Electric traction is the future.
Hello,
never reverse the battery polarity at the controllers connectors ! The red wire from the battery (positive) must be connected to the big fuse. The battery wires are crossed on the way to the controller ! No one knows why Vectrix did this .
If the motor goes reverse instead of forward direction maybe you have connected the 3 motorphases in a wrong way ?
regards
Klaus
Hi Klaus,
The red lead is connected correctly so I'll leave it alone :-)
The motorphase cables are labelled A, B & C and are in the correct order. On my bike the A lead won't reach the C terminal so it is impossible to get these connections wrong.
Allan
Electric traction is the future.
If all except motor direction of rotation seems normal, it is very possible that you did NOT return the 3 large electrical leads from the motor to exactly the same positions they were at first. ( Reversing or switching positions, of any TWO of the motor leads will also reverse the motor rotation!)--- To correct the problem, disconnect the battery connector, wait about 30 minutes for the capacitor charges to discharge, and CAREFULLY remove and interchange any TWO of the heavy wires to the motor, making certain they are fully and properly secured and tightened, then, use a device to limit charging current, and carefully re-connect the battery, after this, rotation should return to normal.
Robert M. Curry
Hi,
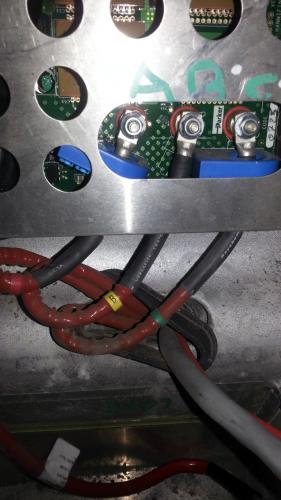
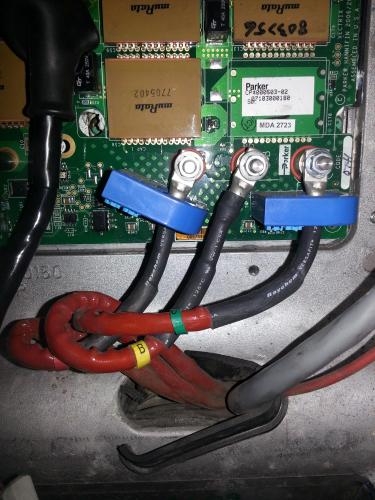
Ordinarily I would agree with you and I have thought long and hard about the correct connections for the motor. But, as you can see from the attached photos, they are reconnected in exactly the same order as they came off.
Before removing
and after installation
I am at a complete loss and my brain hurts :-(
Electric traction is the future.
Yes, the leads seem to be placed back in the original configuration!-Are the ENCODER LEADS also attached as at first?? If anything upsets the phase relation between the motor and encoder, rotation can be affected. Are there any wiring changes relative to the OLD controller board?--Carefully compare them.
Robert M. Curry
Hi,
The boards look identical apart from my old board is Rev G and the new board is Rev J but I have no idea what changes have been made to the board by Vectrix. All the wiring connectors will only fit in one way round in their relevant sockets so it is not possible to get them wrong. I am tempted to switch the A and C leads around but I am wary of damaging the bike.
Allan
Electric traction is the future.
Hi Allan,
I assume your Vectrix has a NiMH battery and you did install the cover and both impellers were running when you charged the battery and it got to 47degC.
If those assumptions are correct, then your problem is the old "Recharge after BALPOR" issue: A recharge after a battery low point reset, in which the charger tries to force 30Ah or more into a battery that has a lower capacity than 30Ah. Perfectly normal that the battery gets hot in these circumstances, and very bad for the battery.
Regarding the wheel turning the wrong way round:
Considering that the motor controller and the encoder don't know each other yet, I think a encoder calibration is what will fix your problem. There is a magic sequence to do this involving key, brake levers and throttle. It's somewhere in the handbook. The rear wheel needs to be off the ground for this so it can rotate during the procedure.
Edit: I found it: http://visforvoltage.org/book/ev-collaborative-hand-books/10431
What you need to do is the Motor Phase Test and the Motor Encoder Calibration.
For when you get the new fuse: You do not need to take the rear battery to pieces to get it out. You need to make some sort of lifter to attach to the tops of the studs that hold the rear battery modules down, then lift the rear battery out. However, it's very heavy and a hoist is a good idea.
This information may be used entirely at your own risk.
There is always a way if there is no other way!
Mik you are a diamond geezer !
It is now working again - I couldn't be more happier :-)
Tomorrow I will clean all the panels and put it back together again for its first ride out in ages.
Thankyou all for your help and expertise, I couldn't have done it without you. I only wish Vectrix would have done the same :-(
Regarding the fans - yes, all fans were connected and the battery was 1/3rd full when it started the charging sequence.
Allan
Electric traction is the future.
Wow Allan that is great news. Well done Mik - I should have thought of that.
