It is only a prototype....
... and there are a few things that need attention yet,
like it still needs a box...etc...
but here is the long awaited much anticipated
Can Bus Monitor for the Vx1...
If you like it please let me know.
It is only a prototype....
... and there are a few things that need attention yet,
like it still needs a box...etc...
but here is the long awaited much anticipated
Can Bus Monitor for the Vx1...
If you like it please let me know.
There are currently 0 users online.
I like it, A Lot, Amazing, Well done, I want one...Two actually. How much and when..How good would this be embedded into the Handle bar cover.. I have access to a 3D printer and lots of black ABS plastic.
Exceptional.
But what did it display when charging lol !
I'd buy two as well.
Several questions
Will you be selling them?
if so (and as I am ok with electronics)
1 will you be selling them as complete units
2 kits (parts ready to solder with i assume a pre-programmed pic)
3 schematics with source code ?
To be honest you have done the hard graft and I am sure many people here would love one of these and would also like to pay you for your efforts.
Well done... can i beta test it lol
Cheers
Chris
Wonderful! I need 2 of them for both Vectrix that I own.
Hi Everyone....
Thank you for the positive feedback, it is most welcomed; but, alot
of the credit has to go to Mik for doing the initial legwork and posting
all of the data/comments garnered from the Vx-1 CanBus. In all honesty
I probably would not have pursued this project without it.
My apologies for the poor quality video in the garage.
((what you see in the video is the maiden voyage/1st test run))
The display is formatted as follows:
Battery-"V"oltage "F"ront (Pack C Temp/sensor readings)
Buss-"A"mperes "R"ear (Pack C Temp/sensor readings)
...during charging the values are obtained from the charger (obviously);
and, during riding the values are obtained from the motor controller....
at least all of the documentation I have used as a reference indicates
this to be so.
I have as yet to work out any details but I was hoping to
make this available for sale soon... please stay tuned...
@ BigTony: Please PM me, thanks.
THAT
IS
AWESOME!
Brilliant, got to get me one of those
Regards,
Peter
-----------------------------------------------------------
Central Scotland
I was actually thinking about something with clips...
clips like a garage door opener has to clip/slip onto
the visor/sun screen of your cage vehicle... these would
slip over the black protruding rounded part...the shroud
over the dash, if you will ... presenting the display in more
of a heads up position....sort of similar to what OATNET
did with his CA mounting bracket but without having to remove
the wind shield.
That looks very nice, well done!
Is the trimpot used to dim the back-light?
This information may be used entirely at your own risk.
There is always a way if there is no other way!
+1 I would be interested in a few for both bikes
Trim pot is used to adjust the contrast... backlight is always on.
I suppose other display types are available so if one has a preference
please do so indicate as several are available. NewHaven is the
display manufacturer. It is good during the day, at night it can
be a bit bright (no pun intended)... I am still working out
details but a different display is certainly within consideration.
Also I refined my video'ing skills a little (very little) so a better
quality video of the CanBus Monitor is now available at:
http://youtu.be/OOm9PGWqZbs you can now actually see the
values change when charging. ...and I should probably mention
the data display is formatted as:
Battery-Volts Front-Pack-Temperatures Top/Left Top/Right Mid/L Mid/R Bot/L Bot/R
Battery-Amps Rear-Pack-Temperatures Top/Left Top/Right Mid/L Mid/R Bot/L Bot/R
Not wanting to take anything away from the efforts of others, but, this display does
offer the benefit of narrowing down the area of concern with a high battery
temperature reading/alarm at a glance.
Cheers.
Very clever... but... I have a couple of questions now having seen the latest video...
In normal riding mode, (battery discharging) current is drawn from the battery and so a sign convention would be helpful here (I'm not sure if there is a recognised standard for this sort of thing yet?). If not, I would suggest as discharge is 'depleting', then the current drawn ought to be indicated as negative current value; i.e. -123A from the battery. When you then use regen, the battery is replenished with charge; so display a positive current value; i.e. 54A. Just a thought! You may not have enough characters/segments remaining to show a +ve/-ve sign on the display?