Allan, I really hope all your angst and hard work (and expense?) is rewarded with much happy motorcycling. Without wishing to gush too much, your perseverance and ultimate success is an example to us all and a credit to you.
As a side note, how have you got on with the ZEV in the meantime?
Best of luck. Martin Winlow.
Regards, Martin Winlow
Isle of Colonsay, Scotland
evalbum.com/2092
Congratulations Allan, it's good to hear the gamble paid off and you got it going for a fraction of the cost of a new motor controller.
Did you let them have a look at the old damaged MC board as well? I'm still not convinced that it cannot be fixed...
This information may be used entirely at your own risk.
There is always a way if there is no other way!
Hi Mik,
Yes, I took my old board along to the engineer to be looked at. After a brief smile and a laugh she confirmed what I already knew that 'if' parts could be found and 'if' they could be replaced then 'maybe' it 'might' function again. Also, she was very concerned about the plasma damage to the large beige coloured chip next to high voltage post. When I explained what had happened she asked why such high voltages where going through the board - I didn't have an answer - she was not very impressed with the design of the board :-( Unfortunately there were too many 'if's and 'maybe's in our conversation for me to even consider rebuilding the board. I am sending the dead board to another Vectrix rider in Australia (postage costs only) as it is of no use to me, maybe he can salvage it for parts.
I've been running the bike for about a week now and everything seems to be fine and my confidence is growing again :-)
I still have one slight problem, when charging, the temperature rises to about 30c, before the board blew it never went above about 23c. I know that this is within the charging tolerances from what I understand from other users so I am not too worried. I'll have to recheck the battery connections when I replace the fuse in a few weeks - assuming it arrives by then !
Allan
Electric traction is the future.
Hi to everyone watching my progress with the replacement board.
It appears that the new board has the old software (62mph). Am I in the unique position of having the original software, then the newer software and then back to the original software again ?
A few quite unexpected things have happened as a result of this software reversal.
(1) The battery no longer 'hiccups' after about 25 miles (this used to signal the steady reduction in speed and performance for the remaining 10 to 15 miles).
(2) The performance, although marginally slower acceleration, has improved for the better and is far smoother than it used to be.
Best of all (3) The range has increased ! I know I am not dreaming this as I kept accurate range testing records over the years to watch the decline of the batteries over its lifespan. Today I went out to do some shopping : on the motorway I did 62mph for about 3 miles, I then drove at 40~50 mph for the remainder of my journey. I drove quite hard as I was not planing a big trip so range was not my concern. On the way home I realised that the bike was performing quite well and the range was approaching 29 miles with no drop off in performance and no warning lights. I decided to drain the battery to the first 'busvlt' warning (as I usually do with range testing). To my amazement I got 36 miles of range before the bike slowed to 25mph (no 'busvlt' warning). Previously with this type of driving style I only got 32 miles of range.
Later this week I am going to do a 30mph (maximum) range test and see what happens - this usually gets me 37 miles if I am very careful. I'll pop the result on here later.
One thing is for certain - I won't be installing the newer software again.
Does anyone else have any insights into this behaviour ?
Electric traction is the future.
The low voltage limit of the older software is lower, allowing you discharge deeper and at a higher rate
the downside is reduced battery service life
Matt
Daily Ride:
2007 Vectrix, modified with 42 x Thundersky 60Ah in July 2010. Done 194'000km
Hallo,
I'm working for the official VECTRIX Importer in Austria (MP-ecodrive GmbH). We have brandnew Motor Controllers and other spare parts in stock. In the last months we could help many customers with difficulties in organising spares, software problems and with pre delivery vehicles.
From deep conviction about electric mobility and as VECTRIX veteran we deal despite difficult times, especially with this topic.
If you choose the option to replace your Motor Controller, don't hesitate to contact us for a offer.
KR,
Gerald
Hi, thanks for the information. How much would a new MC Board cost ?
Electric traction is the future.
Hi Guys,
just a bit of an update
Allan kindly sent me this dead MC board for the cost of postage
I was able to repair it yesterday
Basically I used a dremell to cut away the burnt plastic, like I would for one of the phase connections.
The interesting part was electrically reconnecting the positive to the board, both for power for the bike, but mainly so the ceramic caps could do their job at keeping the voltage stable while the IGBT is doing it's switching
I soldered two eye crimp terminals onto the positive traces, after scraping off the conformal coating.
Today I put the repaired board back into service in a friends bike, whose MC had died (IGBT module on his board failed internally)
Incidentally, replacement IGBT modules can had fairly cheaply here:
http://www.ebay.com.au/itm/MITSUBISHI-PM300CLA-060-MODULE-1pcs-Refurbished-PM300CLA060-/111026348332?pt=LH_DefaultDomain_0&hash=...
Also, I am now selling replacement studs
Mine are made out of tinned copper (not steel), much the same as the terminals on the new MC versions
I hope this to be the final solution to MC boards burning out at the terminals
Matt
Daily Ride:
2007 Vectrix, modified with 42 x Thundersky 60Ah in July 2010. Done 194'000km
Good job!
How much are the replacement studs?
This information may be used entirely at your own risk.
There is always a way if there is no other way!
The IGBT's that you've posted are refurbs - is this ok ?
I will have to let you know when I install one, but it should be
The last one I bought was from china and I think that was second hand too
a brand new one is ~$40 more, if you're concerned that would be the way to go
I would be interested in what is involved in refurbishment
I have a few IGBT modules that have failed internally - not burnt out but the thermal cycling has caused the gates to become detached from the heatsink resulting in the over temp cutout being activated under acceleration, particularly at low speed
you don't normally see that failure mode till after 30'000km or more (the IGBT module used isn't designed for an automotive application with significant thermal cycling)
Given that many bikes are reaching that extent of use, I'm expecting to see a bit of a run of people with bad IGBT's
Daily Ride:
2007 Vectrix, modified with 42 x Thundersky 60Ah in July 2010. Done 194'000km
I have to get a quote on getting them tinned - but I'm looking at $8 - $10 per stud.
That would include a M5 bolt, and you have 3 choices of size:
16mm long for if you want to cut a hole in the board and bolt directly to the IGBT module
10mm long for if you want to just replace the original steel studs
28mm long for if you have had to repair a burnt out terminal and had to re-drill a hole in the copper tab coming out of the IGBT module
getting them made is surprisingly labour intensive
I'm getting copper tube cut and drilled on a lathe, then electroplated with tin
the copper studs I'm using have a conductor surface area of 107mm2, so should run cold (the battery interconnects on the nimh battery are 45mm2 for reference)
Daily Ride:
2007 Vectrix, modified with 42 x Thundersky 60Ah in July 2010. Done 194'000km
Let us know when they are ready, please. They'll go in the next time the MC board is out for some reason.
This information may be used entirely at your own risk.
There is always a way if there is no other way!
They're ready:
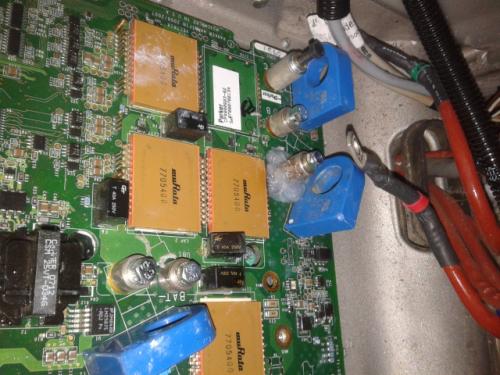
There's presently 3 sizes:
$7.50 - 10mm - can only be used on negative terminal and centre phase terminal
$8.50 - 16mm - for left and right phase terminals and the positive terminals, and any terminal where the PCB has been cut away
$9.50 - 28mm - for where a burnt out terminal has been repaired and a new hole had to be drilled in the IGBT module
Included is the correct size M5 bolt (between 10mm and 20mm longer than the stud), a pair of nordlock washers and if needed, a nyloc Nut.
the nyloc is only needed if you have cut away the backside of the IGBT module
I use www.auspost.com.au for shipping
the outer diameter of the studs is 12.7mm
Matt
Daily Ride:
2007 Vectrix, modified with 42 x Thundersky 60Ah in July 2010. Done 194'000km
Very nice!
What would you suggest as a preventative modification?
I think it might be best to drill / dremel out all 5 terminals, so that the board is gone and the terminals connect straight to the undamaged IGBT module.
So 5 x 16mm needed?
This information may be used entirely at your own risk.
There is always a way if there is no other way!
The Positive and negative connections can't be drilled out, regrettably, at least not until we can work out a good way to solder the new studs to the board
but the 3 phase terminals, dremmelling out would be the best
I mis-measured the required stud lengths - I forgot about the washer and spring washer between the stud and the PCB
so that's why the 10mm versions exist - you need minimum 12mm to clear the hall sensors (although you can use the 10mm ones, the lug on the wire just bends down.
the 16mm versions were supposed to be for when you dremel out the holes for direct connection to IGBT, but they actually need to be minimum of 18mm long.
the 28mm stud is the correct length (thankfully)
I'm waiting to see what kinda demand there is for these lugs before committing another $700 to making a second batch
Matt
Daily Ride:
2007 Vectrix, modified with 42 x Thundersky 60Ah in July 2010. Done 194'000km
I just discovered using a Panel drill for the phase connections is *way* easier and faster
http://www.ebay.com/itm/3Pcs-HSS-Steel-Large-Step-Cone-Drill-Titanium-Bit-Set-Hole-Cutter-4-12-20-32mm-/141300309767?pt=LH_Defau...
Daily Ride:
2007 Vectrix, modified with 42 x Thundersky 60Ah in July 2010. Done 194'000km
Pages