When the charging part of the video is shown, it would seem that a current value of something like 111A at 135V is obtained, shortly after switch on, when normal charging mode is established - this is surely not the case! It looks like you're reporting the speedo needle position - i.e. 111km/h. The charge scale is (as far as I'm aware) to be read on the m.p.h. scale and divided by ten. So, 111km/h is 69mph so 6.9A charge current. I may be wrong but this is the way I understood it. To test my 'what I heard', we can take a nominal charge voltage of say, 135V x 6.9A charge current. This is 931 Watts into the battery which does seem a bit low to me so my information source/calculations may well be incorrect. Even if I allow for a charger efficiency of only 70%, then power in (from mains supply) would be 931/0.7 = 1330W and I thought they (both types) were 1.6KW input chargers (at max power).
Either way, it looks like there may need to be some more number crunching somewhere along the (canbus) line.
Very impressive nonetheless!
Drew
Drew
Thinking about it some more, it may be the case that the charge current is actually km/h divided by a factor of 10... this would mean 111km/h is 11.1A charge current at nom 135V. 11.1 x 135V= 1498W. 1.6kw input (at full whallop) gives a charger efficiency of approx 94% which seems more like it to me. It also means the charger only has to dissipate 100W of losses.
Can someone tell me if this is correct?
Thanks chaps.
Best wishes,
Drew
Drew
Thank you.
Thank you Drew it is a good point. The main intended focus
is on the battery temperature readings. The current magnitude
reading is put up more for 'data point' purposes than anything
else at this point in time; however, this is subject to change.....
please remember this is still only a prototype....
The next time I perform a charge I will place a current meter on the
input to the bike and report back. Also please be aware that I am
running a runt battery pack at the moment. I posted 3 cells jumped
in another thread... so this would follow for the increased power
demand on charge (11.1A). I must watch carefully when charging so as not
to overcharge my pack more than about 141v. In doing so the
pack has never reached a state of charge to allow the charger to
enter any of the other charging phases.... I have replacement cells
but have not had time to install them due to the time which will be
required to the get the pack and the extra cells to a nearly identical
state of charge..... (wish me luck on this one).
The pic's as promised. End of charge at 140V and 1"space".7 amperes ;-)
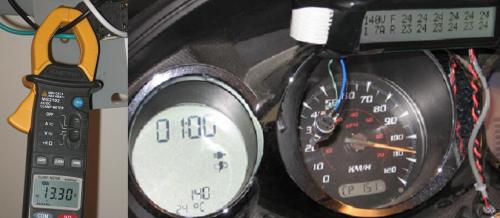
((like I said...it's still in prototype stages so that shall be corrected))
If you look at the photo of your speedo, the needle appears to be at 107km/h so could '1' 'space' '7' be '107' without the 'zero' being displayed (for whatever reason)? I think you may just be picking up on the needle position reading, as in; indicate a value of 107 on the display, rather than a current value output? Just a thought!
Also, where did you place the current monitor? AC input or DC output side?
Good work - and I fully appreciate that it's work-in-progress!
Best wishes,
Drew
Drew
Thanks Drew - um... the ICM (instrument cluster module) is a separate entity
from the charger and motor controller (as I understand it). So when obtaining values
from the CanBus (as is done in the Monitor circuit) during charging the only place
where that value can be obtained is from the Charger itself. (it has all the current
monitoring circuitry) The ICM also uses that value to position the Speedo needle
for an indication of the charge current.
Now, I'm still playing around with obtaining different values from the CanBus and
during charging it is redundant to display the charger current again on the Monitor
display but for my own confidence building I chose to do this during the
prototyping development. The zero was left out in formatting the display to
leave out the leading zero characters when displaying a value less than ten - so
when the display went to more than 100 and less than 110 then the display looked like 1 7.
That has been corrected to display a zero when the values fall between 100 and 110.... so now its 107.
I placed the current meter on the AC input to the bike. The display indicated more than 13 amperes.
Thanks I appreciate the input - it helps to work out some of the overlooked items.
Double post... ?
Really impressive work, congratulations!
I want one for my vectrix.
Do you have the original Nimh batteries? I've seen your vectrix going under 104 volts in a youtube video. That extreme undervoltage, allowed by early MC firmware, kills the NIMH battery very kickly. Try to keep it over 120 volts (115v min).
Very impressive - Arduino hardware? I'm trying to do the same thing, but with a slight difference - I'm trying to write values to the dash - specifically to the battery gauge - Counting amp-hours rather than voltage.
I take it you look for a certain ID in the string and strip the value? I'm stuck on the hardware for canbus to serial at the moment...
I don't have temperature sensors on the batteries (LifPo4) so things like phase current/battery current would be useful to read/intercept.
Just to avoid confusion, as far as I'm aware, ICM stands for Interface Control Module - see below... hence it does more than drive the instruments alone.
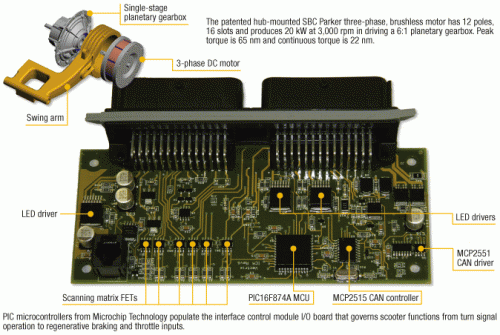
Ah, I can see why you did that now!
What is your mains supply voltage - presumably 120V? This would mean a power input of 120V x 13.3A = 1596W which sounds about right. (1.6kW charger) The DC output wattage will be less due to a few losses in the charger (wasted as heat, hence fans). If we took your needle position as an indication of a dc charge current of 10.7A at 140V dc, then that is a DC power of 1498W, giving a charger efficiency of approx 94%. It does seem to stack up. It would be great if someone could shove a current meter in the DC charge line and actually measure it! Sadly, I'm not about to tear into my daily commuter to find out. I'm sure Mik or The Laird may well have done this already.
Keep up the good work! I look forward to seeing how you get on with it!
Drew
Drew
During charging, the speedo shows the charge current (DC) multiplied by 10.
This information may be used entirely at your own risk.
There is always a way if there is no other way!
I hope to have them available before too long.
Yes, Nimh - just finished replacing a few cells and now have a full pack.
Sorry about overloading the battery - I will try to keep it over 115 but no guarantees.... ;-)
no - I figure since Vectrix used Microchip mcu's I would follow suit so that should I
ever need to I will already have the tools to work on the circuit boards...
@ Drew & Mik: Thanks! - I knew it was something like that....
Using the km/h scale rather than mph? That it what seems to be the case.
Drew
That's right: Divide the km/h value by 10 to get the A (DC) going into the battery.
This information may be used entirely at your own risk.
There is always a way if there is no other way!
Pretty much get the data out of the CanBus packet. I wasn't aware that a serial
buss existed. What is it used for? (comms to the LCD?)
Sorry, I wasn't very clear there. I am trying to figure out how to read the canbus packets - I am very interested in the hardware you are using - from your comments I would be assuming its a PIC, are you using one with inbuilt CAN communications, or are you using an interface to talk between the CAN bus and the PIC?
Ie. MCP2515 to SPI? Very interested...
Stupid triple post!
Stupid triple post.
Performed a calibration of the temperature display values
this weekend and now they are accurate +-3 degrees.
Here is the video: http://youtu.be/SvqIPHy9Wt8
Again my apologies for the poor quality video but
the sensor that was used to calibrate the firmware
was the bottom second from the right on the Monitor display....
I would prefer not to elaborate on the method used
to calibrate the firmware because it involves a fair
amount of exposure to the live battery buss; however, if
must absolutely know how it was done then please PM me
and I will share it with you.
Availability update: 3 to 5 weeks. Some parts have
been received and others are in shipping channels to me.
No further details have been worked out yet.
Once the initial few units have been successfully field
tested then more info will be available.
Here is the latest on the Vx-1 CanBus Monitor Prototype.
Just a short video (good quality this time) showing the
latest revision of firmware consisting of the start of
a ride and a few stopping points along the way. Somewhere
along the line somebody had asked about multiple screens - after
mucking around some... well, I will let the video speak it
for me.... have a look here: http://youtu.be/iU78ReSLe1I
I tried to select a switch rate that would not be
distracting; how did I do? Please let me know.
Thanks.
Pages